As both an industry and an entire class of technology, robotics changes and advances rapidly. Whether as a hobbyist or seasoned robotics engineer, you need to know each component inside and out. You should also know how to choose between several different variations.
How to Select the Right Motor for Your Robot
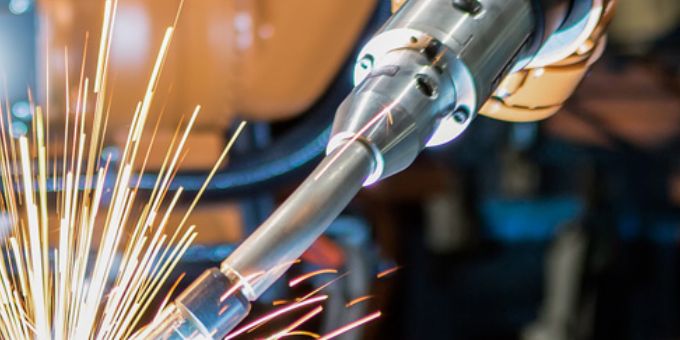
Megan R. Nichols for | Roboworld
This is the case with robotic motors. No matter how clever the articulation on a robot, you need the right product to give all that metal and plastic motion, power and range.
WHAT ARE THE TYPES OF ROBOTIC MOTORS?
There are multiple robotic motor categories. Each has subtypes and its own applications and advantages. Here’s a rundown of the types available today.
ROBOTIC ACTUATORS
There are three types of actuators:
- Pneumatic actuators: These use compressed air to function. With few moving parts, they’re reliable and easy to maintain. They lack the control over speed, position and precision offered by other types, but they’re an ideal choice for warehousing tasks like picking and stowing.
- Hydraulic actuators: These are a good choice for larger robots carrying heavy payloads. Instead of air, they use a pumped, oil-based fluid to provide motion. Although bulkier and noisier than other types, they’re accurate — at the expense of possible fluid leakages over time.
- Electric actuators: Electric motors translate a source of electricity into mechanical energy. These are the most common type in all robot categories today because electricity is a relatively plentiful resource. They also function well in robots of all sizes, are compact relative to their power output and are easier to maintain with virtually zero pollution.
Although electric actuators are the most common and serve the widest range of functions in robotics, they can pose a risk in environments containing explosives. They also require a more complex command system compared to other motor types.
ELECTRIC MOTORS
Within the electric motors category, there are several different kinds. This class includes the following types:
- Alternating current (AC) motors: Alternating current is available in common wall outlets. AC motors employ this abundant energy source to generate electromagnetic induction. Engineers favor AC mechanisms in situations that demand consistent velocity. However, they’re a rare sight outside of industrial-scale, high-torque robotics.
- Direct current (DC) motors: Instead of a wall socket, DC motors typically receive power from batteries. DC mechanisms appear in a wide range of sizes and provide highly variable load ranges, plus fast response times and mobility compared to plug-in models.
- Servo motors: Also simply called “servos,” including industrial servos, these are some of the highest-precision motors available. They support virtually instant error adjustments while in operation. If you need precise positioning plus high torque in a small package, these motors are excellent for robotic arms and other robot and cobot types. There can be a delay between motions when working with servos.
- Stepper motors: Stepper motors operate in very small increments to provide high torque while holding an object — as well as exact positioning for each step. Precision for these motors tends to be on the order of 0.01 degrees and 0.1 mm. The overall torque is similar to servo motors. Stepper motors are somewhat costlier to operate than other types regarding required electricity.
HOW DO YOU CHOOSE THE RIGHT MOTOR FOR YOUR ROBOT?
You can review the points above to narrow down your choice of motor for your next robotics project. Before you re-read all that, though, create a list of the can’t-miss features you need in your robot.
What task will it perform, and what’s your margin of error for its movements?
Study the regulatory environment closely to understand your tolerance for contamination, as well. Motor contamination isn’t just the leading cause of failure in motors — it’s also a threat to product quality in risk-averse manufacturing environments.
In other words, you wouldn’t necessarily match up a hydraulic actuator with high-finesse, high-cleanliness facilities like food or drug manufacturing.
These are the other main points to look for as you study various robotic motor types:
- Size to power ratio: At what scale are you building? Does the robot need to navigate tight quarters, or is raw power more important than size?
- Load limits: The drive types you choose for your robot need enough torque to deal with the expected loads it will carry.
- Accuracy: When the robot is in motion, what’s the tolerance for aberrant movements? Do you require a motor that provides on-the-fly, pinpoint error correction?
- Reliability: How well-staffed is your maintenance department? How often do you want to perform maintenance on your robot?
- Resource consumption: Not every robotic motor is as kind to the environment as others. Stepper motors consume power even in standby mode, but sometimes they’re the only choice.
A MOTOR FOR EVERY ROBOT
From the consumer level to large-scale robotics deployments, motors are everything. If you study the regulatory and working environments beforehand, you’ll quickly see there’s a motor type out there for every robotics project.
The content & opinions in this article are the author’s and do not necessarily represent the views of RoboticsTomorrow
Comments (0)
This post does not have any comments. Be the first to leave a comment below.
Featured Product
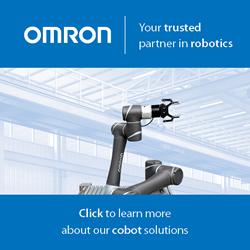