Solving the logistics labor puzzle: Choreographing a Tango of Robots and Human Labor in Warehouse Operations
The labor situation in the supply chain and logistics space is still far from optimistic. According to a recent study, 76% of leaders in the space report significant workforce shortages across the globe, with many of them characterizing the shortage as high to extreme, impacting financial performance, peak season operations, logistics partner performance and customer service. Naturally enough, the gravity of the workforce shortage was keenly felt in warehouse operations. However, living in the midst of unprecedented technological breakthroughs comes with its own share of benefits, allowing us to reassess workforces and leverage technology to supercharge productivity.
Automation emerges as a priority for productivity
An international study conducted by Descartes revealed that the most successful organizational strategy for enhancing worker productivity is the automation of non-value added and repetitive tasks (54%). This emphasizes the prevalence of routine yet non-integrated functions within the supply chain and logistics sector, which currently necessitate manual intervention. Warehouse operations (40%) was the top area of investment to mitigate the impact of the current labor market, followed by transportation operations (32%).
The most pressing dilemma for the logistics industry is perhaps maximizing output levels that match consumer needs while not having enough employees taking up physically demanding tasks like parcel picking and sorting. Not to mention, the growing costs that accompany the situation. In order to remain competitive, it’s integral to scale up capacity-wise while also keeping labor costs in check. If there is one thing that the persistent labor shortage has demonstrated, it’s that passively waiting around for things to get better is a chancy gamble. The most practical solution lies in taking action, even if it means tackling one thing at a time. Picking and placing packages is one such area with a lot of potential. Robotic systems automate the stacking, (de)palletizing, and handling of goods and products, reducing the physical and mental strain that warehouse workers bear.
Pick & place stations- The new focus of automation
Robotic pick & place solutions are redefining the standards of precision and agility for automated systems, optimizing space and significantly increasing parcel throughput in the process. Most importantly, robots being able to perform these tasks consistently and round the clock, takes care of repetitive and strenuous activities like moving heavy goods around, which are otherwise handled by human workers. Not only does it alleviate the obvious risks inherent in such rigorous activities, it also reduces the likelihood of errors in execution. Especially during peak seasons, when warehouse personnel are stretched to full capacity to fulfill an overwhelming flow of orders, automated pick & place systems can increase capacity and performance without the need for significant additional manpower. Besides, high volumes of inventory and traffic also mean that warehouses face a lack of storage space available to accommodate these fluctuations, potentially leading to problems in order fulfillment. This is particularly true for warehouses specializing in stocking e-commerce and retail merchandise, like electronics and personal-care products. Automated systems can optimize storage space by efficiently organizing and storing inventory, thereby maximizing available space. It can also quickly adjust to fluctuating demand, ensuring reliable turnaround times even in highly demanding logistics.
Intelligent parcel picking robots are engineered for reliability, with intuitive AI technology at their core. This enables robots to self-teach and adapt to their surroundings, continuously enhancing efficiency and productivity with minimal human supervision. By automating parcel picking tasks, these systems not only improve efficiency, but also contribute to the long-term sustainability of logistical processes by reducing the physical strain on human workers. Moreover, given the systems’ ability to run continuously, they work favorably to achieve a quicker return on investment as well. Looking ahead, we’ll see automation becoming more accessible and affordable for small establishments, with flexibility and scalability at the heart of it.
That said, efficient implementation of automation also requires the warehouse infrastructure that supports it, and thus, the readiness to redesign layouts if necessary. For eg. reliable electricity connections and layouts free of support columns, minimizing obstacles for the robots to navigate, reducing the risk of collisions. In a well implemented arrangement, robots and humans can indeed work together, fitting perfectly like a puzzle, each filling in for the other’s weaknesses but complementing each other’s strengths. However, like a puzzle, the implementation of automation must be appropriate and thoughtfully executed to ensure it aligns with the needs of the operation. A single solution may not address all the problems, nor it may fit appropriately everywhere.
With new technologies come new job opportunities
While automation renders some tasks redundant, it also creates opportunities for more value-added work, such as knowledge-based tasks. This is especially significant in the supply chain and logistics industry, where over half of leaders surveyed across the globe have identified knowledge- based roles as the most challenging to fill, as operations are becoming more technology-enabled and data-driven. Think about it this way— if there is a pressing labor shortage, automating those areas for which there are already no takers, doesn’t necessarily “threaten” jobs. But at the same time, it creates opportunities to make the industry more attractive for job seekers. It’s not about replacing humans with robots, but about allowing humans to do what they like to do more of and are valued for, by relieving them of tasks they would rather pass— the tedious, draining tasks, the risky ones.
Ascertaining certain tasks to the robotic workforce not only relieves its human counterparts of a large part of the physical labor, but also frees their mental capacities enabling them to utilize intrinsically human skills like critical thinking and empathy. For instance, in an e-commerce fulfillment center, pick & place robots may handle the repetitive task of picking items from shelves and placing them into shipping containers, while the human staff identify opportunities to improve efficiency in the order fulfillment process, such as streamlining packaging procedures, optimizing pick paths, or analyzing data to make informed decisions about stock levels and product offerings. They may have more time thanks to automation to take on novel and interesting tasks, hone new abilities, and cultivate relationships with stakeholders, customers, and coworkers.
When humans and robots are mentioned in the same breath, it’s not about choosing one or the other; it’s about materializing the most rewarding combination of the two. After all, the success of the technology largely hinges on the skill and expertise of the human workforce utilizing it.
About Heico Sandee
Smart Robotics Founder and CEO, Heico Sandee, holds a PhD degree and previously acted as program manager for robotics at Eindhoven University of Technology. With more than 15 years of experience in robotics development, Heico now leads Smart Robotics in developing intelligent, robot-independent software for flexible deployment of automated solutions.
About Smart Robotics
Smart Robotics is a specialist-developer of robotics and automated warehouse systems. The pick and place robotic solutions offered by the company are engineered to improve overall capacity, increase the reliability of warehouse operations, and tackle issues related to the continuing labor shortage in the logistics industry. These solutions are driven by Smart Robotics’ tech-trinity hardware and software. Smart Robotics’ tailormade automation solutions help improve working conditions for warehouse floor workers by taking over repetitive and physically strenuous tasks, such as order picking, packing, palletizing, and sorting.
Comments (0)
This post does not have any comments. Be the first to leave a comment below.
Featured Product
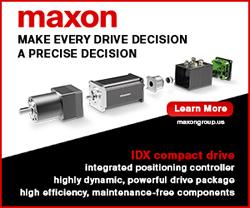