Rockwell Automation enhances PlantPAx Process Automation System
Rockwell Automation extended the reach of its PlantPAx process automation system to integrate critical rotating assets, such as compressors, pumps, turbines and fans, giving users the ability to manage plantwide operations with a single platform.
November 15, 2011 - Rockwell Automation extended the reach of its PlantPAx process automation system to integrate critical rotating assets, such as compressors, pumps, turbines and fans, giving users the ability to manage plantwide operations with a single platform. The PlantPAx system combines the company's core process automation capabilities and technologies with those of partners and acquisitions to deliver an integrated control and information solution for customers.
Users now can tie intelligent motor devices into this unified-control architecture, making an immediate and measurable impact on asset availability, operational efficiency and energy management. The tight integration between process automation and motor control is especially beneficial in heavy industrial applications with considerable mechanical investments, such as: metals, mining, cement, power, oil and gas, water/wastewater, and pulp and paper applications.
PlantPAx system users will have access to diagnostic information on any device in the system from any location - including: motor control centers, drives, compressors, pumps, fans and instrumentation. Leveraging the EtherNet/IP network, engineers can monitor process conditions such as electric motor current, vibration signatures of key rotating assets and torque signatures of variable speed drives. This allows plant engineers to predict potential problems and help avoid equipment downtime - resulting in improved productivity and reduced maintenance costs.
Unlike other distributed control systems that require users to manually map data from motor control devices to the control system, the PlantPAx system mirrors the device memory, making data automatically available within the control system. Users can also setup applications in the PlantPAx system to collect and archive performance data from motor control devices into databases for analysis.
This convenient data acquisition provides cost savings throughout the lifecycle of the equipment. For example, bringing intelligent motor control devices into the PlantPAx system is useful in managing the performance of energy-intensive assets. Furthermore, since EtherNet/IP is the delivery mechanism for the PlantPAx system, users can avoid electrical hazards by accessing information remotely, helping personnel safely monitor, troubleshoot and diagnose motor control centers and other equipment. This saves time associated with suiting up with personal protective equipment and helps protect personnel from exposure to hazardous conditions.
In addition to integrating motor control devices into the control system, other key features with the PlantPAx system include:
EtherNet/IP network support for redundant systems and Device Level Ring network topology that provides a highly available EtherNet/IP network without any additional infrastructure costs.
Improved device integration and asset management as drives, for example, are now exposed via icons and faceplates in the visualization layer, and managed in the asset management layer to provide disaster recovery, automatic backup and restore of drive configuration, and change auditing.
Accelerated design engineering with initial sizing and architecture design, the creation of reusable engineering and template objects, and engineering and deployment tools for objects and diagnostics in the PlantPAx library.
According to Barry Young, analyst, ARC Advisory Group, "The PlantPAx system helps lead the trend in the convergence of power and process automation systems, which will result in improved productivity and energy efficiency for end users in: metals, mining, cement, power, oil and gas, and pulp and paper industries."
"To improve plant performance, our customers prevent unplanned shutdowns while protecting expensive machinery," said John Genovesi, vice president and general manager, Information Software and Process Business, Rockwell Automation. "Leveraging a single-network architecture to bring operational information from motor control devices into the control system helps engineers extend the life of their mechanical assets and improve their overall configuration, operation and maintenance experience."
About Rockwell Automation
Rockwell Automation, Inc. (NYSE: ROK), the world's largest company dedicated to industrial automation and information, makes its customers more productive and the world more sustainable. Headquartered in Milwaukee, Wis., Rockwell Automation employs about 21,000 people serving customers in more than 80 countries.
Featured Product
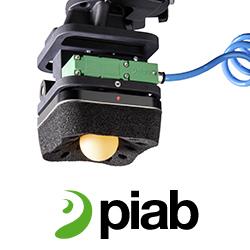