With solutions that enable intuitive and harmonized programming of robots from a wide range of manufacturers using pre-developed programming templates, effort and costs are reduced considerably. This makes their use attractive for more and more companies.
Standardized Robot Programming - From Lean Entry to Complex Applications
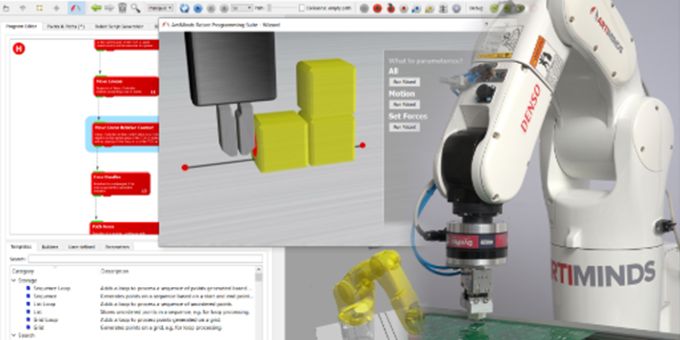
Article from | ArtiMinds Robotics GmbH
Today, robots can already do more than one might think. You just have to “teach them.” But it is exactly this teaching, i.e. robot programming, that is the reason why many companies shy away from using robots. Small and medium-sized companies dread the large programming effort, while large companies are always troubled by the lack of standardization. With solutions that enable intuitive and harmonized programming of robots from a wide range of manufacturers using pre-developed programming templates, effort and costs are reduced considerably. This makes their use attractive for more and more companies.
Programming languages of robots are not only complex, but also individual for each robot model. Thus, they are taught in extensive training courses. This has consequences: Small companies often commit themselves to one manufacturer and do not change so easily. Large companies have teams of experts, but each of them can only set up and operate the robot from a specific manufacturer.
Alternatively, companies outsource the programming of robots directly to external suppliers. Subsequent changes to the source code – no matter how small – are then only possible with outside help. Thus, the main costs do not come from the acquisition of the hardware but rather from the creation of the software as well as later adjustments and maintenance. This is particularly problematic if the robot – in its actually ideal field of application – is to be used as a flexible automation device, i.e. if it is to be repeatedly adapted to individual tasks. Companies that regularly bring new products to the market in smaller quantities could benefit immensely from automation aids if it were not for the hurdle of complex programming.
VISUAL PROGRAMMING OF VARIOUS ROBOT TYPES
We at ArtiMinds Robotics have developed our Robot Programming Suite (RPS) for this purpose. The software allows intuitive programming of robots of all well-known manufacturers as well as of all compatible peripheral hardware such as electrical or pneumatic grippers and tactile or optical sensors. Programming is no longer done via lines of code, but graphically via drag and drop with the aid of pre-developed building blocks. There is no need for programming expertise. Users simply select the hardware components used for their current project. To program the individual application, they then use a selection of over 60 templates stored in the library. The library contains blocks for simple robotic movements as well as blocks for force-controlled alignment, for camera-based search movements and for PLC communication.
This makes the software equally interesting for those looking for a lean entry into robotics as well as for companies that have to implement complex tasks. After the selection of the respective template, a wizard, a digital assistant so to say, guides the user iteratively through the steps of adaptation to the individual production conditions. Programs created in this way can be tested in the software. Using these simulations, the user can check directly whether the robot can, for example, approach all points in the work area, whether TCP or tooling need to be adjusted, whether collisions occur and much more.
The code is then compiled in the native robot language of the selected hardware and loaded onto the robot controller. Now it can be tested under real conditions and can be optimized further. By the way: already existing code can be integrated into the RPS to be reused.
ROBOTS ARE MORE CAPABLE THAN ONE MIGHT THINK
Force-torque-based control engineering opens up areas of applications for robots that would have been unimaginable with conventional programming and realistic effort, for example, the insertion of flexible cables in connector assembly. A flexible cable is gripped by the robot, measured by a camera system and then inserted into the hole, e.g. using a combination of spike and spiral search. A tensile test then ensures that the cable is placed correctly.
