As part of an in-house robot build, optimizing the drive train that powers and controls each joint is vital to the robot’s performance. The most effective way of achieving this is by developing the drive train as a complete module.
The rise of modular robots and the importance of drive train design
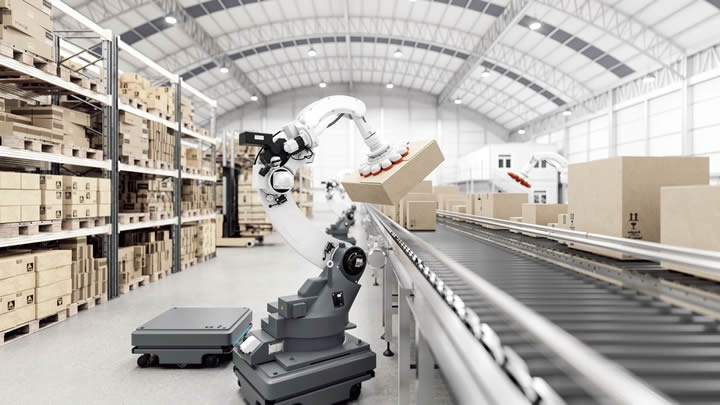
Roman Berger | maxon group
As the requirements for robots continue to become increasingly specialized to task, the advantages of modular robots are to the fore. The ability to change their form and configuration, thanks to a combination of modules, as opposed to a fixed body, gives greater flexibility. This means that a modular robot can be reconfigured, or customized, as often and as quickly as is required. And should the robot fail, a replacement can be rapidly, and economically, provided.
In particular, there’s been a marked change towards modular designs in the industrial robot class at the level of lightweight robots and cobots. These smaller designs, typically handling loads between 3kg and 16kg, lend themselves to specialization and the benefits of modularity. Their small size enables easier configuration, and for this payload range, there are a high volume of tasks that robots are required to fulfil. This is confirmed by reports in the growth of lightweight robots deployed, ranging from 20% to as high as 40% each year worldwide.
To facilitate the modular robot demand, there’s been a corresponding need for greater flexibility in robot control. Motion controller manufacturers and PLC manufacturers are increasingly offering kinematic libraries that enable robot control programming. This is allowing system integrators, as well as end users, ranging from car manufacturers to warehousing and delivery companies, to develop their own robots, instead of having to rely on dedicated robot manufacturers. The advantage is enhanced robotic control, more specific to their requirements, met with the flexibility to quickly respond to changing needs.
Motor design
Central to the increasing trend towards modular, lightweight robots, designed and built internally, is the need to power their kinematic motion. The motion system, or drive train, is responsible for moving and controlling each robotic joint. Just as a modular robot design must enable the flexibility to fulfil various specialized tasks, so too, the capability of the drive train has to match this need.
The motor itself is central to the drive train. To achieve the required high dynamic performance, necessary attributes include high torque density and low inertia, enabling rapid acceleration and deceleration. Smooth control of each robot joint is also essential, so the motor must ensure capabilities such as low cogging, minimizing micro ripples and jerks during motor rotation.
For lightweight robots, a compact motor is also essential, which further emphasizes the need for high torque density. A frameless design, like maxon’s EC frameless motor, enhances design integration, and its hollow shaft enables through routing of cables. Despite the motor’s small footprint, this design also answers the essential criteria of heat and energy efficiency.
The drive train
However, to optimize robot motion performance, not just the motor, but the complete drive train must be taken into consideration. The drive train, itself a module of the robot, typically comprises the motor, plus the gearhead, the encoder, which provides continual feedback on position and speed, as well as the motor’s position and speed controller. Like the motor, each of these components should be designed to enhance distinct performance criteria, yet the design of the drive train as a complete module is fundamental to optimizing motion performance.
This requires correct dimensioning, and crucially, correct sizing, in terms of meeting the required motion output values, such as torque, speed, acceleration, and position profile. Often, the specialized requirements of modular robots for each individual application also mean that customization of distinct motion components is also necessary. As these components perform together in concert, design changes to individual parts can have a subsequent impact on the operation of the motion system as a whole. Therefore, if customization to any aspect is required, treating the drive train as a complete module is a more effective way of optimizing both the motion performance as well as design integration.
To meet these objectives, the design stage should also include kinematic simulation. Creating a working, virtual model is vital to plan the robot’s motion path, ensuring that the desired kinematic profiles can be achieved, according to factors such as position, acceleration, and torque. Simulation is also crucial to ensure that the robot operates within safe limits for the protection of users, as well as the physical environment. This service can be provided by a motion designer like maxon, in conjunction with programming support for each axis of motion.
Optimizing design efficiency
Designing and simulating the drive train as a module also makes the development process significantly more efficient. Most significantly, it removes the time required to develop and test the performance, compatibility, and integration of individual drive system components. In addition, it reduces demand on procurement teams. As a combined result, robots can be brought online more quickly.
The alternative approach of procuring distinct components might be attractive from an initial cost perspective. However, the development time required for in-house drive train engineering can make this process less cost-effective long term.
The greatest advantage of working with dedicated motion engineering expertise though, is the improved motion performance that can be achieved. Not only can this partnership increase a robot’s capabilities, but a tried and tested approach to drive train development can also enhance reliability, minimizing downtime when the robots are deployed in the field.
When engaging a drive train designer, considering the impact that motion specification has on robot performance and design integration, ideally the motion engineers should be involved at the earliest opportunity. This will speed up development by minimizing the volume of required iterations, and will quickly help achieve a finalized design.
To find out more about maxon’s drive trains and engineering services for lightweight robots, visit https://www.maxongroup.com/en/market-solutions/mobility-solutions/robotics
The content & opinions in this article are the author’s and do not necessarily represent the views of RoboticsTomorrow
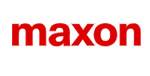
maxon group
maxon is a leading supplier of high-precision DC brush and brushless servo motors and drives. These motors range in size from 4 - 90 mm and are available up to 500 watts. We combine electric motors, gears and DC motor controls into high-precision, intelligent drive systems that can be custom-made to fit the specific needs of customer applications.
Other Articles
Automate 2025 Q&A with maxon group
Understanding Torque and Speed in Electric Motors
How Parvalux Is Helping to Develop the Next Generation of Conveyor Systems
More about maxon group
Comments (0)
This post does not have any comments. Be the first to leave a comment below.
Featured Product
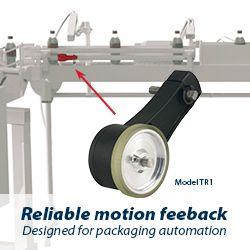