Are Labeling and Palletizing Robots the Secret Weapon Manufacturers Need?
More manufacturers are exploring how to stay competitive in an increasingly challenging landscape, and many are evaluating whether it’s time to add a palletizing robot or labeling robot to their existing assortments of industrial equipment. Robots are not magic fixes to all manufacturing industry obstacles, but they can allow users to overcome many challenges when implemented thoughtfully.
Deploying a Palletizing Robot to Pursue Growth
Many decision-makers realize their companies must grow to maintain competitiveness and meet customer needs. They often determine that robotics investments will help them reach future growth goals.
One example comes from a whole-grain foods company founded in 1978. One of its aims is to double the number of people consuming its products by 2030. However, the manual labor workforce had dwindled during the COVID-19 pandemic. Leaders wanted to tackle that issue by finding a collaborative robot that could work in close quarters with operators. They felt it would fill the gap between traditional industrial robots and manual palletizing.
Executives eventually chose a palletizing robot that could handle up to 14 cases per minute. That was approximately double what the company’s production line required, and significantly better than the ten to 12 cases-per-minute rate workers were trying to achieve. It soon became clear that the model was an excellent choice to work with the 81-inch pallets used in the facility. The cobot could easily reach a pallet’s far corners without requiring elevation.
Leaders also liked how product changeovers can happen in minutes. That’s important for this brand, which processes everything from baking mixes to granola in its facility. Additionally, it only took about an hour for everyone to be trained on working with the cobot. Executives found all operators could learn to operate it.
The labor force changes were also positive. The cobot freed up four operators over four shifts, allowing them to switch from pallet stacking to more value-added tasks. Injury rates decreased as well.
Using a Labeling Robot for Better Accuracy
Labeling is another task well-suited to robots because they excel when performing duties with little variation. Some robotic systems used for label applications also have built-in tracking features, allowing people to verify specifics about the labeled products, including their destinations or package contents.
Well-designed and properly placed labels can also increase customer trust. One study found 60% of consumers who shopped online chose transparency as the most important brand trait. It’s not always easy for someone to know exactly what they’re buying through the internet, but an increasing number of e-commerce companies offer label photographs in product descriptions.
Whether a brand sells its products online, in physical stores or both, challenges remain concerning label accuracy. People must ensure labels have the right details printed and the correct ones are on the appropriate products.
Mislabeling is a common cause of product recalls. In one recent case, a candy company recalled nut-containing items that didn’t mention that ingredient on the labels. The oversight is particularly severe since tree nuts are among the most common allergens affecting children and adults.
Fortunately, a carefully chosen labeling robot can reduce or eliminate such issues. Many have computer-vision systems that scan a package and its label, ensuring the two match. One commercially available system can attach up to 2,400 labels per hour, including on unusual or randomly shaped containers. This automated solution can also recognize a package’s features — such as existing labels or barcodes — preventing placement errors.
Investing in Robots to Address Labor Shortages
The manufacturing labor shortage has been a popular topic across industry blogs. What must concerned parties do to attract more people and position jobs as appealing options? This industry is one of many that has recently experienced a shortage of workers.
People have also faced challenges in finding enough candidates with the right skills to work on construction sites. One strategy applied to cases is to increase the number of women working in such environments. Females are in the minority, so the idea is that increasing their prevalence on construction sites could address persistent shortages.
A manufacturing leader may similarly find that a labeling robot or palletizing robot could address labor needs, depending on the specific obstacles faced. A 2024 study analyzed the manufacturing labor shortage by comparing the number of searches for particular jobs and the actual roles available. The results showed Wyoming is the most severely affected state, showing an 89.47% deficit, or only 20 searches performed for 190 roles.
Labor shortages can also increase injury rates, especially if people push themselves too hard or become fatigued during their shifts because of overly heavy workloads. Then, workforce deficits ultimately worsen due to employees needing time off to recover. However, robots can help manufacturers cope with these assorted issues.
Real-Life Labor Shortage Relief From Robots
Although coverage of industrial robots’ impact on the labor shortage is widespread, the content doesn’t always detail the precise results. However, hearing about how machines have helped manufacturing leaders in the real world can increase executives’ confidence in using them.
The leaders of a Chicago-area coffee company researched available palletizer robot models to speed production. Although the business started by roasting and packaging a single brand at its facility, it now has four in-house blends and fills the needs of several private labels. Once executives purchased two palletizers, they helped increase the company’s productivity by 15% and allowed decision-makers to bid more aggressively to acquire new customers.
Additionally, robotic options, such as those that handle palletizing and labeling, can tackle the tasks that put people at risk of repetitive strain injuries. One cheese company switched from a manual process to a labeling robot, which enabled a labeling rate of up to 81 products per minute. The chosen machine also meets stringent meat and poultry processing plant requirements.
Is It Time to Invest in Robots for Labeling and Palletizing?
Before purchasing labeling and palletizing robots, manufacturing leaders should consider their budgets and technology implementation timelines. Those things will inform how and when they proceed.
Executives should also consider the current manufacturing layout. Would a palletizing robot fit into it without requiring major changes? How does the company handle labeling now, and could it replace several pieces of equipment with one machine that positions labels on containers? Answering questions like these is a great way to make highly informed purchasing decisions and anticipate measurable results.
Comments (0)
This post does not have any comments. Be the first to leave a comment below.
Featured Product
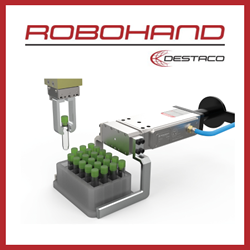