Experts estimate the time required to develop this solution using textual programming to be about a hundred times longer than their programming approach. In addition to electronics production, there are also applications in mechanical assembly, e.g. joining parts with low tolerances, setting plastic clips, seals, plugs or rivets, gear and engine block assembly or positioning and tightening screws. Today, these activities are often carried out by hand, especially in the case of small production lot sizes.
ArtiMinds has also gained experience in surface treatment: When grinding and polishing painted surfaces, a camera analyzes the surface of products, detects defects and polishes them with force-moment control. For this, a path can be created out of a CAD model connected to a force-movement template. But also grinding and deburring of edges or corners, gluing or paint application and material testing are feasible applications in this industrial sector. There are also numerous applications in quality control and inspection, handling and packaging as well as laboratory applications.
DATA ANALYSIS AND MACHINE LEARNING
In this way, already today completely new applications for robots can be realized, such as through hole technology (THT) assembly, in which the insertion holes are found via spiral or spike search (see use case below).
After configuration and testing on the real model it is often helpful to evaluate process data in order to optimize the process. During the operation of a robot a large amount of data is generated. The Learning and Analytics for Robots (LAR) tool collects this data and makes it available to users in a clearly structured form. In this way, values suitable for the respective template, used in the robot program, can be displayed and evaluated systematically.
In the case of THT assembly, for example, the user can have the data displayed for spiral position searches. If the user finds that the starting position at which the robot starts to search for holes is not selected optimally, he can adjust the parameters of the respective programming block in the RPS accordingly. In this way, processes can be optimized with little effort, whether to shorten production times, improve quality or make the entire program more robust.
CONTINUOUS DEVELOPMENT
The building blocks offered are of course developed further according to user requirements. Dr.-Ing. Andreas Hermann, Team Leader Advanced Robotics, adds, “In addition to constantly expanding the list of supported peripherals, we are constantly working on adding new intuitive and powerful functions to the software that make programming even more efficient and open up new areas of application.”
Here, ArtiMinds Robotics is continuously working on making new hardware available in its Robot Programming Suite. In addition, we not only support our users with software for robot programming and analysis, but also offer services.
Hermann emphasizes, “At the end of a customer project, the clean transfer of technology and knowledge is always important to us. We provide our customers with all project files so that they can make as many changes as possible independently in the future. In the case of other service providers, external help is often needed for the next small change, but this is different with us.” The robotics experts are also particularly interested in cooperative ventures in which they can open up and further develop innovative fields of technology together with customers.
EXEMPLARY USE CASE: THT ASSEMBLY
In THT assembly, electronic components with wire connections (e.g. ICs) are inserted into contact holes of a printed circuit board and soldered subsequently. The number of wire connections can vary from a few to several hundred contacts. Robot-assisted insertion of such a component without damaging the wire connections is anything but trivial. If individual contact wires are bent or the board is not positioned exactly, conventional automation systems reach their limits. It is necessary to find the exact position of the holes and to then insert the component sensitively.
There are various selection options for this in the programming blocks. In the case of spiral search, for example, the robot places the component at a defined position on the circuit board and then “pushes” it carefully over the board in a spiral until the correct position is found. Now the component is pressed in with force-moment control. For highly sensitive wire connections, an alternative procedure is to lift the component repeatedly and to carefully place it on the new position of the board until the correct position is found (spike search).
The programming blocks can also be used to implement solutions in which single pins of a module are inserted at an angle and all wire connections are gradually “threaded” into their final position by tilting them. Realizing these force-torque controlled solutions using textual programming involves a great deal of effort. With the RPS, on the other hand, even nonprofessionals can find a solution in the shortest possible time.
The content & opinions in this article are the author’s and do not necessarily represent the views of RoboticsTomorrow
Comments (0)
This post does not have any comments. Be the first to leave a comment below.
Featured Product
