Enhancing Equipment Reliability: Implementing xPump – AI/ML Based Pump Monitoring & Predictive Maintenance System on Dry Screw Vacuum Pumps EH and Mechanical Booster Pump EH1200C
Introduction: The Need for Advanced Pump Monitoring Systems In the world of industrial equipment, maintaining operational efficiency is paramount. Pumps, especially vacuum pumps and mechanical boosters, play a critical role in industries such as semiconductor manufacturing, chemical processing, food production, and more. As these pumps age or operate in demanding environments, their performance can degrade, leading to unplanned downtime, costly repairs, and even production halts.
To combat these challenges, many industries are now turning to AI/ML-based monitoring systems that help predict pump failures before they happen. By implementing xPump—a state-of-the-art predictive maintenance system—equipment reliability can be drastically improved, reducing downtime, maintenance costs, and increasing overall system performance.
In this blog, we'll explore how the xPump AI/ML-based monitoring and predictive maintenance system can be implemented on Dry Screw Vacuum Pumps EH and Mechanical Booster Pump EH1200C to enhance equipment reliability and extend the life of these vital industrial machines.
What Is xPump?
xPump is a cutting-edge monitoring and predictive maintenance solution designed to improve the reliability of industrial pumps. By leveraging Artificial Intelligence (AI) and Machine Learning (ML), xPump continuously monitors key performance indicators (KPIs) of pumps in real-time, identifies abnormal patterns, and provides early warnings about potential failures. This early detection empowers maintenance teams to take proactive action, addressing issues before they escalate into costly problems.
With xPump, pump operators and maintenance teams can access real-time data, predictive analytics, and historical trends to make better, data-driven decisions regarding pump performance, service schedules, and spare parts inventory management.
Understanding Dry Screw Vacuum Pumps EH and Mechanical Booster Pump EH1200C
Before diving into the benefits of implementing xPump for these pumps, it's important to understand the function of the Dry Screw Vacuum Pump EH and the Mechanical Booster Pump EH1200C.
Dry Screw Vacuum Pumps EH
Dry Screw Vacuum Pumps EH are widely used in applications requiring low levels of contamination. These pumps are known for their ability to operate in harsh environments without the need for oil or other lubricants, reducing the risk of contamination in the vacuum system.
Their primary applications include:
Semiconductor Manufacturing
Pharmaceuticals
Food and Beverage Processing
Packaging
Mechanical Booster Pump EH1200C
The Mechanical Booster Pump EH1200C is typically used to enhance the capacity of a primary vacuum pump, providing a significant increase in pumping speed. These pumps are often used in conjunction with Dry Screw Vacuum Pumps to extend their performance range, especially in high-throughput operations.
Together, these pumps play a crucial role in maintaining the consistency of vacuum processes, ensuring the quality of the end product, and enabling greater process efficiency.
Why Implement AI/ML-Based Monitoring for These Pumps?
The Dry Screw Vacuum Pumps EH and Mechanical Booster Pump EH1200C are highly specialized and crucial components in vacuum systems. However, they are also complex machines that can experience wear and tear over time. Traditional maintenance methods, such as time-based servicing or reactive repairs after a failure, can result in unnecessary downtime and increased maintenance costs.
By integrating AI/ML-based pump monitoring systems like xPump, manufacturers can achieve a range of benefits that significantly improve equipment reliability and operational performance.
Key Benefits of AI/ML-Based Monitoring for Dry Screw and Mechanical Booster Pumps
1. Predictive Maintenance
The primary advantage of implementing xPump is its ability to predict when a pump is likely to fail. By analyzing historical and real-time data, xPump can identify patterns that are indicative of impending failures, such as unusual vibrations, temperature fluctuations, or pressure inconsistencies. This allows maintenance teams to intervene early, scheduling maintenance before the failure occurs and preventing unscheduled downtime.
2. Reduced Downtime and Maintenance Costs
xPump enables predictive maintenance by providing insights into the condition of pumps. This reduces the need for reactive repairs and helps avoid unexpected failures, leading to significant reductions in both downtime and maintenance costs. The ability to monitor pumps continuously in real-time means that maintenance schedules can be optimized, ensuring that parts are replaced only when necessary.
3. Extended Equipment Lifespan
By proactively monitoring the health of Dry Screw Vacuum Pumps and Mechanical Booster Pumps, xPump helps identify wear-and-tear symptoms early, allowing for timely replacements of components that are nearing the end of their lifespan. Regular maintenance and part replacements ensure that the pumps continue to operate at peak efficiency, thus extending their overall lifespan.
4. Optimized Performance
AI/ML algorithms within xPump analyze vast amounts of pump data, including pressure levels, temperature, vibration patterns, and more. By continuously monitoring these variables, the system provides detailed insights into how the pumps are performing, ensuring they operate at maximum efficiency. For pumps like the EH1200C Mechanical Booster, which are often working in high-speed environments, optimizing performance can have a significant impact on overall system output.
5. Data-Driven Insights
One of the standout features of xPump is its ability to provide data-driven insights. The system not only predicts failures but also offers suggestions on the optimal operation parameters. For instance, it can advise adjustments to operational conditions, such as pressure or flow rate, to improve efficiency or reduce wear. This level of insight helps equipment operators and managers make informed decisions that directly contribute to operational success.
6. Reduced Energy Consumption
Efficient pump performance also means reduced energy consumption. By ensuring that pumps are operating optimally, xPump helps minimize unnecessary energy expenditure. This can lead to substantial cost savings, especially in large-scale operations that rely on vacuum pumps running continuously.
Implementing xPump on Dry Screw Vacuum Pumps EH and Mechanical Booster Pump EH1200C
Step 1: Data Integration and Sensors Installation
The first step in implementing xPump is installing sensors on the Dry Screw Vacuum Pumps EH and Mechanical Booster Pump EH1200C. These sensors will collect data from various parts of the pumps, including temperature, pressure, vibration, and operational speed.
Step 2: Real-Time Data Monitoring
Once the sensors are in place, the xPump system begins to monitor the pumps in real-time. The data collected by the sensors is sent to a central control unit where it is processed and analyzed by the AI/ML algorithms.
Step 3: Predictive Analytics and Alerts
Using advanced algorithms, xPump will analyze the incoming data to detect any anomalies or signs of potential failure. If the system detects any issues, it will immediately alert the maintenance team with specific diagnostic information. This allows the team to take action before the problem escalates.
Step 4: Ongoing Optimization
With continuous data monitoring and periodic updates to the AI models, xPump ensures that the predictive maintenance system becomes smarter over time. As more data is fed into the system, the algorithms improve their accuracy, further enhancing the predictive capabilities and overall performance of the pumps.
Conclusion: Future-Proofing Pump Performance
Incorporating AI/ML-based predictive maintenance into the monitoring of Dry Screw Vacuum Pumps EH and Mechanical Booster Pump EH1200C ensures that businesses can optimize the reliability, performance, and lifespan of these crucial industrial machines. With xPump, companies can move from reactive to proactive maintenance, reducing downtime, cutting costs, and improving efficiency.
Is your equipment ready for the future? If you're looking to implement AI/ML-based predictive maintenance for your pumps, contact eInnoSys today to learn how our xPump solutions can help future-proof your operations and maximize your equipment's performance.
Take action now and enhance your equipment reliability with eInnoSys' advanced predictive maintenance system!
Featured Product
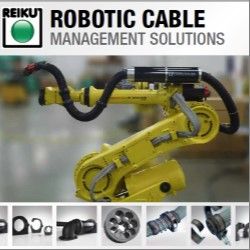