3-D printing could really change medical research. Important questions can be answered, saving both time and money, as 3-D-printed models give surgeons new perspectives and opportunities to practice, and patients and their families a deeper understanding of complex procedures.
Len Calderone
3D printing, also called additive manufacturing, is a process of making three dimensional solid objects from a digital file. The creation of a 3D printed object is achieved using additive processes. In an additive process an object is created by laying down successive layers of material until the entire object is created.
A 3D printer needs to have instructions for what to print, called a file. The file — a Computer Aided Design (CAD) file — is created with the use of a 3D modeling program, either from scratch or beginning with a 3D model created by a 3D scanner. Either way, the program creates a file that is sent to the 3D printer. Along the way, software slices the design into hundreds, or more likely thousands, of horizontal layers. These layers will be printed one atop the other until the 3D object is done.
In medicine, now it's possible to print a model of your own bones, innards, and other anatomical structures starting from a CT scan 3D image, and using only open source software tools. Probably the most commonly used Open Source software applications for processing medical images are OsinX and 3D Slicer.
3-D printing could really change medical research. Important questions can be answered, saving both time and money, as 3-D-printed models give surgeons new perspectives and opportunities to practice, and patients and their families a deeper understanding of complex procedures. Models of an anatomical body part can be created, allowing a surgeon to view a true to life part and even practice on that part prior to the actual operation, thus insuring better results. Training tools and customized surgical equipment can also be printed.
3D printed liver for practice
When a surgeon is learning his or her trade, a cadaver is used for practice. 3D printing presents a better alternative. With 3D printing, there is no wait for a cadaver, reducing the waiting time for practice by printing replicated tissue in just a few days. The difference between the real thing; and the 3D model is minimal and allows for the wider use of models.
Vincent van Gogh lost his ear in a fight with his friend, the French artist Paul Gauguin, although many think that he cut off his own ear. If he were alive today, the doctors could make him a new ear using 3D printing.
Every year thousands of children worldwide are born with a condition known as microtia. Microtia is a congenital deformity of the external ear, where it fails to fully develop. Approximately 1 in every 8,000-10,000 babies born will have some form of microtia. 3D printing could aid these children.
To create a new ear, a 3D scanner will scan the normal ear of the patient. The scan will be reversed, and turned into a 3D printable model. Then a 3D print of the ear will be printed out of a spongy plastic-like material which is porous and will act as a scaffold. The ear will then be placed under the skin on the forearm of the patient for between 4 and 8 weeks. During this time, the forearm skin will grow around the scaffold, along with the necessary blood vessels. The ear is then removed from the arm, and transplanted to the patient’s head.
The advantage of 3D printing in medical applications is the ability to produce custom-made medical products and equipment. 3D printing can produce made-to-order jigs and fixtures for use in operating rooms. Surgical time, the success of an operation and patient recovery time are all positively impacted by custom made implants and surgical tools.
Eventually, drug dosage forms, release profiles and dispensing will be customized for each patient. Using 3D technology, Pharma can custom make prescription medicines for individual patients in the exact dosage to the nearest microgram. This could be the end of the one size fits all dose, which has patients taking too much or too little.
3D printer adapted to produce pharmaceutical compounds
With some medications, like those prescribed to a liver patient, a fraction of a milligram of a drug makes a big difference; and at present, it is exceptionally expensive to adapt to these needs. At some point, we might see that a patient will be able to keep a 3D printer at home, capable of creating formulas for patients that need to change their dosage daily. We might see this technique used in hospitals within the next five years.
Lose a tooth? Had to have a tooth pulled? Now, dentists can print a tooth in 6.5 minutes and replace your lost one. 3D printing allows dentists to replace teeth, crowns, veneers, and inlays in a single sitting. The advantage of 3D printing over the old method of milling is that the process is better able to custom manufacture an appliance with intricate details, such as a tooth's irregular grooves, crannies, and valleys.
Right now, most podiatrists prescribe and develop custom insoles is through outsourcing to a CNC company, which cuts the insoles out of a solid chunk of material.
Podiatrists can now use their own low cost 3D printer to manufacture custom insoles using a new material, Filaflex. First, the Podiatrist scans the patient's foot for 10 seconds using any standard smartphone or tablet. A specialized application will take a complete 3D scan of the patient's entire foot. Then the patient selects a few options for customization, including the color s/he would like the insole. Shortly thereafter, the patient receives the printed insole.
3D printing is also used to create one-of-a-kind artificial limbs to the customer's specifications. No factory parts are used and each limb is made for the specific user.
These one-of-a-kind prosthetics help amputees recover their mobility while at the same time be personalized.
With 3D printing, we will see a trend toward personalized medicine, by customizing nutritional products, organs, and drugs. We will see 3D printing commonly used in pharmacy settings. Pharmaceutical companies will email databases of medication formulations to pharmacies for on-demand prescription printing.
The most important use of 3D printing is the bioprinting of complex organs, like the heart. We could see a fully functioning heart in twenty years. When used as a transplant, a printed organ would be less likely to be rejected by the body, as the patient's own cells would be used to make the organ.
We may even see stem cells stored for growing and developing replacement tissues and organs. Bioprinting for repairing external organs, such as skin, has already taken place. In one case, a 3D printer was used to fill a skin lesion with keratinocytes and fibroblasts in stratified zones throughout the wound.
Researchers will be exploring new uses for 3D printing, as medical advances continue in this field; yet, some of the more revolutionary applications, such as organ printing, will need time to evolve. Presently, 3D printing is a $10 million dollar industry, but it could exceed $2 billion within the next decade.
For further information:
-
http://www.stratasys.com/resources/~/media/
D2C8DC6A4D3243629FE8BF5DE05FA515.pdf -
http://smartechpublishing.com/images/uploads/general/
Final_Medical_White_Paper.pdf
The content & opinions in this article are the author’s and do not necessarily represent the views of RoboticsTomorrow
Comments (0)
This post does not have any comments. Be the first to leave a comment below.
Featured Product
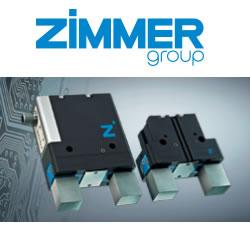