Revolutionizing Warehouse Floors: How AGVs & AMRs are Driving Safety in Modern Manufacturing
Maintaining peak warehouse operations in today’s manufacturing industry requires more than simply overseeing production. To run a productive and efficient facility, safety should be a core priority. If it’s not, you put your staff, equipment, and overall bottom line at risk.
There are countless ways to enhance safety in manufacturing, but one of the most effective ways in today’s landscape is to adopt automated solutions. With automated systems, the possibilities for implementation are endless, but depending on your business goals and needs, automated guided vehicles (AGVs) and autonomous mobile robots (AMRs) prove to be particularly impactful. These solutions are designed to keep your warehouse running smoothly and safely, all while enabling faster and more accurate order fulfillment.
Let’s examine three specific ways AGVs and AMRs can support operational safety and drive your warehouse into the era of smart manufacturing.
Improved Emergency Safety Protocols
The first benefit of AGVs and AMRs in warehousing is the improved safety protocol. Implementing these robotic solutions into your infrastructure can automate operations through advanced safety systems. These systems offer capabilities such as emergency shutdowns or delayed stops for robotic fleets, ensuring the protection of both employees and equipment in the event of an emergency situation like a major collision, warehouse fire, or power outage. When these emergency events occur, it’s vital that you have standardized safety protocols in place and automated solutions that can respond quickly and efficiently for a seamless resolution.
Enhanced Flexibility with Charging Solutions
The next way AGVs and AMRs can contribute to safer, more productive warehouse floors is through thoughtful charging infrastructure choices. Flexible solutions like charging contacts and wireless charging help optimize vehicle range and minimize downtime by enabling efficient charging processes. With the right charging infrastructure, you can often leverage opportunity charging, where vehicles recharge for shorter periods of time throughout the day rather than waiting for a full battery depletion. As a result, charging stations can be placed in various warehouse locations due to increased flexibility and maximized range.
From a safety standpoint, flexible robot charging solutions can help prevent congestion and reduce the risk of potential collisions so your vehicles can remain on track and in great working condition. While AMRs do not follow a predetermined path, they rely on sensors to detect possible obstacles and reroute them to maintain efficiency. Additionally, automated charging processes remove the need for manual intervention, lowering the overall risk of workplace incidents and ensuring a safer, more efficient workflow.
Reduced Warehouse Incidents
Manufacturing facilities experience workplace-related incidents on a regular basis. In fact, the Bureau of Labor Statistics reported over 355,800 manufacturing injury cases in 2023. Common workplace incidents include slips, trips, falls, lifting injuries, burns, and more. These examples are often the result of poor housekeeping practices like unorganized warehouse floors, a lack of safety features, or human error. Turning a blind eye to these behaviors can put your employees and equipment at risk, leading to costly operational downtime and slowed productivity.
Automated solutions can provide the necessary safety assistance to ensure better safety and warehouse productivity. In terms of organization, AMRs are free of trailing wires and cables, immediately reducing the risk of cable-related incidents. AGVs on the other hand follow fixed routes along wires or magnetic tape embedded into the floor. With predetermined routes, these robots perform collision avoidance where they can sense an obstacle hindering their path and wait until it is removed, allowing the equipment to operate safely and with limited hazards.
Moreover, AGVs can carry heavier loads, removing the need for manual lifting, which can lead to potential human injuries. AMRs and AGVs are designed to establish a workplace synergy between robots and humans, automating processes and taking away the need for manual intervention. By adding these solutions to your warehouse floor, you can rest assured that your facility, team, and equipment are safe and supported.
Safety for the Future
Now that you know the primary benefits of automated solutions, you can begin thinking through next steps for implementation. Conducting a safety assessment helps identify current pain points and gaps that have caused or could lead to potential hazards or incidents. Consider asking the following questions during your assessment:
- Is my warehouse layout optimized for safety?
- Does excessive pedestrian traffic create trip hazards?
- Are safety issues resulting from a lack of automation?
- Is my equipment well-maintained and in good working condition?
If your responses reveal that your facility needs a better safety strategy, automated robot solutions may be your answer. To get the biggest safety ROI out of your equipment, you want a solution that can provide immediate results and benefits while supporting your business long-term. Automated solutions like AGVs and AMRs offer more than increased efficiency – they're lasting investments that support the safety and sustainability of your employees, equipment, and facility. By automating safety protocols, enhancing charging flexibility, and reducing the risk of equipment damage or incidents, AGVs and AMRs are pivotal for modernizing warehouse operations.
Kelly Schroder is the Business Development Manager, Americas, for Automated Mobile Solutions at Conductix-Wampfler, a leader in the industrial electrification industry. By developing solutions to business challenges and providing constant support, she ensures successful product implementation and customer satisfaction.
Comments (0)
This post does not have any comments. Be the first to leave a comment below.
Featured Product
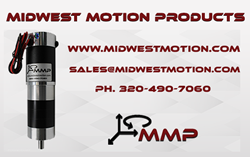