When industrial machine vision makes sweetness visible
Vision 2016 Trend Report: From hyperspectral systems, embedded vision and 3D technology to machine vision technology in detail
Vision once again impressively confirmed the development intensity of the machine vision industry. At the end of 2016, the focus was on hyperspectral systems, embedded vision and 3D technology at the leading global trade fair for machine vision. Apart from these themes, detailed machine vision also acted as a magnet for the public - from liquid lenses to photodiode sensors and made-to-measure high-end cables.
"Did you know that you can see the sweetness of a grape?" Manfred Pail, CFO of Perception Park GmbH, based in Graz (Austria), appealed to visitors to Vision 2016 with this unusual question. What is discussed here is hyperspectral machine vision, which works in the range between the visible and infra-red range (NIR/SWIR). According to Manfred Pail: "Every customer can develop their own applications themselves and integrate them into their own IT solution." A so-called 'manufacturer-neutral' plug-in system enables users to use the Graz company's data processing with all kinds of hyperspectral cameras. The software runs in real-time mode on conventional industrial PC graphics cards and in future on compact embedded vision systems.
Puchheim-based Stemmer Imaging GmbH is Perception Park's sales partner for Europe and Asia and is able to offer complete solutions including cameras with the Graz company's complete systems based on Chemical Colour Imaging (CCI) technology. "The idea lies in illuminating objects with over 100 different wavelengths and then analysing the reflections," explains Peter Stiefenhöfer, Head of Marketing and Public Relations. "Every material radiates the wavelengths back differently. The patterns enable, for instance, rotten parts of fruit and vegetables to be identified."
Quality and stability of the systems - it depends on this
Kathrin Martens of Basler AG observed one key point at VISION 2016: namely that all the reputable manufacturers' products are becoming more similar in terms of their installed hardware. "More than ever, it is about companies showing what they can offer in addition to the product," explains Kathrin Martens.
"It is not just about coordinated vision components, but also the quality and stability of the systems coupled with professional advice." The reliability and progressiveness of the manufacturer and his products therefore plays an increasingly important role for customers, which they could determine from the many live demonstrations.
Overseas expertise
There was also brisk business on the Edmund Optics stand, headquartered in Barrington, in the US state of New Jersey. The company's cooperation with the Canadian firm, Ottawa-based Pixelink, a specialist in autofocus cameras with liquid lens technology, attracted a lot of interest.
According to Project Engineer Rhiannon Jenkins: "The use of modular Cx lenses, produced by Edmund Optics, simplifies the integration of filters, liquid lenses and other optical elements for customers. When combined with the Pixelink camera exhibited, users can now easily and flexibly create a compact system, ideal for inspection systems with two different working distances."
The effectiveness of machine vision stands and falls with the optical sensors, presented by the Fraunhofer Institute for Microelectronic Switches and Systems (IMS). Among other systems, the Institute produces sensors for LiDAR (Light Detection and Ranging) systems, using which partially autonomous cars can locate and recognise other vehicles, cyclists, pedestrians or building sites. The sensors for LiDAR, developed in a standard CMOS process at the Fraunhofer IMS, consist of multiple photodiodes - known as Single Photon Avalanche Diodes (SPADs) - which are characterised by their exceptional sensitivity to light. These sensors enable objects to be detected more accurately.
According to scientist Jennifer Hess: "We are integrating and optimising these highly sensitive diodes into the 0.35 µm CMOS technology available to the IMS. This has the advantage that control as well as timing of LiDAR applications can be designed more effectively and durably." The initial systems using these sensors will go into series production in 2018.
In the past, many users have neglected the importance of cables for machine vision but this has now changed. Components Express, Inc. (CEI), based in Woodridge (Illinois), now produces made-to-measure standard cables, the quality and performance of which are the reasons why CEI has no fear of wireless image transmission, possibly using Wi-Fi. According to Steve Mott, Vice President: "Customers are attaching greater importance to the processing of extremely high volumes of data, which must be transmitted in real-time, with a high level of reliability and performance." CEI has been presenting its ideas and products at Vision for over ten years - according to Steve Mott with great success, as Vision is the perfect trade fair for business contacts.
Featured Product
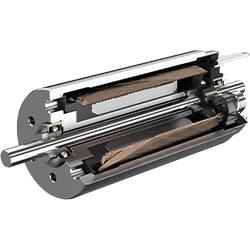
FAULHABER Drive Systems at the Robotics Summit & Expo in Boston from April 30 to May 1 in Hall C at Booth 534
Faulhaber will be presenting their drive systems for robotics and smart technology. Robots are versatile and can be found in many areas, for example, transporting goods, operating on patients or supporting the agriculture industry. With the help of robots, processes can be automated, the flow of materials optimized and employees relieved. Equipped with FAULHABER drive systems, these robots can take on tasks where the demands on function and applications are high.