If You're Struggling With Production Inefficiencies, Cobots Might Help
Manufacturers face greater pressure to increase their output than ever before. While automation has helped meet these rising demands, bottlenecks remain. The answer may lie in recognizing the benefits of cobots.
Cobots — short for “collaborative robots” — are automated equipment designed to work alongside humans instead of replacing them. As a fairly new category, their adoption numbers have been modest. They account for just 34.9% of factory automation today, but that may soon change as manufacturers realize how they could boost production efficiency.
Robotic Efficiency
The most obvious benefit of cobots is the same as all automation — it’s faster than manual work. Repetitive tasks like welding, component placement and machining are challenging for humans to perform efficiently. Even skilled workers will eventually slow down as they get tired, but machines don’t face the same limits.
One company tripled its throughput after implementing a cobot welder. What once took an employee eight hours to do took the bot just two and a half. It’s worth considering that such a jump came from a single robot, so larger investments could yield even more impressive results.
Similarly, cobots enable greater overall productivity by offsetting the impact of labor shortages. Manufacturers struggle to scale up efficiently as fewer young workers enter the industry. However, facilities do not need as many employees to increase production when automated equipment handles much of the work, making skill gaps less impactful.
Error Reduction
In addition to completing tasks faster than humans, cobots are less likely to make mistakes. People get tired and distracted, leading to errors resulting in scrap and rework, but a robot delivers the same accuracy with each cycle. A cobot can perform the same process hundreds of times with no decline in quality.
Such precision impacts productivity in a few ways. First, it minimizes bottlenecks in quality control because there will be fewer defects to flag and put aside, stopping the line. Preventing scrap also improves material efficiency, as the manufacturer can maintain the same output with less input.
Error prevention also removes the need for rework. As a result, the production line can operate with no energy or time loss from fixing a mistake.
Higher Adaptability
All robots, collaborative or otherwise, provide higher efficiency and reduced mistakes, but cobot benefits go further. Conventional automation is inflexible, so even though it works faster than manual alternatives, it’s prone to disruption from process deviations. Any unexpected changes will produce errors and downtime, counteracting its productivity.
By contrast, studies show operations work much more efficiently when people and automation collaborate instead of having fully automated workflows. That’s because cobots let manufacturers capitalize on the unique benefits of robots and human workers. Machines are fast, and employees are adaptable, so a solution centering on them working together offers an ideal middle ground between speed and reliability.
Such collaboration may look like humans handling preprocessing before a cobot performs repetitive, predictable tasks like welding or cutting. Alternatively, manufacturers could use employees to transport goods and ensure they meet quality standards but deploy cobots to process these materials. In any case, cobots allow greater flexibility by working alongside humans.
Less Infrastructure
Another benefit of cobots over conventional robots is that they require less hardware. Industrial automation often needs bulky physical safeguards, power systems and similar infrastructure to keep it efficient and safe. While necessary, those additions quickly add costs and take up valuable space. Cobots, by contrast, don’t need the same restrictions.
Because cobots work closely with humans by design, they have additional built-in protective features. These often include sensors to detect nearby employees and programming to keep them from moving with too much force. As a result, they can safely operate without barriers or large supplementary equipment.
Removing the need for such infrastructure means manufacturers have more floor space for production increases. It’s also worth considering how average manufacturing rents have risen to $9 per square foot, an almost 50% increase over 2020’s costs. Consequently, some businesses may be unable to scale up in terms of space, so using compact cobots enables scaling where it’s inaccessible otherwise.
Improved Safety
Similarly, cobots are safer than traditional automation solutions. Injuries resulted in 108 million lost workdays of productivity in 2022. While all robots reduce these incidents, cobots produce more meaningful improvements because they address accidents involving human contact with heavy machinery.
In addition to featuring built-in protective measures, cobots accustom people to working closely with automated equipment. As a result, employees learn not to make dangerous mistakes. Fixed conventional robots may fail to achieve the same safety levels because people are less familiar with them, making injury-producing errors more likely.
Of course, cobots require additional implementation steps to be as safe as possible. Preventive maintenance lowers the chances of unpredictable behaviors that may cause injuries, so a proactive care plan makes this equipment much safer. Thorough employee training and recalibrating cobots often will also help.
Versatile Use Cases
Application versatility is another key cobot benefit deserving of manufacturers’ attention. Many industrial robots are purpose-built, which is great for efficiency but leaves no room for necessary adaptations amid changing conditions. By contrast, a single cobot can often perform several roles.
The manufacturing industry is changing. Almost 80% of enterprises today expect their supply chains to be more circular in the next few years — a change requiring workflow adjustments. Adapting to these new setups is challenging with fixed, single-task robots, but cobots are versatile by design, making them easier to reprogram into a new setup.
Minimizing disruption amid workflow changes means manufacturers can maintain peak productivity over a longer period. It also reduces the associated costs. Consequently, cobots are the better solution in the long run, even if conventional robots yield larger short-term speed improvements.
Capitalize on the Benefits of Cobots Today
As these cobot benefits show, a collaborative approach to automation offers solutions where older methods have fallen short. Manufacturers who have struggled to achieve desired results from conventional robotics should consider how cobots can help them strike an ideal balance.
Taking advantage of this opportunity will become increasingly important as time goes on and demands rise. Learning how cobots can pave the way for higher throughput and lower costs is the first step in a long road to meeting the needs of tomorrow.
Comments (0)
This post does not have any comments. Be the first to leave a comment below.
Featured Product
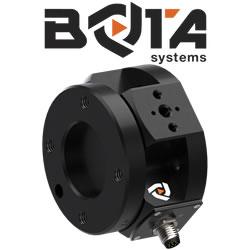