Guidance Automation helps Yantra replace Traditional Navigation with 'Natural Feature'
Guidance Automation, an award-winning pioneer in guidance, navigation and control technologies, has partnered with Yantra, a leading manufacturer and supplier of material handling equipment in India, to upgrade their vehicle navigation options to include industry-proven ‘natural feature’ navigation.
Yantra manufactures high quality automated guided vehicle (AGV) solutions, and prior to 2019, it solely used to work on path-guidance technology, where the robot or AGV would navigate according to the tape that was laid in the warehouse. They noticed a change in market demands as ‘natural navigation’ became a buzzword, and found that their clients were increasingly requesting adaptable vehicle navigation capability that didn’t depend on traditional line, wire or surface mark following where the environment was already feature rich.
In August 2018, both companies attended an automation exposition in Mumbai, where the Yantra team saw Guidance Automation demonstrate their laser-based ‘natural feature’ navigation system, ‘SCENE,’ which is capable of navigating by reference to existing features within the working environment. This means that no navigation marks are needed. Advanced 2D and 3D laser contour scanning and mapping algorithms are combined to generate a navigation map, which is then used to determine vehicle position during their operation.
Following the exposition, Yantra decided to accelerate their autonomous mobile robot development by partnering with Guidance Automation, transitioning away from the traditional tape-based technology to implement natural navigation.
The installation took place in 2019 and took just over a month, but despite time zone constraints, Rohit Dashrathi, Yantra’s CEO, emphasises that the support they received was excellent – and was the key differentiating factor of choosing Guidance Automation over their competitors. “We were able to be supported remotely, and Guidance Automation could take control of our robots, help us navigate and conduct the troubleshooting. “
“Many times in the industry, we have observed that once a solution is sold, you are often left on your own, especially for international transactions because distance and time zones play a great role. But Guidance Automation was extremely helpful and available to support us, even if it was over Whatsapp.”
Since implementing this technology, Yantra has found that the issues that had arisen from their traditional approach were eliminated, as the navigation didn’t rely on any external accessories, allowing the robots to navigate freely and easily. This, in turn, reduced their maintenance-related expenses by almost 20% due to needing no recurring work after the initial installation. Additionally, there was a 25% saving in manpower, as they were able to re-deploy two members of their workforce who were originally required to maintain the robotic setup.
Additionally, one of the most important factors for Yantra was the facilitation of simpler automation. There isn’t a need to ‘rip and replace’ facilities in order to embed automation technologies into existing processes, and Rohit wanted to ensure that the navigation technology was user-friendly and easy to comprehend. He explains, “After some initial training, Guidance Automation’s technology was straightforward to deploy, and we had no concerns, which added immense value to us as far as implementation at a customer-level is concerned.”
With a majority of companies looking towards automation, especially during COVID-19, Rohit explains that implementing natural navigation technology has given Yantra a good starting platform to develop solutions that are ‘pandemic compliant’. “We are deploying robots in healthcare systems for hospitals, but even simple tasks such as distributing medicines or food inside healthcare premises, these processes are still manual and require human intervention.
“During COVID-19, many companies are trying to formulate solutions that could automate this kind of material transport. And for the healthcare industry, traditional navigation methodologies wouldn’t work due to the size of the pathways. But Guidance Automation’s technology plays a major role because it is a plug-and-play deployment and doesn’t require additional accessories; it can be easily implemented in order to map the environment and start navigation.”
Dr Paul Rivers, CEO at Guidance Automation, commented on the partnership: “Our aim is simple – we develop advanced robotic vehicle guidance, navigation and control technologies to help accelerate autonomous mobile robot development. We enable our clients to keep pace with increasingly demanding market needs, and this is exactly what Yantra was looking to do.
“With our deep understanding of end user processes and working practice, we develop intelligent technologies that deliver on these needs and facilitate adaptation for the future. Guidance Automation looks forward to continuing our work with Yantra.”
Rohit Dashrathi concludes: “At Yantra, we are focused on client process needs and the provision of solutions that meet client goals. With Guidance Automation’s help and expertise, we have been able to successfully upgrade our vehicle navigation options and are already supplying enhanced AGVs/AMRs to our clients to meet the needs of their business operations. We look forward to exploring what technology Guidance Automation brings to the table going forward and expanding our relationship.”
Comments (0)
This post does not have any comments. Be the first to leave a comment below.
Featured Product
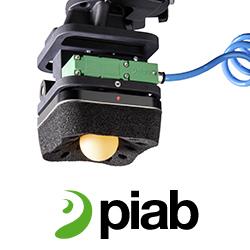