DESIGN COMPETITION DEMONSTRATES PROMISING FUTURE FOR ADDITIVE MANUFACTURING IN SATELLITE DESIGN
Engineers from around the world leave jury of aerospace experts impressed with submissions
Minneapolis & Rehovot, Israel - Aug. 25, 2015 - Stratasys Ltd. (Nasdaq:SSYS), a leading global provider of 3D printing and additive manufacturing solutions, along with its subsidiaries GrabCAD and MakerBot, has announced the winners of the CubeSat Challenge after a month-long, highly competitive engineering competition.
Home to the world's largest community of mechanical engineers, the GrabCAD Community was invited to use 3D printing to rethink the design of a CubeSat, a standardized small satellite frame originally developed to allow university students to build low-cost satellites for research and education purposes. The goal was to design CubeSat structures that would be faster and easier to manufacture, and pack more utility into the very small volume that CubeSat designers had to work with. Participants had the chance to win prizes that range from MakerBot Replicator Desktop 3D Printers to cash to manufacturing services provided by Stratasys Direct Manufacturing.
Surpassing expectations, over 200 entries were submitted from all engineering disciplines and geographic locations. The submissions demonstrate the ability of additive manufacturing to vastly improve design over traditional manufacturing methods. "Engineers were able to reduce satellite structures from up to 50 parts down to two or three parts by using additive manufacturing," said Scott Sevcik, business development manager for aerospace and defense at Stratasys. "There were a number of very creative approaches to redesigning the satellite structure, and it was great to see several of the entries consolidate the build down to two or as few as one part. That highlights one of the most significant benefits of 3D printing a structure.
Reducing part count from 50 to three can make a significant impact on a manufacturers operations. It can:
· Reduce the amount of assembly labor, which saves cost and time.
· Reduce the risk of assembly error, or a late part delaying production.
· Reduce the risk of repetitive stress and other ergonomic injuries due to assembly effort.
· Simplify the supply chain, reducing purchasing, receiving inspection and other ancillary risks and costs.
First place was awarded to Paolo Minetola for his entry FoldSat, a design that uses geometries only possible with 3D printing. Second place went to David Franklin for his entry STRATASATT - FDM ONE, a design that illustrates customization using real CubeSat components. Third place went to Chris Esser with his entry Foldable Articulated CubeSat for Additive Manufacturing. His design featured 3D printed threads and six hinged panels.
Entries were judged based on technical requirements including feasibility, production, value and being optimized for additive manufacturing. The judging panel included experts from the aerospace and 3D printing industry:
· Dr. Jordi Puig-Suari, Cal Poly Professor and Co-Inventor of the CubeSat Standard
· Dr. Robert Hoyt, CEO and Chief Scientist, Tethers Unlimited Inc.
· David Espalin, Center Manager - W.M. Keck Center for 3D Innovation, University of Texas, El Paso
· Adam Hadaller, Mission Manager, Spaceflight Industries
· Patrick Price, Aerospace Additive Manufacturing Research Engineer, Stratasys
· Jesse Marin, Aerospace Project Engineer, Stratasys Direct Manufacturing
· Jonathan Cook, Director of Product, MakerBot
Visit the GrabCAD CubeSat Challenge results page to view the winning designs. The Aerospace vertical solutions team sponsored the CubeSat Challenge, with collaboration from GrabCAD, MakerBot and Stratasys Direct Manufacturing.
To learn more about the capabilities of Stratasys 3D Printers and Production Systems, visit the website. To participate in a GrabCAD challenge or inquire about sponsoring your own, visit the website.
Stratasys Ltd. (Nasdaq:SSYS), headquartered in Minneapolis, Minnesota and Rehovot, Israel, is a leading global provider of 3D printing and additive manufacturing solutions. The company's patented FDM and PolyJet 3D Printing technologies produce prototypes and manufactured goods directly from 3D CAD files or other 3D content. Systems include 3D printers for idea development, prototyping and direct digital manufacturing. Stratasys subsidiaries include MakerBot and Solidscape, and the company operates the digital parts manufacturing service, Stratasys Direct Manufacturing. Stratasys has more than 3,000 employees, holds over 800 granted or pending additive manufacturing patents globally, and has received more than 30 awards for its technology and leadership. Online at: www.stratasys.com or http://blog.stratasys.com
Featured Product
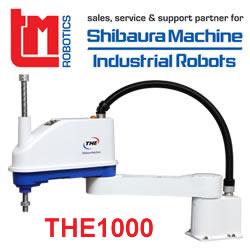
TM Robotics - Shibaura Machine THE SCARA range
The THE range from Shibaura Machine is an extensive line up of SCARA robots. Available in four arm lengths THE400 (400mm), THE600 (600mm) and the most recent THE800 (800mm) and THE1000 (1000mm), this range is suitable for assembly, handling, inspection and pick and place processes in varied industrial applications. The THE1000 boasts a 20kg payload capacity and an impressive 0.44 second cycle time, providing high speeds for processes with large components. In fact, the range has been recognised for as the price-to-performance leader compared to other SCARA models in its price range due to its impressive speed versus payload capacity.