In this blog, you'll learn about these two lens types with key insights into their attributes and best-use scenarios in the world of embedded vision.
Prabu Kumar | e-con Systems
Embedded vision systems rely heavily on the capabilities of their lenses. The lens’s optical properties, such as its focal length, aperture, and field of view, dictate the clarity, depth, and breadth of the captured image. These parameters, along with sensor size and resolution, directly impact the system’s ability to analyze and interpret visual data. Hence, the type of lens, whether autofocus or fixed-focus, impacts the overall performance, especially in real-time processing scenarios.
So, understanding the differences between autofocus and fixed-focus lenses becomes critical. In this blog, you’ll learn about these two lens types with key insights into their attributes and best-use scenarios in the world of embedded vision.
What is a fixed-focus lens?
A fixed-focus lens comes with a determined and unchangeable focal length. Once set, this focus remains constant and doesn’t adjust based on changes in the scene or the distance of the target object. Such lenses are calibrated during the design or manufacturing phase for a specific application or distance, ensuring optimal clarity for that designated range.
Fixed-focus lenses are advantageous in scenarios that demand consistent and predictable imaging results. For instance, in industrial applications where objects are always presented at a consistent distance from the camera, such as quality control checks on an assembly line, fixed-focus lenses offer stability and repeatability.
What is an autofocus lens?
An autofocus (AF) lens can automatically adjust its focus based on the scene. Unlike manual focus lenses, which require a predefined focus set during the design or initial setup, autofocus lenses dynamically adjust to ensure the targeted subject or region of interest remains sharp. It is achieved through sensors and algorithms that detect the optimal focus point, allowing the lens to modify its focus in real time.
Autofocus lenses offer a high level of adaptability and accuracy in embedded vision systems, ranging from industrial automation to medical devices. They can continuously adjust to provide sharp images, whether an assembly robot inspecting objects of varying sizes and distances or a medical endoscope maneuvering the human body.
Selection criteria for autofocus lens vs. fixed focus lens
Proximity
The distance between the camera and the target plays a crucial role in selecting a lens, impacting the clarity and precision of captured images. Autofocus lenses are preferable for fluctuating distances, especially from a close 10cm to an endless range, allowing dynamic adjustments. However, a fixed-focus lens is better suited for a set distance, ensuring consistent imagery without any adjustments.
Example: For drones monitoring crop health from varying altitudes, autofocus is crucial to adjust to different heights, ensuring sharp imagery across diverse topographies. On the other hand, a tractor with a fixed lens-based camera setup monitoring seed planting might prefer a fixed focus for consistency, delivering uniform visuals of the seeding process without any variations.
Depth of Field
Depth of Field (DoF) refers to the span from the closest to the furthest point in clear focus. Cameras with autofocus lenses offer broader field depths than their fixed-focus counterparts. But sometimes, depending on the use case, a fixed-focus camera lens may be required, as some applications do not need broader field depths.
Example: For ultrasound imaging, a broader depth of field can capture a more comprehensive view of an organ or tissue, which might benefit from autofocus lenses, providing clinicians with a clearer overall picture. In contrast, a dermatoscope, used for detailed skin examinations, might employ a fixed-focus lens to deliver consistent, high-resolution skin surface images every time.
Type of lighting conditions
The type of lighting condition, as you may already know, directly influences the clarity of the photos. Autofocus lenses perform better under low lighting, with some fine-tuning to provide clarity. However, under brightly lit conditions, a fixed-focus camera lens can offer clear images within its preset range.
Example: In outdoor parking areas, lighting can change dramatically from daytime sun to nighttime artificial lighting or even shadowed areas due to buildings and trees. Autofocus lenses can adapt to these lighting shifts, ensuring clear license plate reads. However, covered parking garages with uniform LED lighting throughout might leverage a fixed-focus camera lens for stable image quality.
Rate of capture
Fixed-focus lenses typically work faster than their autofocus counterparts, as they lack the need for focus adjustments. Their design prioritizes speed over adaptability, making them efficient for certain tasks. Consequently, if an application demands fast image capture without interruptions, a fixed-focus lens is the recommended choice. It ensures consistent, rapid imaging without the potential lag of autofocus lens adjustments.
Example: In high-traffic indoor environments, such as stores during sales or holidays, kiosks equipped with autofocus lenses monitor customer movements and transactions. They adapt quickly to varied distances and lighting conditions, ensuring superior customer service. Conversely, outdoor kiosks face challenges like changing weather conditions and varied light levels. Here, fixed-focus camera lenses with faster capture rates capture document details or transaction information. This is important for maintaining consistent performance in conditions less controlled than indoors.
Adaptability
The camera lens’ versatility is also a deciding factor. Autofocus lenses perform better in low-light scenarios, with some customization. However, fixed-focus camera lenses can offer clear images within their preset range under brightly lit conditions, where light is stable and abundant.
Example: For MRI machines that might need to capture images of different body parts at varying distances, autofocus offers adaptability, ensuring clear visuals regardless of the target area’s depth. In contrast, a bone density scanner, which requires uniformity and consistent imaging parameters, would use fixed-focus lenses to maintain its precision.
e-con Systems offers fixed-focus and autofocus lens-based cameras
e-con Systems, with 20+ years of designing, developing, and manufacturing OEM camera solutions, can guide you in selecting the perfect lens that meets your application’s needs. We also offer lens mounting and adjustments to address problems like vignetting and color discrepancies. Furthermore, e-con Systems has a lengthy proven track record in offering customization for camera modules, covering ISP adjustments, firmware modifications, enclosure designs, and carrier board configurations.
Prabu Kumar is the Chief Technology Officer and Head of Camera Products at e-con Systems, and comes with a rich experience of more than 15 years in the embedded vision space. He brings to the table a deep knowledge in USB cameras, embedded vision cameras, vision algorithms and FPGAs. He has built 50+ camera solutions spanning various domains such as medical, industrial, agriculture, retail, biometrics, and more. He also comes with expertise in device driver development and BSP development. Currently, Prabu’s focus is to build smart camera solutions that power new age AI based applications.
The content & opinions in this article are the author’s and do not necessarily represent the views of RoboticsTomorrow
Comments (0)
This post does not have any comments. Be the first to leave a comment below.
Featured Product
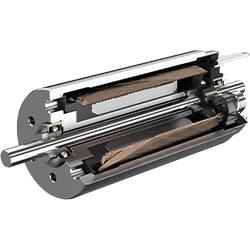