In the world of robotics, Offline Programming (OLP) has come a long way in a short time, and the global pandemic has jumpstarted more innovation. Industrial robots have evolved to collaborative robots (“cobots”) that work side by side with their human counterparts.
Big Trends in Offline Programming Software for Robot
Article from | Robotmaster
As technology advances, the industry is seeing many changes and enhancements to OLP. Let’s take a look at some of the future trends.
Versatility
When manufacturing facilities first started to use robots, the robots were massive, cumbersome, and task-specific. One robot did the welding, another the grinding, and another the assembly. Repairing, updating, and resetting required significant production downtime, and the robots needed a large footprint to operate safely. They were costly, required skilled technicians to operate them, and were often out of reach for small and mid-sized manufacturing operations. Robots were chosen for the task, and it was not uncommon to have several different robot brands within the same manufacturing operation. That required programmers to be versed in several different programming languages, which complicated training, parts management, maintenance, and software updates.
Companies wanted an all-in-one solution that could integrate with existing hardware. Rather than a series of piecemealed solutions to get the ideal setup, manufacturers and integrators sought out an integrated solution that works with various applications, especially in a high-mix, low-volume operation. This is where Offline Programming (OLP) software originated. When properly designed, OLP software can communicate to any robot brand, even older models, making the robot cell more flexible, and able to switch tasks without production downtime. As advancements in machine learning, artificial intelligence (AI), and the Industrial Internet of Things (IIoT) continue to push the capabilities of manufacturing technology, OLP software will continue to simplify and integrate robotic solutions. Companies that want to expand into new product areas can use OLP for programming, path creation, simulation, optimization, and validation.
Flexible OLP software allows companies to customize a solution that incorporates specific elements unique to the manufacturing facility, while taking advantage of the knowledge of others who have come before. This trend of collective wisdom is likely to continue.
Smart machines
As IIoT and machine learning become more sophisticated and user-friendly, users want robots with machine and robot intelligence embedded into the operating systems. Programming a robot using a conventional teach pendant is time-consuming, cumbersome, and subject to user error. Depending on the robot cell configuration, reaching all the points with the robot arm in teach mode can be impractical, or even dangerous.
When using an OLP, all the programming can be completed before the robot’s installation. The operation can be tested and issues resolved, so that installation and setup can be completed in a few hours or days rather than weeks. Program edits can be performed within the OLP software, rather than shutting down production to change points in teach mode on the pendant. The next function can be queued up while a current task is already in progress. With the right OLP and minimal training, anyone can program a robot, which is advantageous given skilled labor shortages.
Maximizing ROI is a primary objective in manufacturing, so, for example, it is far more cost-effective to have a welder embed their process experience into a powerful and easy to use programming software, than trying to find a programmer who is also experienced in welding.
Another advantage of OLP is the ability to troubleshoot, upload, and program from anywhere through the IIoT using a computer or tablet. Rather than shutting down the production line to determine what is wrong, advanced troubleshooting data and reporting can help programmers solve the problem quickly without an in-person trip.
In tandem with this, there will be a continued push for efficient analysis of all the data the robots generate, whether regarding errors, exceptions, or production reports. It’s not enough to produce the data; companies will need a means of analyzing, interpreting, and storing that data, bringing new challenges to both designer and user. While things like kinematic errors will continue to happen on the floor, the ability to pinpoint location, anticipate, and resolve the issue could significantly reduce production errors and downtime.
Simple and Accessible
There are a few OLP solutions in the market, each with varying strengths. Robotmaster® Offline Robot Programming Software has always strived to create a powerful robot programming solution while being as user-friendly as possible. Each software element needs a purpose, and users should be able to approach and use it confidently, regardless of their robotics experience level. Users do not need to be a robotic or CAD/CAM expert to utilize OLP software.
One way to provide a positive user experience has been through the use of open/flexible architecture, which allows users to have the best of both worlds, providing the advantage of the standard features, while allowing some of the functionality to be customized to meet their unique challenges.
Simulation
One of the advantages of OLP and CAD is building, testing, tweaking, and training a robot virtually, before it is installed in the factory. Advances in augmented and virtual reality will continue to push the envelope, and OLP will need to keep pace. Singularities and joint limits can be identified and solved in the simulation environment before the robot is installed. Areas prone to kinematic errors can be anticipated and optimized in engineering the robot cell prior to installation.
Users will continue to push for enhancements such as a user interface that provides graphical feedback to the programmer. Real-time data is key to answer common questions like, “Is the robotic path good to execute,” or “Why have I encountered path issues like singularities and collisions, or come across reach limits requiring edits to be performed?”
The more calibration that can be done before installation, the faster and more efficiently the robot integration can be completed and up and running.
Competitive advantage
OLP and robot integration has become a competitive market, requiring participants to innovate to maintain their competitive advantage. Robotmaster provides manufacturers and integrators the features needed to stay ahead of their competition; and that requires constant innovation. For example, in many manufacturing facilities, brand-agnostic OLP solutions will continue to be an invaluable sales tool, offering the ability to quickly format/adjust a solution to deliver an accurate time/cost estimate for customers.
Often, robot OEMs provide their own brand of OLP software which is compatible with their specific brand. However, a manufacturing facility that has multiple robot brands might be better suited to a brand agnostic OLP solution, an all-in-one solution to program all robot brands. At the same time, a custom OLP solution may not make sense in a facility using automation that doesn’t change a lot over time. There will always be the delicate balance between customization to meet a customer’s unique challenges and pricing the solution out of reach for small or medium manufacturers.
As manufacturing facilities become more familiar and comfortable with robotic integrated solutions that can enhance productivity, perform hazardous, tedious, or dangerous tasks, or automate repetitive operations so employees can use their skills elsewhere, the pressure to innovate, adapt, and evolve will endure. OLP continues to become more agile and robust, providing time saving solutions to many robotic integration challenges.
Learn more
Want to learn more about OLP? Read our previous article: Why use Offline Robot Programming Software and how to get started.
At Robotmaster, since 2001 we have been taking great pride in creating intuitive, easy to use Offline Robot Programming software with a team of professionals that understands manufacturing and design, kinematics, mathematics optimization, simulation, and CAD/CAM. Hypertherm is 100% employee owned, with over 1,800 associates.
The content & opinions in this article are the author’s and do not necessarily represent the views of RoboticsTomorrow

Robotmaster
Robotmaster, a Hypertherm Associates brand, is an offline, is an offline robot programming software that helps manufacturers maximize their robot's productivity with easy and efficient robot programming for a variety of applications such as cutting, trimming, milling, welding, spraying, polishing, sanding, grinding, deburring, and more. Robotmaster uses integrated CAD/CAM functionality to make robotic programming easy and intuitive for everyone, even first-time users.
Other Articles
Have You Looked at Automating Fabrication Tasks in the Past? Why Didn’t You?
Trane® Saves Over 80 Hours of Robot Programming Time
3 Benefits of Working With a Robotic Integrator
More about Robotmaster
Comments (0)
This post does not have any comments. Be the first to leave a comment below.
Featured Product
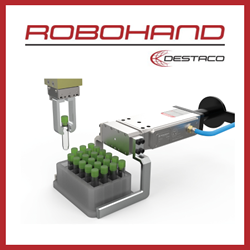