Industrial robots offer increasingly compelling opportunities to help companies get more done and promote consistency in the workplace. Robot safety is another area of concern, especially since robots can reduce some of the risks that cause accidents.
How to Improve Worker Safety Around Robotics
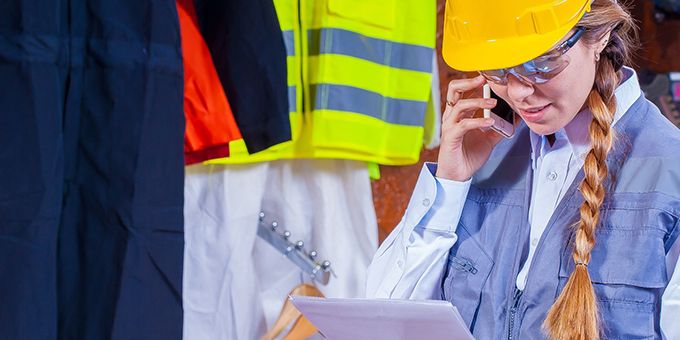
Kayla Matthews | Productivity Bytes
Industrial robots offer increasingly compelling opportunities to help companies get more done and promote consistency in the workplace. Robot safety is another area of concern, especially since robots can reduce some of the risks that cause accidents.
However, merely investing in a high-tech machine is not enough to enhance safety. Managers must also take purposeful steps to meet that goal. Here are six ways they can do that.
1. Design the Work Area for Robots
Some company leaders decide they're ready to purchase robots but don't think far enough ahead when it comes to designing the factory floor to accommodate robots and keep workers safe. Planning the proper design before bringing a new robot onsite should help increase success.
For example, considering the setup for a workspace with robots means choosing the right kind of robot cell and where to locate it. Employers must also envision the flow of traffic through the workplace and think about how to maintain the necessary distance between workers and machines.
2. Practice Machine Safeguarding
Machine safeguarding encompasses a wide variety of options such as laser guides, features that lock parts of the robot while someone performs maintenance and more. If company decision-makers are ready to implement robotics in the workplace, they should feel obligated to also look at the products and techniques that allow for machine safeguarding.
The Occupational Safety and Health Administration (OSHA) reports that a lack of machine safeguarding is one of its most frequently cited violations. Moreover, that violation appeared four times on a recent list of the largest monetary penalties given in a particular year. Therefore, failure to practice proper safeguarding for robots in the workplace could prove both dangerous for workers and costly for companies.
3. Understand How Robotic Applications Impact Safety
The wider availability of cobots substantially opens the possibilities for deploying robots in the workplace. Many people mistakenly believe that these machines are inherently safe because manufacturers build them to operate around humans. However, that isn't true.
Technical specifications are available that discuss the maximum allowable force, power and speed associated with using a cobot safely. Managers must also take into account how not all tasks are best suited for cobots or other kinds of industrial robots. Plus, even those that are good matches require careful considerations for keeping people safe while getting work done.
One of the advantages of cobots is their portability. Users can move cobots to other parts of the factory and set them up to do new tasks in a matter of minutes. However, managers must perform new safety assessments for each new job handled by a robot. Additionally, they need to account for the possible risks involving people moving cobots to different sections of a work area.
4. Improve the Visibility of a Mobile Robot's Path
Many companies purchase mobile robots that move around the factory floor to assist with bringing components or finished products to their intended destinations. These machines typically have sensors, turn signals and other integrated features to improve safety. However, company personnel should also do all that's in their power to keep people safe.
Statistics say that 51,550 workers get hurt or killed each year while doing warehouse jobs. The reasons behind those incidents vary, but many issues occur when employees are in the wrong place at the wrong time.
Safety paint is a low-cost, highly effective way to mark the path of a mobile robot to decrease the likelihood that a worker walks into it. Factories should also adopt a system that uses colors to warn of certain hazards so that people associate them with messages.
5. Train Workers Thoroughly and Regularly
Anyone who will potentially encounter robots in the workplace must receive training that addresses the most likely risks and how to mitigate them. Training workers to do tasks in the company of robots requires a detailed approach that gives people updated material as the machines become more advanced or the ways a company uses them change.
Employees should receive supervision until they feel comfortable working around the machines. Having channels they can go through to get questions answered or report concerns is also a smart move regarding safety.
Data indicates that human error is one of the top causes of injuries related to robotics in the workplace. Thus, if companies take training seriously from the start, as well as view it as an ongoing process, those things can help employees and employers reap the benefits of these machines without compromising safety.
6. Become Familiar With Robot Safety Products
Robotics engineers are progressively making robots safer as technologies improve. However, some companies provide customers with safety solutions related to automated equipment. One of them is Pilz, which addresses the whole machine lifecycle with its products. Also, Dynatect provides safeguarding options plus protective covers, giving customers a library of more than 50,000 products.
Similarly, companies should learn about companies in the robotics sector that specialize in automation for Industry 4.0. For example, Comau sells a complete assortment of robots, including cobots and wearable options.
7. Take Robot Safety Seriously
These six suggestions are crucial for companies that want to immediately and continually prioritize robot safety. In addition to following them, companies should remember to build safety into the company's culture and make it a team effort.
The content & opinions in this article are the author’s and do not necessarily represent the views of RoboticsTomorrow
Comments (0)
This post does not have any comments. Be the first to leave a comment below.
Featured Product
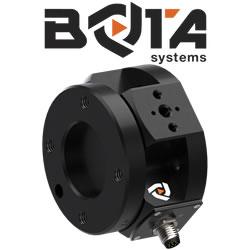