A sentin VISION system uses AI-based recognition software and can be trained using a few sample images. Together with a GigE Vision CMOS industrial camera from IDS and an evaluation unit, it can be easily embedded in existing processes.
Automate Image-based Inspection with Artificial Intelligence

Article from | IDS Imaging
High demands on products as well as high time and cost pressure are decisive competitive factors across all industries and sectors. Whether in the food or automotive industry - quality, safety and speed are today more than ever before factors that determine the success of a company. Zero-defect production is the goal. But how can it be guaranteed that only flawless products leave the production line? In order to make quality inspection as efficient, simple, reliable and cost-effective as possible, the German company sentin GmbH develops solutions that use deep learning and industrial cameras from IDS to enable fast and robust error detection. A sentin VISION system uses AI-based recognition software and can be trained using a few sample images. Together with a GigE Vision CMOS industrial camera from IDS and an evaluation unit, it can be easily embedded in existing processes.
High demands on products as well as high time and cost pressure are decisive competitive factors across all industries and sectors. Whether in the food or automotive industry - quality, safety and speed are today more than ever before factors that determine the success of a company. Zero-defect production is the goal. But how can it be guaranteed that only flawless products leave the production line? How can faulty quality decisions, which lead to high costs, be avoided? In order to test this reliably, a wide variety of methods are used in quality assurance.
A visual inspection with the human eye is possible, but it is often error-prone and expensive: the eye tires and working time is costly. A mechanical test, on the other hand, is usually accompanied by complex calibration, i.e. setting up and adjusting all parameters of both software and hardware in order to detect every error. In addition, product or material changes require recalibration. Furthermore, with the classic, rule-based approach, a programmer or image processor must program rules specifically for the system to explain to the system how to detect the errors. This is complex and with a very high variance of errors often a hardly solvable Herculean task. All this can cost disproportionately much time and money.
In order to make quality inspection as efficient, simple, reliable and cost-effective as possible, the German company sentin GmbH uses IDS industrial cameras and deep learning to develop solutions that enable fast and robust error detection. This is because, in contrast to conventional image processing, a neural network learns to recognize the features on the basis of images themselves. This is exactly the approach of the intelligent sentin VISION system. It uses an AI-based recognition software and can be trained on the basis of a few sample images. Together with a GigE Vision CMOS industrial camera from IDS and an evaluation unit, it can be easily embedded in existing processes.
Application
The system is capable of segmenting objects, patterns and even defects. Even surfaces that are difficult to detect cannot stop the system. Classical applications can be found, for example, in the automotive industry (defect detection on metallic surfaces) or in the ceramics industry (defect detection by making dents visible on reflecting and mirroring surfaces), but also in the food industry (object and pattern recognition).
Depending on the application, the AI is trained to detect errors or anomalies. With the latter, the system learns to distinguish good from bad parts. If, for example, a surface structure is inspected, see metal part in the automotive industry or ceramic part, errors are detected by Artificial Intelligence as deviations from a comparison with reference images. By using anomaly detection and pre-trained models the system can detect defects based on just a few sample images of good parts.
The hardware setup required for the training and evaluation consists of an IDS industrial camera and appropriate lighting. The recognition models used are trained using reference images. For example, a system and AI model was configured for the error-prone inspection of fabric webs in the textile industry. A difficult task, as mistakes can be very subjective and very small. The system camera for optimum image material of textiles and web materials was selected together with IDS on the basis of specific customer requirements. A GigE Vision CMOS camera (GV-5880CP) was selected, which provides high-resolution data, triggered with precise timing, for accurate image evaluation.
The system learns what constitutes a "good" fabric structure and knows already from a few shots of the fabric what a clean and flawless product looks like. For quality inspection, the image captured by the IDS Vision CP camera is then forwarded via GigE interface to an evaluation computer and processed with the recognition model. This computer can then reliably distinguish good/bad parts and highlight deviations. It gives an output signal when an error is found. In this way, slippage and pseudo rejects can be reduced quickly and easily.
Slippage is the proportion of products that do not meet the standard but are overlooked and therefore not sorted out, often leading to complaints. Pseudo rejects, on the other hand, are those products that meet the quality standard but are nevertheless incorrectly sorted out.
