Automation isn't a one-size-fits-all: 5 key considerations for your warehouse
The explosion of e-commerce has catapulted consumer demand to dizzying heights, leaving traditional warehouse operations scrambling to adapt. With projections indicating that over 75% of companies will have adopted some form of advanced automation within their warehouse operations by 2027, it's clear that change is already here.
Out of this rapid evolution comes robotics and AI-vision technologies, promising to revolutionize efficiency and productivity through automation. However, the allure of automation comes with a caveat: There's no universal blueprint for success.
Each warehouse is a unique ecosystem with its own rhythms, challenges and opportunities. To unlock its full potential, organizations must thoughtfully implement automation based on what their environment needs to thrive, whether that be labor replacement, rapid ROI or predictability within the facility.
From AI-vision systems revolutionizing inventory management to advanced depalletization solutions streamlining logistics, we'll explore five critical considerations that can make or break your journey toward integrating robotics into warehouse operations.
The current state of warehouse operations
Global e-commerce sales are projected to surpass $5 trillion annually by 2027. This surge has pushed the logistics industry, including warehouses, to its limits. As leaders expand their warehouse footprint, 77% of them recognize the urgent need to modernize their operations. Yet many struggle to implement new technologies swiftly.
While some operations undertake full-scale deployments in new facilities, many more are navigating the complexities of gradual, piecemeal upgrades in existing warehouses. This shift toward modernizing brownfield sites — more common now than during the height of COVID-driven expansion — often results in a more measured pace of technological adoption.
This hesitation comes at a cost. Today's consumers demand lightning-fast fulfillment, with about a quarter abandoning carts due to inadequate shipping options. To meet these expectations, warehouses must look beyond traditional cost-cutting measures. The new frontier of efficiency lies in smart automation, AI-driven processes and robotics that can work alongside human workers.
The challenge now is not just to grow but to grow smarter. Warehouses must evolve into high-tech hubs capable of meeting the rapid pace of e-commerce while navigating ongoing labor shortages. As we stand on the brink of this transformation, the question isn't whether to automate but how to do so in a way that maximizes return on investment and positions businesses for long-term success.
Five key considerations for adopting warehouse robotics
By carefully weighing each of the following factors, you'll be better equipped to harness the full potential of robotics while avoiding common pitfalls in the automation journey.
1. Long-term ROI vs. short-term investment
The initial cost of robotics can be daunting, but the upfront price tag is an investment into significant long-term benefits, such as increased productivity, reduced errors and 24/7 operation capabilities.
For those hesitant about large capital expenditures, Robotics as a Service (RaaS) offers an attractive alternative. This scalable model allows warehouses to deploy robotic solutions without the burden of ownership and maintenance costs, making automation more accessible to businesses of all sizes.
2. Suitability assessment
Automation isn't a one-size-fits-all solution. Some warehouses, particularly those dealing with highly variable or delicate items, may not be immediately suited for certain types of robotics. For instance:
- Facilities that store delicate and uniquely shaped items may struggle to use standard robotic arms for retrieving items.
- Warehouses specializing in custom-made furniture with varying dimensions may have difficulty using automated storage and retrieval systems designed for standard box sizes.
- Distribution centers for fresh produce may encounter challenges due to food storage requirements.
So, warehouse operators must assess their specific needs and constraints with a thorough suitability assessment before diving in. This will help them identify which areas of operation are prime for automation — such as tasks that would benefit from depalletization robots — and which may require alternative solutions.
3. Unique workflow analysis
Every warehouse has its distinctive set of processes shaped by years of operation. Successful automation hinges on understanding and respecting these existing workflows. Rather than forcing a complete overhaul, the goal should be to enhance efficiency within the current framework.
AI-vision systems play a crucial role here. By analyzing current operations in real-time, these systems can identify bottlenecks, predict potential issues and suggest optimizations. This data-driven approach ensures that robotic solutions are tailored to your specific needs, maximizing their impact and minimizing disruption.
4. Software integration and deployment
The most advanced robotic system is only as good as its integration with your existing warehouse management systems (WMS) and warehouse control systems (WCS). Seamless integration is vital for maintaining operational continuity and leveraging automation's full potential.
Look for providers offering solutions designed to work harmoniously with your current software ecosystem. The right partner can often facilitate rapid deployment, allowing you to start reaping the benefits of automation from the very first day.
5. Human-robot collaboration
The goal of warehouse robotics isn't to replace all humans but to augment their capabilities. AI and robotics excel at repetitive, physically demanding tasks, freeing up human workers to focus on complex problem-solving and decision-making roles.
In practice, this might involve robots handling routine picking and packing while humans manage quality control and customer service. Or, it could involve AI systems flagging potential issues for human review, combining machine efficiency with human judgment. The key is to view automation as a tool to empower your workforce, not substitute it.
By carefully considering these five factors, warehouse operators can chart a course towards automation tailored to their unique needs, maximizing efficiency and positioning their operations for success in the explosive world of e-commerce.
About the Author
With more than 30 years in the robotics and automation industries, Crystal Parrott, COO of Plus One Robotics, has a history of bringing emerging technologies to market. Previously, Crystal served as the Vice President of the Robotics Center of Excellence for Dematic Corp, where she led all robotic initiatives and guided and supported the generation of robotic solution sales in the logistic market. Prior to joining Dematic in 2018, Crystal spent 11 years leading the development of advanced robotics technology and promoting it to create new businesses at Southwest Research Institute. Crystal holds a Master of Science in Management of Technology from the University of Texas at San Antonio as well as a Bachelor of Science in Electrical Engineering from Kettering University.
Comments (0)
This post does not have any comments. Be the first to leave a comment below.
Featured Product
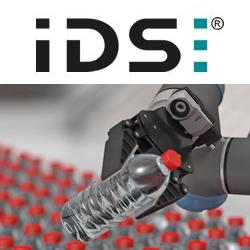