2025 Trends for Augmented Reality in Manufacturing
The shape of augmented reality technology
Augmented reality (AR) is no longer just a futuristic technology to monitor—it has become a powerful tool reshaping the manufacturing industry. From enhancing worker productivity to bolstering operational efficiencies, AR solutions are proving their worth across manufacturing environments. But what does the future hold?
Hélène Druet, Senior Offer Marketing Manager at DELMIA, has analyzed the evolving landscape and identified five key trends for AR in manufacturing in 2025. These trends promise to redefine how manufacturing professionals and organizations leverage AR for innovation and growth.
These five key trends for AR in manufacturing in 2025 are not merely theoretical concepts or long-term visions. They represent the new and tangible advancements that users can experience and benefit from today, shaping the future of the manufacturing industry.
1. Flexibility in augmented reality hardware use
Gone are the days of being locked into one specific AR hardware provider. By 2025, manufacturers will enjoy increased flexibility in their choice of devices, effortlessly switching between AR platforms or systems. This interoperability makes AR adoption more scalable and cost-effective, providing businesses with the agility to leverage the best tool for every task.
Imagine using smart glasses for assembly operations one day and projection system the next—all without compatibility issues or extended downtimes. This ability to adapt seamlessly will empower manufacturers to maximize the value of their AR investments.
One of DELMIA’s Augmented Experience customers, a global leader in aerospace, provides operators with the flexibility to conduct quality inspections using either a tablet or a camera. This allows workers to select their preferred tool for each task, every day, based on their individual comfort and workflow. It’s a great example of adapting to user needs—whether it’s technological familiarity, ergonomic preferences like sitting or standing, or overall ease of use—ensuring seamless adoption of augmented reality solutions.
2. Leveraging Artificial Intelligence (AI) for smarter Augmented Reality (AR) applications
Augmented Reality (AR) is a technology that increasingly depends on artificial intelligence (AI), and the two are becoming closely integrated. AR involves connecting the real world with the virtual, helping users understand their environment through localization and contextual definitions. AI enhances this by analyzing reality and interpreting environments at an advanced level, effectively aligning and synchronizing the virtual twin of a product with the real world.
By 2025, we anticipate a stronger reliance on AI, particularly for quality inspection applications. AR systems enabled with AI will identify defects much quicker and in a reliable way. Another area where AI is going to bring a lot of value is in its ability to improve tracking initialization, enabling rapid and accurate alignment of the digital 3D data and the real part for straightforward visualization of AR instructions.
AI’s role will go beyond troubleshooting or identifying flaws. Predictive algorithms and machine learning will enhance workflows, providing operators with actionable insights in real time. This integration will make AR tools more intuitive, reducing complexity while improving outcomes.
3. Automated Augmented Reality (AR) work instruction creation
Creating AR work instructions for manufacturing processes can be labor-intensive, especially in the case of frequent changes in the 3D model and configurations of the parts. However, automation is set to streamline this in 2025. Advanced software will generate AR-guided instructions directly from CAD models and processes definition, supporting automated updates. Additionally, AI will contribute to enhance processes and work instructions definition, further accelerating the automation of the content creation process.
This innovation will significantly reduce implementation time while ensuring instructions are always up-to-date with the latest designs or processes. Workers will benefit from accurate, clear, and visually immersive directions that reduce errors and improve precision on the shop floor.
4. Enhanced integration of Augmented Reality (AR) with connected technologies
By 2025, augmented reality (AR) in manufacturing is expected to make a significant advancement through greater integration with third-party technologies, resulting in a more enhanced and immersive experience. This development will go beyond simply displaying work instructions and will allow for increased interaction with work cells and the surrounding environment.
For instance, we anticipate seamless connections to smart tools and voice modules, which will expand the possibilities for connected workers. Voice modules will allow workers to interact with AR systems simply by speaking, enabling hands-free operation. Meanwhile, smart tools—like sensors, torque wrenches, or IoT-enabled equipment—will feed real-time data into the AR interface, creating a unified and smarter workspace. Leveraging the AI capabilities mentioned earlier, these technologies become more intuitive by integrating multi-modal interactions through vision (AR) and dialogue (voice), paving the way for a virtual assistant.
This level of connectivity will reduce cognitive workload, enhance comfort, and allow workers to focus on decision-making rather than repetitive tasks. The result? Improved productivity and safer, more intuitive work environments.
5. Improved and extended collaboration thanks to Augmented Reality (AR)
As the adoption of AR systems continues to expand in manufacturing, together with the use of the virtual twin, we are witnessing an exciting trend towards improved and extended collaboration. With an increasing number of AR platforms interconnected, professionals will soon collaborate seamlessly across multiple devices, operators, and even machines, such as robots. Powered by the virtual twin, which serves as a reference point and ensures digital continuity, this connectivity will enable real-time information sharing, synchronized actions, and coordinated decision-making, significantly boosting productivity and efficiency.
By connecting multiple AR devices, several operators can work together on the same task simultaneously, improving coordination. For example, technicians could collaborate on complex assembly processes, such as those in aerospace or automotive manufacturing. This trend not only increases productivity but also enhances teamwork, reduces errors, and is particularly valuable in industries where precision and collaboration are critical.
Enhanced AR systems collaboration can also foster cross-departmental coordination for faster problem-solving. For instance, if an operator identifies a defect, they can immediately report it to a quality inspector, who can then provide real-time AR guidance for diagnosis and correction. This rapid response cycle helps resolve issues quickly and efficiently, ensuring smoother production.
This real-time collaborative model could also extend to interactions with production teams spread across multiple sites, further strengthening the agility and overall efficiency of the manufacturing process.
Why these trends matter for manufacturing professionals
Understanding these trends isn’t just about having a competitive edge—it’s about preparing for the transformation that AR will bring to manufacturing workflows. Whether you’re leading a digital transformation initiative, managing IT strategies, or heading AR based projects, staying ahead of these trends will be critical for driving progress.
Comments (0)
This post does not have any comments. Be the first to leave a comment below.
Featured Product
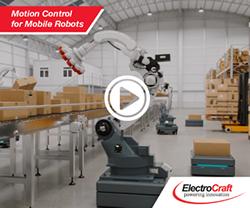