It is easy to imagine the time saved by using the latest simulation tools to develop vision guided robotic applications.
How Using the Latest 3D Simulation Software for Vision Guided Robotic Applications Will Save You Time and Money
Contributed by | Axium
Reprinted with Permission
Image source: Emulate3D
Recent technological developments now make it possible to use 3D simulation software to test vision system algorithms. In a previous blog post , we described the various advantages of using 3D simulation to debug automated equipment so that programmers can spend more time programming and less time manipulating hardware.
What are the advantages of using the latest 3D simulation software? It will undoubtedly save you time and money! Because you no longer have to prepare and set-up the camera, lighting, robot, etc., you can now fine tune your image analysis algorithms from the comfort of your own desk.
It is also possible now to test the interaction of the 3D Simulation Software and the physical environment, as well as its interaction with the PLC and the robot. In other words, it’s a lot easier to integrate different programs.
By converting the object’s depth map from the 3D Simulation Software, this data can be forwarded to the vision software that can now run its algorithms like it would do with a real depth image taken from a standard 3D camera.
To test this new feature, a product sorting sequence was programmed in the 3D Simulation Software to test a vision-guided picking robot application:
- Robot requests pick data;
- Vision software requests depth map;
- Simulation software returns depth map data according to what is “seen” on the infeed conveyor;
- Vision software processes the image;
- Vision software returns pick data to robot;
- Robot executes its task.
The results are conclusive. As you can see from the video below, the 3D Simulation Software works as if it was in a real life situation. In fact, any type of product can be tried, as long as we can get a 3D model of it. With this, an (almost) infinity of test scenarios can be verified without spending a minute on the shop floor to put together the vision guided robot cell.
It is therefore easy to imagine the time saved by using the latest simulation tools to develop vision guided robotic applications. Also, the algorithm robustness can be tested much more easily by virtually trying various scenarios that could be difficult to try in real life situations.
Axium is using Emulate3D solutions.
About Axium
Axium is a leading provider of factory and warehouse automation solutions in a wide variety of industries. Recognized throughout the industry for its innovative designs and expertise, Axium is proud to deliver integrated solutions that yield performance, efficiency and reliability. Axium’s strength is its people. Having installed more than 500 robotic assembly and material handling projects throughout North America and around the world over the last 20 years, Axium’s team has acquired the knowledge and experience necessary to engineer and deliver complex turnkey automation projects.
The content & opinions in this article are the author’s and do not necessarily represent the views of RoboticsTomorrow
Comments (0)
This post does not have any comments. Be the first to leave a comment below.
Featured Product
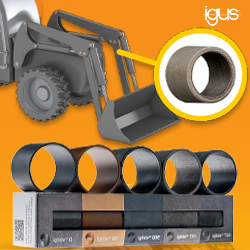