The primary uses for inertial sensors are platform stability and global positioning, but we are seeing increasing use as feedback in articulated limbs.
The use of Inertial Sensors in Robotics
Fritz Martin | LORD Corporation
Tell us about LORD MicroStrain.
LORD Sensing – MicroStrain develops inertial, wireless and displacement sensors and sensing systems for a variety of applications and industries; including, oil and gas, aerospace, unmanned systems and industrial.
Where have you seen the most growth in the company the last few years?
We’ve seen growth across the board – in industrial test and measurement, aerospace antenna pointing, autonomous vehicles, off-highway, and robotics. MEMs Inertial is no longer used exclusively proof-of-concept projects, it is a required component in almost every system.
How are you seeing your Inertial sensors being used in robotics?
The primary uses are platform stability and global positioning, but we are seeing increasing use as feedback in articulated limbs.
What are some of the key specs for determining the best inertial sensor for a robotic application?
An important spec for robotics is often not found on spec sheets and that is the dynamic roll-pitch accuracy. Static accuracy and repeatability are easy to measure and that is usually what is quoted in spec sheets. As soon as you throw in linear accelerations, you often don’t know what you are going to get. The problem is, there is no standard useful dynamic profile with which to measure dynamic accuracy as the dynamics of each application are unique. The best way of determining which device will have the best dynamic accuracy for your application is to measure the error in-run. In head-to-head tests, our Auto Adaptive EKF has consistently out-performed other EKFs in dynamic roll-pitch accuracy.
Another important spec is latency because inertial devices are often in feedback loops for balance and attitude. We test all our devices in a balancing robot.
How does temperature effect sensors?
Bias stability of MEMs sensors can be quite good at constant temperature but often falls apart over temperature. Temperature cycling also brings out bad behaviors such as bias and scale factor hysteresis and even large step jumps. The latter is often an effect of embedment stress caused by the CTE mismatches that are often present in low cost packaging and mounting materials.
The use of sensors in robots has expanded rapidly, how is demand effecting the pricing pressure on inertial sensors?
The horizontal market for robots is rapidly expanding and with it is the expanding demand for lower cost, high-performance MEMs IMUs, AHRS, and GNSS/INS. Volume is what will drive the cost down, and there are few companies that are prepared to provide accurate, low cost, high volume calibration and temperature compensation for inertial sensors. LORD Sensing – MicroStrain is very well situated in this regard, with our fourth generation of proprietary high-volume NIST traceable calibration equipment and our pedigree as a reliable global industry supplier with ISO-9001/AS9100 certification.
What do you feel sets a LORD MicroStrain sensors apart from others on the market?
Every inertial device we have shipped since 2004 has come with a full calibration report, and I don’t believe any other company in our product space can say the same. We develop our own in-house proprietary calibration equipment and have developed a database and domain knowledge that allows us to provide un-rivaled calibration at high volumes and low cost. We also have extensive insight into the real-world behavior of various MEMs components and because of that we only use MEMs components that behave well in dynamic environments. We regularly receive feedback from customers that say that our devices “just work better” even though our specs may be comparable to our competitors, and that is because we have deep insight into how to extract the best dynamic performance from the best MEMs.
With this rapidly changing market how do you see LORD MicroStrain continue to evolve and grow to meet demand?
The inertial market is no-longer in “early-adopter” phase where companies are experimenting with putting inertial devices in their products. Our customers are becoming sophisticated inertial experts and they are coming to us with very specific requirements in performance, price, and volumes. To this end, we are providing a catalog of COTS products that allow the customer to pick only what they need in terms of features and performance. At the same time, better components are coming out quickly, so we are refreshing our product line continuously, but we do it such a way that the customer does not have to re-engineer their product to take advantage of advances in technology. We have stable device footprints and API that allow drop-in upgrades.
The content & opinions in this article are the author’s and do not necessarily represent the views of RoboticsTomorrow
Comments (0)
This post does not have any comments. Be the first to leave a comment below.
Featured Product
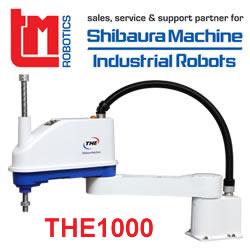