Trio combines machine and motion performance with new Flex-7 controller
Flex-7 features dedicated cores for high performance communications and motion. Trio will launch the Flex-7 Flexible Machine Controller at the SPS exhibition, Hall 1-Stand 360, taking place in Nuremberg, Germany, from 12-14 November 2024.
Trio Motion Technology is launching a new machine controller at SPS for large machines with control for up to 128 servo drive and robot axes over high speed EtherCAT. The new quad-core Flex-7 Flexible Machine Controller also increases machine automation capabilities by expanding network connectivity and data processing power, combining control flexibility and compact dimensions. Flex-7 features dedicated cores for high performance communications and motion.
The new Flex-7, a single controller for machine, motion, and robotics, precisely coordinates high axis counts while optimizing control and integration with expanded automation systems. The multi-axis machine controller is designed for large applications in manufacturing automation, packaging, and material handling.
Providing powerful machine control, Flex-7 features high speed Ethernet to give fast, reliable data exchange, optimizing communications with wider controllers and networks. This is achieved with two, 1Gbps Ethernet ports, compatible with Industrial Ethernet protocols including Ethernet/IP and Modbus TCP.
The Flex-7 increases control to 128 servo or robot axes and provides the high precision motion coordination that Trio is renowned for. Flex-7 achieves EtherCAT update rates as fast as 125µs for up to eight axes, and the full 128 axes are coordinated with update rates down to 4ms. Ensuring consistent motion synchronization for large machines, Flex-7 features <5µsec jitter and can control a wide variety of EtherCAT devices including servo drives and I/O.
A theme of Trio's Flex controller range is compact size, and this is continued with the Flex-7. Just 51mm wide, 147mm high, and 107mm deep, the DIN rail-mounted machine controller enables simple design integration and installation. Machine control functionality can be added directly with Trio's range of click-in Flexslice I/O modules that communicate with the Flex-7 using EtherCAT via the Ebus interface. Flexslice I/O slices give machine builders flexibility in adding required functionality while minimizing space and cost.
Flex-7's motion synchronization capability is powered by Trio's Motion-iX motion engine. Motion-iX is based on a command set for servo and robot axes, including multi-axis coordination in multiple dimensions, as well as numerous kinematic models for robotics. The motion engine is accessed through Trio's Motion Perfect software interface, and programming can be achieved with Trio Basic, designed to speed-up development through its English language-based approach, as well as IEC languages including ST and LD, as well as PLCopen.
Trio's Motion Perfect software enables fast set-up of servo drives and robots, and the software is also the center of machine control integration, providing easy management of peripheral devices and network connections. As well as designing a range of controllers, servo drives & motors, and I/O systems, Trio can also support machine builders with turn-key automation solutions, including HMI and SCARA robots.
"Trio's machine control approach provides machine builders with a motion-first automation solution. The Flex-7 extends this capability to builders of high axis count machines, giving them flexibility over machine control functionality, together with fast, powerful data processing and communications," says Trio's President, Tom Alexander.
"To create Flex-7, we've built on the popularity of Trio's pocket-sized, flexible controllers by extending motion coordination up to 128 axes and boosting processing power to enhance machine control. Supported by Trio's extensive motion library, the new Flex-7 will enable machine builders to quickly develop large, motion-first machines, with the machine control integration of their choice," adds Tom.
Featured Product
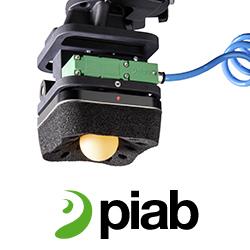