Both hardware and software of the system are flexible: For multiple or wider webs, additional cameras can easily be integrated into the setup. If necessary, the software also allows for re-training of the AI models. "Experience simply shows that a certain amount of night training is always necessary due to small individual circumstances. With pre-trained models from our portfolio, you need fewer reference images for individualization and post training," explains Christian Els, CEO and co-founder of sentin. In this case, the images show the structured surface of a fabric and a small anomaly on it, which was filtered out in the image on the right:
Anomaly extracted from a recording of a substance – sentin GmbH
Camera
Extremely accurate image acquisition and precise image evaluation are among the most important requirements for the camera used. Perfectly suitable: The GigE Vision CMOS camera GV-5880CP. The model has a 1/1.8" rolling shutter CMOS sensor Sony IMX178, which enables a very high resolution of 6.4 MP (3088 x 2076 px, aspect ratio 3:2). It delivers frame rates of up to 18 fps at full resolution and is therefore ideal for visualization tasks in quality control. The sensor from the Sony STARVIS series features BSI technology ("back-side-illumination") and is one of the most light-sensitive sensors with a low dark current close to the SCMOS range (Scientific CMOS). It ensures impressive results even under very low light conditions. Thanks to the sensor size of 1/1.8", a wide range of C-Mount lenses is available for the GigE Vision camera model GV-5880CP. "In addition to resolution and frame rate, the interface and the price were decisive factors in the decision for the camera. The direct exchange with the IDS development department has helped us to reduce the time needed for camera integration," says Arkadius Gombos, Technical Manager at sentin. The integration into the sentin VISION system is done via GenTL and a Python interface.
The GigE Vision camera GV-5880CP from IDS ensures precise image acquisition and accurate image evaluation when inspecting fabric webs – sentin GmbH
Conclusion
Automated, image-based quality control with Artificial Intelligence offers many advantages over human visual inspection or conventional machine vision applications. "In AI-based image interpretation, the aim is to create images on which humans can see the error, because then the AI model can do it too," concludes Christian Els. The system learns to recognize the requirements of the product similar to a human being. But the human brain is beaten at any time by an artificial intelligence in terms of consistency and reliability. Even if the brain is capable of remarkable peak performance, an AI can recognize much more complex error patterns. The human eye, on the other hand, cannot stand up to any camera in terms of fatigue and vision. In combination with deep-learning recognition software, the image processing system therefore enables particularly fast and accurate inspection. Depending on the application, image acquisition and evaluation can take place in just a few milliseconds.
The system can also be applied to other areas such as surface testing. Similar applications are e.g. the testing of matte metal/coatings surfaces (automotive interior), natural materials (stone, wood) or technical textiles such as leather. Scratches, cracks and other defects on consumer goods can thus be detected and the respective products sorted out. Exclude quality defects and produce only “good stuff” - an indispensable process within the framework of quality assurance. IDS cameras in combination with the deep learning supported software of sentin GmbH significantly optimize the detection of defects and objects in quality control. This allows the personnel and time expenditure for complaints and rework, as well as pseudo rejects, to be significantly reduced in a wide range of industries and areas.
The content & opinions in this article are the author’s and do not necessarily represent the views of RoboticsTomorrow

IDS Imaging Development Systems Inc.
World-class image processing and industrial cameras "Made in Germany". Machine vision systems from IDS are powerful and easy to use. IDS is a leading provider of area scan cameras with USB and GigE interfaces, 3D industrial cameras and industrial cameras with artificial intelligence. Industrial monitoring cameras with streaming and event recording complete the portfolio. One of IDS's key strengths is customized solutions. An experienced project team of hardware and software developers makes almost anything technically possible to meet individual specifications - from custom design and PCB electronics to specific connector configurations. Whether in an industrial or non-industrial setting: IDS cameras and sensors assist companies worldwide in optimizing processes, ensuring quality, driving research, conserving raw materials, and serving people. They provide reliability, efficiency and flexibility for your application.
Other Articles
2D cameras for positioning and inspecting ultra-fine wires in semiconductor production
Picking the right chart - (Semi-)Autonomous surface and underwater mapping for rivers and lakes
Pallet by pallet - Intelligent robotic vision system destacks up to 800 objects per hour
More about IDS Imaging Development Systems Inc.
Comments (0)
This post does not have any comments. Be the first to leave a comment below.
Featured Product
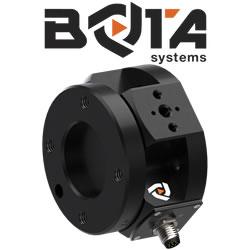