In order to become more efficient and work more quickly but at the same time protect the health of their employees, it is worth investing in ergonomic lifting devices.
Ergonomic Under Load: Vacuum Handling Systems for the Logistics Industry
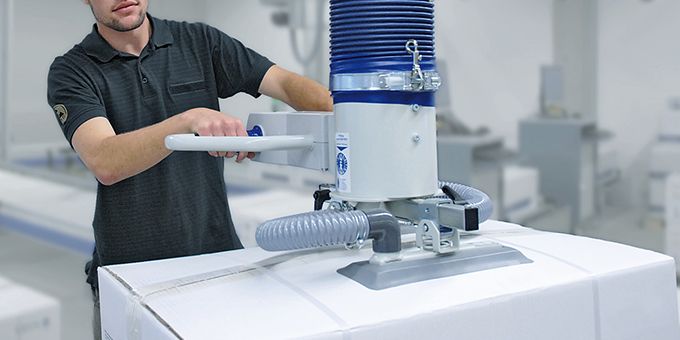
Case Study from | Schmalz, Inc.
One in three online buyers now makes several online orders every week. In 2019, online sales grew by over eleven percent compared to the previous year. This is the result of the e-commerce consumer study by the German E-Commerce and Distance Selling Trade Association (bevh). Manufacturers, dealers and logistics service providers therefore need to optimize their processes accordingly. In order to become more efficient and work more quickly but at the same time protect the health of their employees, it is worth investing in ergonomic lifting devices. J. Schmalz GmbH is an expert in this field. Schmalz designs individual handling solutions and crane systems. The manufacturer also helps to improve the internal material flow in terms of time and costs while at the same time maintaining a focus on ergonomics.
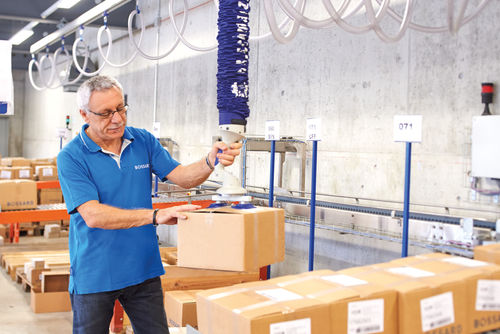
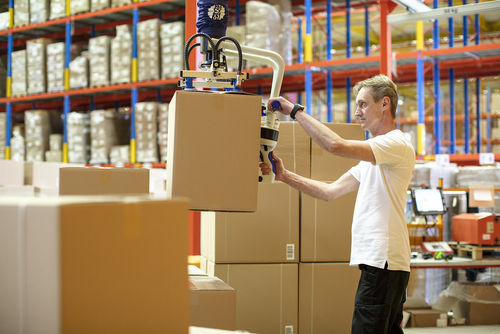
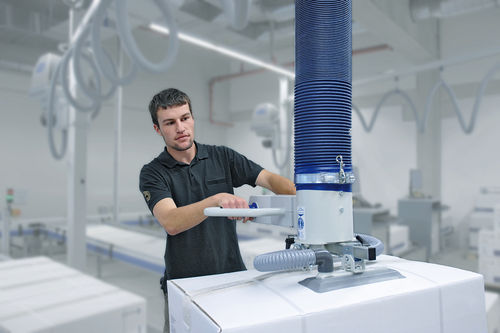
In both intralogistics and distribution logistics, companies have to move large quantities of goods quickly and accurately. The processes mostly involve lifting, rotating and carrying. For example, crates or cardboard boxes are picked up and moved from the conveyor belt to the transport trolley. Schmalz has developed the vacuum tube lifter JumboFlex for the dynamic handling of small workpieces weighing up to 50 kilograms. The vacuum experts designed the operator handle together with the Chair of Ergonomics at the University of Munich. Regardless of whether the user is right or left-handed, he can move the load with a single hand. The lifting, lowering and releasing of the goods can be controlled using just one finger.
The operator can replace the suction cups easily and without tools using the integrated quick-change adapter. Round vacuum grippers are available for cardboard boxes and plastic bags, and double suction cups and four head suction cups are available for open, clamped, glued or larger flat workpieces. The multiple vacuum gripper is a more universal solution for cardboard boxes of various sizes and properties. And even if only 75 percent of the suction area is covered, the gripper can still safely lift the load.
Aiming high
The device boasts a special feature for the loading of pallets. With traditional lift systems, the maximum stack height is usually 1.70 meters. In order to make this process more ergonomic, Schmalz developed the JumboFlex High-Stack. Like the basic version, it is designed for dynamic handling cycles of compact workpieces weighing up to 50 kilograms. The up and down movement is still controlled with just one hand. With the other hand, the operator guides the vacuum tube lifter using an additional guide bar. This allows the vacuum tube lifter to ergonomically and effortlessly reach a maximum height of 2.55 meters. To prevent the unintentional release of the workpiece from a great height, the JumboFlex High-Stack is equipped with a new release mechanism. The operator can only remove the workpiece using a second control button once the workpiece is lowered.
Weighing heavy
If the task calls for handling larger and heavier loads, Schmalz uses the vacuum tube lifter JumboErgo. Since the device is based on a modular system, the operator can individually adjust the suction capacity, lifting height and operator handle. For example, setting the correct operator handle length ensures that there is sufficient safety distance between the employee and the load. The main difference between the JumboFlex and JumboErgo is the form and function of the operator handle. Instead of using just one hand, the user operates the JumboErgo with both hands. That way, he always maintains full control over the heavy objects. As a result, the JumboErgo can ergonomically lift loads of up to 300 kilograms. Using a twist grip, similar to a motorcycle throttle, the operator handle can be used to lift, lower and release the load. Using the optional quick-change adapter, the JumboErgo is easily adapted to different logistics operations. In addition, Schmalz offers a variety of suction cups for different workpieces such as cardboard boxes, crates or barrels.
Familiar processes
As the use of networking in industry increases, there is also greater demand for digitalization of manual processes in logistics. Intelligent handling devices are one way of simplifying ever more complex tasks. The collaborative rope balancer SRCB from Schmalz is a lifting aid with additional sensors and motors for the digital production environment. The electric rope balancer follows the movements triggered by the user. By automatically detecting which gripper is connected, the SRCB can follow approved movement patterns accordingly. It also recognizes programmed work areas. The result is fewer mistakes and improved reliability of the process.
Increased operating range
In addition to the various handling devices, Schmalz offers an extensive range of crane systems. Column-mounted or wall-mounted jib cranes made of aluminum are often used. They combine optimal low-friction operation with lightweight components. This increases efficiency and working speed without impairing positioning accuracy or ergonomics. With a maximum jib length of 6,000 millimeters and a swivel angle of 270 degrees for the column-mounted jib crane or 180 degrees for the wall-mounted jib crane, the operating range of the lifting aid is significantly expanded. Thanks to the modular system, the crane system can be perfectly adapted to the existing infrastructure at a minimal cost. This also allows Schmalz to achieve a high degree of flexibility while limiting the variety of basic components.
The content & opinions in this article are the author’s and do not necessarily represent the views of RoboticsTomorrow
Comments (0)
This post does not have any comments. Be the first to leave a comment below.
Featured Product
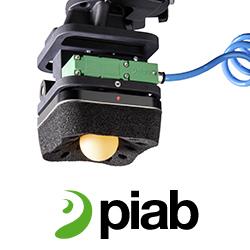