Building a simulation for a palletizing cell helps the integrator and customer start on the same page. Once rate, product, and pallet information is input into the software, realistic cycle times can be shown for any layout/configuration.
Contributed by | Motion Controls Robotics
Building a simulation for a palletizing cell helps the integrator and customer start on the same page. To build a simulation using the PalletTool software from FANUC, you need to discuss and lay out all the information about the process upfront.
This includes information about:
- Pallet size
- Accurate pallet patterns
- Accurate part dimensions/masses
- Realistic expectations of rate based on the upstream/downstream process
- End of Arm Tooling (EOAT) Design – considers the mass and inertia of the EOAT and product load on tooling. In cases where there are multiple parts with different masses, we will usually base the rate off the worst-case scenario
After gathering the data about the process and product to be handled, a robot is selected for the job. Since PalletTool is a FANUC software, the robot’s specifications are already available to the program. The EOAT is designed as a .IGS CAD file and input into the simulation as well as the best layout for the cell. Lastly, items like boxes, pallets, tier or slip sheet racks, cylinders, fencing, and other peripherals can be added.
Simulations can be built for a variety of product types.
Once this information is input into the software, realistic cycle times can be shown for any layout/configuration. Having this simulation available, allows for testing of different setups. As an integrator, we find jobs can go through multiple changes that affect rate such as:
- Conveyor/rack/product placement
- Infeed/outfeed conveyor speeds
- Pallet changes
After the setup is complete and the simulation is running, rates can be analyzed to see how they can be perfected to meet goal robot cycle time by looking more closely at:
- Motion Time (robot moving)
- Wait time (waiting on EOAT action, communication, programmed waits)
- Application time (robot computer delay)
Designing a simulation for any processes that will be performed in hot environments (up to 120 degrees Fahrenheit) is especially helpful because PalletTool can analyze the overheat and/or steady-state overcurrent risks based on different variables and can show the changes adding cooling fans or protective covers on different axes can make.
The simulation can even help you to answer questions about ROI through looking at the life expectancy and even power usage based on different variables including:
- Running hours/day
- Running days/year
- Actual cycle time
- And price of electricity
- Regenerative power option on R-30iB and later only
Finally, robot simulations can find singularity issues (robot joints/wrists being programmed to move to a specific point – resulting in a position that is impossible for the robot) before a project hits the floor (sometimes literally), so it can be engineered around ahead of time.
The content & opinions in this article are the author’s and do not necessarily represent the views of RoboticsTomorrow
Comments (0)
This post does not have any comments. Be the first to leave a comment below.
Featured Product
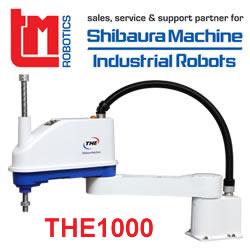