The Role of Automation in Supply Chain Resilience
The modern supply chain faces unprecedented challenges that demand resilience and adaptability. Recent global events, such as the COVID-19 pandemic, have underscored the importance of a robust and flexible supply chain that can withstand disruptions. In this context, automation is emerging as a key driver of supply chain resilience, enabling businesses to adapt quickly, optimize operations, and maintain a competitive edge.
According to a recent study, the global supply chain automation market is expected to grow at a compound annual growth rate (CAGR) of 12.6% from 2021 to 2028, reaching a market value of $31 billion by 2028 . This significant growth highlights the increasing reliance on automation to enhance supply chain resilience.
Let's delve into how automation is transforming the landscape of supply chain resilience.
What is Supply Chain Resilience?
Supply chain resilience refers to the ability of a supply chain to anticipate, prepare for, respond to, and recover from unexpected disruptions. In today’s global economy, where supply chains are more interconnected and complex than ever, resilience has become a critical factor in maintaining business continuity and ensuring customer satisfaction.
Disruptions in the supply chain can come from various sources, such as natural disasters, geopolitical tensions, cyberattacks, or even pandemics. These events can cause delays, increase costs, and result in a loss of trust among customers and partners. Traditional approaches to supply chain resilience often relied on strategies like maintaining excess inventory, diversifying suppliers, and creating contingency plans. While these methods can be effective, they also have limitations, such as increased costs and inefficiencies.
Warehouse Automation Companies are changing the game by offering more dynamic, real-time solutions to these challenges. Automation allows supply chains to be more proactive rather than reactive, enabling companies to identify potential risks early and respond quickly and effectively. This shift from traditional methods to automated solutions is helping businesses achieve a higher level of resilience in their supply chains.
The Role of Automation in Enhancing Supply Chain Resilience
Automation is revolutionizing supply chains by introducing advanced technologies that streamline operations, improve decision-making, and mitigate risks. In the context of supply chain resilience, automation encompasses the use of robotics, artificial intelligence (AI), the Internet of Things (IoT), and data analytics to enhance the adaptability and robustness of supply chains.
Automation in Identifying and Mitigating Risks
One of the most significant benefits of automation in supply chain resilience is its ability to identify and mitigate risks proactively. Automated systems can continuously monitor supply chain operations, flagging potential issues before they escalate into major disruptions. For example, sensors embedded in production lines can detect early signs of machinery failure, allowing for preventive maintenance that avoids costly downtime. Similarly, AI-powered algorithms can analyze vast amounts of data to predict risks such as supplier delays or transportation bottlenecks, enabling companies to take preemptive action.
Real-Time Data and Predictive Analytics
Automation facilitates real-time data collection and analysis, which is crucial for making informed decisions quickly. With the help of IoT devices, supply chains can now gather data from every touchpoint, from raw material sourcing to final delivery. This data, when analyzed using AI and machine learning, can provide predictive insights that help businesses anticipate future disruptions and adjust their strategies accordingly.
For instance, if a significant weather event is predicted to impact a major shipping route, automated systems can reroute shipments in real-time, minimizing delays. This ability to respond swiftly to changing conditions is a cornerstone of supply chain resilience.
Case Studies/Examples
Several companies have successfully implemented automation to enhance their supply chain resilience. For example, Amazon uses robotics in its warehouses to optimize inventory management and speed up order fulfillment. These automated systems not only increase efficiency but also allow Amazon to quickly scale operations in response to sudden spikes in demand, as seen during the COVID-19 pandemic.
Another example is Walmart, which has integrated automation into its supply chain through the use of AI-driven forecasting tools. These tools help Walmart predict demand more accurately, reducing stockouts and overstock situations, thereby improving overall supply chain resilience.
The Benefits of Automation in Supply Chain Resilience
Automation brings a myriad of benefits to supply chain resilience, making it an indispensable tool for modern businesses. By integrating automated systems, companies can not only improve their operational efficiency but also strengthen their ability to respond to disruptions and adapt to changing market conditions.
Improved Efficiency and Reduced Costs
One of the most immediate benefits of automation in supply chains is the significant improvement in efficiency. Automated systems can handle repetitive tasks, such as inventory management, order processing, and shipping coordination, with greater speed and accuracy than human workers. This reduces the likelihood of errors, streamlines processes, and ultimately lowers operational costs.
For example, automated inventory systems can track stock levels in real-time, automatically reordering products when they reach a certain threshold. This reduces the need for excess inventory, saving storage costs and minimizing waste. Moreover, automation can optimize routes for transportation, reducing fuel consumption and delivery times, which further cuts costs and enhances supply chain efficiency.
Faster Response to Disruptions
In a traditional supply chain, responding to disruptions often involves a time-consuming process of assessing the situation, determining the best course of action, and executing the response. Automation significantly shortens this process by enabling real-time monitoring and automated decision-making.
For instance, if a critical supplier fails to deliver on time, an automated system can immediately identify alternative suppliers, adjust production schedules, and reroute logistics to ensure minimal impact on the supply chain. This rapid response capability is crucial in maintaining business continuity during unexpected events.
Increased Flexibility and Scalability
Automation provides supply chains with the flexibility to adapt to fluctuating demands and market conditions. Automated systems can quickly scale operations up or down based on real-time data, allowing companies to meet customer needs without overextending their resources.
For example, during peak seasons like the holiday rush, automated warehouses can increase their throughput by deploying additional robots or adjusting workflows. Conversely, during slower periods, these systems can scale back operations, reducing energy consumption and operating costs. This flexibility ensures that the supply chain remains resilient, no matter the external pressures.
