Many companies make mesh network products for home Wi-Fi systems. Those are indeed valid and popular applications, but there are ample opportunities to use mesh networks for robotics, too.
Readers Choice 2020: Using Mesh Network Applications for Robotics
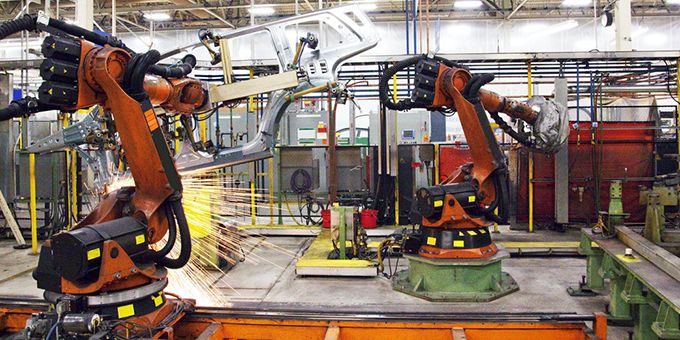
Kayla Matthews | Productivity Bytes
Mesh networks enhance the reach of radio signals when a group of compatible devices work together and branch off of each other.
Many companies make mesh network products for home Wi-Fi systems. Those are indeed valid and popular applications, but there are ample opportunities to use mesh networks for robotics, too. Here are four examples worth exploring:
1. Ground Robots for the Military
As robots become more advanced, the opportunities increase for militaries to use them in their operations. The U.S. Army decided to use a mesh networking system for a medium-sized ground robot called the Man Transportable Robotic System Increment II (MTRS Inc II). In October 2017, the organization gave Endeavor Robotics a $100 million contract to build 1,200 of the robot platforms.
The main advantage of mesh networks for this equipment is that they let single network nodes function as part of a broad infrastructure. Thus, there's no risk of a single communication point going down and causing a major outage.
2. Underground Search Operations
The Defense Advanced Research Projects Agency (DARPA) is experimenting with new opportunities in underground robotics through a multiyear contest called The Subterranean Challenge — SubT for short. For the first leg of the competition, participants had to guide their robots through underground tunnels ranging from 2.5 to 5 miles in length.
DARPA officials positioned objects within the tunnels, and participants competed in a race to find them via 3D maps generated by the robots. Team Explorer, the first-place winner of the event, used a hybrid approach for underground communication between its wheeled robots. The machines formed up to 10 network nodes on command, creating a mesh infrastructure after dropping ranging-radio anchors.
Many of the other participating teams used mesh technology, too, selecting it as the best option when other forms of underground communications became patchy. Team PLUTO, for example, wanted fully autonomous robots. Their machines used this networking option to communicate with each other when in range, plus send data to the base station.
The outcomes of this DARPA competition could pave the way for more capable robots suited to find things underground, thereby boosting safety by letting humans avoid doing this dangerous but often necessary job.
3. Mobile Robots for Warehouses
The rise of the Industrial Internet of Things (IIoT) highlighted a related segment known as the Internet of Robotic Things (IoRT). The IoRT uses smart technology integrated into a robot or the devices around it. Then, a robot can monitor events in the environment and make changes as needed, even manipulating connected machines based on real-time happenings. Users can operate whole fleets from single control centers, too.
Scientists investigated a mixed-architecture approach that relies on mesh networking when appropriate. The team set their sights on mobile robots, knowing communication lapses could make the machines stop moving or otherwise behave unexpectedly.
The researchers knew that any worthwhile system must deliver broadcast traffic at low latencies and found that standard wireless infrastructure did not always achieve that goal. Their findings and a proof of concept demonstrated that using a combination of an enterprise-grade Wi-Fi network and mesh gave the performance required to keep mobile robots operating smoothly in warehouses.
4. Security Robots
Many countries use use mobile security robots to supplement humans who patrol the surroundings on foot, horseback or in cars. Mesh networks for robotics can help such equipment work reliably. One example is the Sharp INTELLOS A-UGV outdoor security robot. It uses a mesh solution from the Rajant Corporation to capture audio, video and environmental information, then sends it back to a control center.
The robot uses Light Detection and Ranging (LiDAR) to measure variable distances. There is also an optional feature to detect toxicity levels. That means, in addition to protecting people by monitoring highly trafficked areas, the bot can handle repetitive tasks that may pose dangers to humans. Moreover, since the machine can roll over uneven surfaces, it's a smart choice for outdoor environments.
5. Mesh Networks Unlock Robots' Potential
These examples give a glimpse into how this type of networking helps robots perform more dependably while maintaining a steady connection — even in challenging conditions.
Robot development professionals should stay tuned to similar developments, particularly as customers continue exploring different ways to deploy robots and seeking consistent results no matter the task.
The content & opinions in this article are the author’s and do not necessarily represent the views of RoboticsTomorrow
Comments (0)
This post does not have any comments. Be the first to leave a comment below.
Featured Product
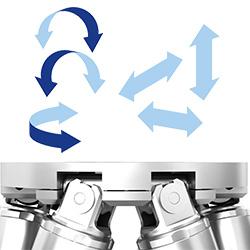