Unlocking Efficiency: The Role of AI in Optimizing Pick & Place Robotics
Pick-and-place automation has become a cornerstone of modern warehouse operations, ensuring that tasks are executed with the utmost precision and consistency. As warehouses evolve to meet the demands of dynamic industries like e-commerce and pharmaceuticals, the role of these robotic systems becomes increasingly vital.
At the heart of pick and place robotics is the automated process of moving items from one location to another with exceptional accuracy. This seemingly simple function is crucial across various industries, from sorting and packing orders in fulfillment centers to handling delicate pharmaceutical products. The ability to perform repetitive tasks with unmatched precision not only optimizes workflow but also minimizes errors and boosts throughput.
Artificial intelligence (AI) and machine learning (ML) are transforming the landscape of pick-and-place robotics, elevating these systems to new levels of efficiency and adaptability. By processing vast amounts of data in real time, AI-driven robots can make intelligent decisions, optimize operations, and continuously improve over time. This advancement is redefining the way warehouses operate, offering enhanced productivity and reliability.
Meeting Industry Demands with Precision and Accuracy
Think of AI and software as the brain behind pick and place robots. Just like our brains process information to make decisions, the AI within these robots constantly analyzes data to determine the best way to handle and place items. This "brain" enables the robot to understand its environment, recognize different products, and decide how to pick them up and move them with incredible precision.
In industries where precision is crucial - like e-commerce and pharma - this capability is invaluable. Accurate order fulfillment isn't just about moving products, it’s about ensuring that every item is handled with care and placed exactly where it needs to be. The AI-driven brain of the robot makes sure this happens consistently, reducing errors and boosting efficiency. By mimicking human decision-making processes, these robots can deliver the level of accuracy and reliability that modern businesses demand.
The Robot’s Path to Continuous Improvement
Imagine the robot’s brain getting smarter with every task it performs. AI-powered pick and place robots don't just follow a set of instructions - they actually learn from their experiences. Using machine learning, these robots analyze their past performance, spotting patterns and figuring out ways to do their job even better.
This continuous learning process is vital in fast-paced environments like warehouses and fulfillment centers, where the layout of products and types of orders are always changing. As the robot's brain processes this information, it adapts, refining its strategies to keep up with the shifting demands. This ability to learn and improve makes these robots increasingly efficient, ensuring they can handle the complexities of modern warehouse operations with ease.
Navigating Complex Environments via Dynamic Path Planning
Much like humans rely on our thought processes to adapt to and navigate tricky situations, so do robots. AI enables pick-and-place robots to navigate complex warehouse environments with agility. By leveraging AI algorithms for path planning and collision avoidance, these robots can adjust their routes in real time to avoid obstacles, optimize travel paths, and minimize downtime. This capability is essential in crowded warehouse settings where space is limited and efficiency is paramount.
By continuously processing data and making split-second decisions, the robot’s brain ensures smooth operations, minimizing delays and keeping the workflow moving seamlessly.
Predictive Maintenance and Reliability
AI-powered robots can monitor their own performance, learn from past encounters, and detect potential issues before they escalate into costly failures. Predictive maintenance algorithms allow these robots to analyze sensor data and operational metrics, identifying signs of wear and tear and scheduling maintenance activities accordingly.
The integration of AI into pick-and-place robotics is redefining efficiency, productivity, and reliability across various areas in Logistics. By harnessing AI-driven capabilities like enhanced precision, adaptive learning, dynamic path planning, and predictive maintenance, warehouse operations can be optimized, workflows streamlined, and superior results can be achieved.
Conclusion
As the backbone of modern warehouse operations, pick-and-place robotics have become essential in industries where precision, speed, and reliability are non-negotiable. Yet, it’s the sophisticated software and AI that act as the robot's brain, driving these systems to new heights of efficiency and adaptability. This AI-driven brain is what enables the robot to navigate complex environments, make intelligent decisions on the fly, and learn from each task it performs.
The ability to not only perform tasks with precision but also to improve over time and anticipate challenges ensures that these robots are not just tools, but intelligent partners in achieving success. As technology and robotics continue to evolve, the importance of a well-tuned robotic brain will only grow, paving the way for more innovative and efficient warehouse operations.
Smart Robotics Founder and CEO, Heico Sandee, holds a PhD degree and previously acted as program manager for robotics at Eindhoven University of Technology. With more than 15 years of experience in robotics development, Heico now leads Smart Robotics in developing intelligent, robot-independent software for flexible deployment of automated solutions.
Smart Robotics is a leading developer of AI-driven robotics and automated warehouse systems. Their pick and place robotic solutions are engineered to improve overall capacity, increase the reliability of warehouse operations, and tackle issues related to the continuing labor shortage in the logistics industry. These solutions are driven by Smart Robotics’ advanced AI tech-trinity, hardware and software. Smart Robotics’ customised automation solutions aim to improve working conditions for warehouse floor workers by taking over repetitive and physically strenuous tasks, such as order picking, packing, palletizing, and sorting.
Comments (1)
Featured Product
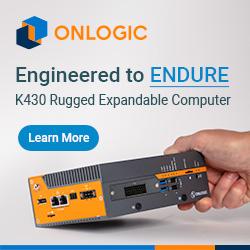