Statistical Insights
Numerous studies have shown a strong correlation between automation and improved supply chain resilience. According to a report by Deloitte, companies that have adopted advanced automation technologies are 3.5 times more likely to outperform their peers in supply chain resilience, demonstrating faster recovery times and better overall performance during disruptions. This data underscores the critical role that automation plays in building robust and adaptable supply chains.
Challenges and Considerations When Implementing Automation
While automation offers significant benefits for enhancing supply chain resilience, it also comes with challenges and considerations that businesses must address to ensure successful implementation. Understanding these challenges is crucial for maximizing the return on investment and minimizing potential risks.
Initial Costs and ROI
One of the primary challenges in adopting automation is the initial cost. Implementing automated systems, whether it’s robotics, AI-driven software, or IoT devices, requires substantial upfront investment. This includes not only the cost of the technology itself but also expenses related to installation, training, and integration with existing systems.
However, it’s important to view this investment in the context of long-term ROI. While the initial costs can be high, automation often leads to significant savings in operational expenses, improved efficiency, and reduced downtime, which can outweigh the upfront expenditure. Businesses should carefully analyze the potential ROI, considering factors such as increased productivity, lower labor costs, and enhanced supply chain resilience.
Integration with Existing Systems
Another significant challenge is the integration of new automation technologies with existing supply chain systems. Many companies operate with legacy systems that may not be compatible with the latest automation tools, leading to potential difficulties in implementation. Successful integration requires thorough planning and often involves upgrading or replacing outdated systems, which can be both time-consuming and costly.
To address this challenge, businesses should conduct a comprehensive assessment of their current systems before implementing automation. This assessment should identify potential compatibility issues and allow for the development of a clear integration plan that minimizes disruptions during the transition.
Workforce Implications
The introduction of automation in supply chains can have profound implications for the workforce. As automated systems take over repetitive and manual tasks, the role of human workers may shift, potentially leading to concerns about job displacement. However, rather than eliminating jobs, automation often changes the nature of work, requiring employees to develop new skills and take on more complex and strategic roles.
To mitigate workforce concerns, companies should invest in reskilling and upskilling programs that prepare employees for the evolving demands of an automated supply chain. By providing training and education, businesses can help their workforce transition to new roles and maintain job security, ultimately contributing to a more resilient and adaptable supply chain.
Security Concerns
With the increased reliance on digital systems and connected devices in automated supply chains, cybersecurity becomes a critical concern. Automated systems are often connected to the internet and other networks, making them vulnerable to cyberattacks that can disrupt operations, compromise sensitive data, and cause significant financial damage.
To safeguard against these risks, companies must implement robust cybersecurity measures, including encryption, access controls, and regular security audits. Additionally, businesses should develop comprehensive incident response plans that outline steps to take in the event of a cyberattack, ensuring that the supply chain can recover quickly and continue to operate with minimal disruption.
The Future of Automation in Supply Chain Resilience
As technology continues to advance, the role of automation in supply chain resilience is expected to grow even more significant. Emerging trends and innovations in automation are set to further enhance the ability of supply chains to withstand disruptions and adapt to changing conditions.
Emerging Trends in Automation
Several emerging trends are poised to shape the future of automation in supply chains. One of these trends is the increasing use of autonomous vehicles and drones for transportation and delivery. These technologies have the potential to revolutionize logistics by reducing dependence on human drivers and enabling faster, more efficient deliveries, especially in remote or hard-to-reach areas.
Another trend is the rise of blockchain technology, which can be used to create more transparent and secure supply chains. By recording transactions in a decentralized ledger, blockchain can enhance traceability, reduce fraud, and ensure the authenticity of products as they move through the supply chain. This added layer of security and transparency can significantly contribute to supply chain resilience.
The Evolving Role of AI and Machine Learning
Artificial intelligence (AI) and machine learning (ML) are at the forefront of automation in supply chains. As these technologies continue to evolve, they will play an increasingly critical role in enhancing supply chain resilience. AI and ML can process vast amounts of data faster and more accurately than humans, enabling more precise forecasting, demand planning, and risk management.
In the future, we can expect AI-driven supply chains that are capable of self-optimizing in real-time, automatically adjusting operations based on current conditions and predictive analytics. This level of automation will not only improve efficiency but also allow supply chains to become more proactive in mitigating risks and responding to disruptions.
Long-Term Benefits for Businesses
The long-term benefits of adopting automation in supply chain resilience are profound. Companies that invest in these technologies will be better equipped to navigate the complexities of the global market, maintain continuity during crises, and stay ahead of the competition. Moreover, automation contributes to sustainability by optimizing resource use, reducing waste, and lowering the environmental impact of supply chain operations.
As businesses continue to embrace automation, they will find that these technologies offer a competitive advantage that goes beyond short-term gains. Automation is not just a tool for improving efficiency; it is a strategic investment in the future resilience and sustainability of the supply chain.
Sum Up...
Automation is crucial for building resilient supply chains that can withstand disruptions and adapt to change. By integrating technologies like AI, robotics, and IoT, businesses can enhance efficiency, reduce risks, and ensure continuity.
To explore how these automation strategies can be applied to your business, visit appsinsight.co for more information and related queries.
Comments (0)
This post does not have any comments. Be the first to leave a comment below.
Featured Product
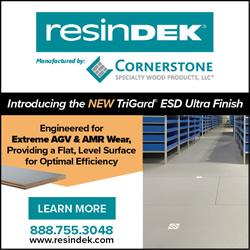