Propelling Your Operations Forward with Wireless Charging: Here’s What to Know
As automation continues to pick up steam in manufacturing, facilities are constantly searching for efficient and effective technology solutions that can streamline operations, limit staffing shortages, and improve service quality. And now more than ever, as the industry continues to face supply chain unknowns, businesses are moving toward automated mobile robot solutions like AGVs and AMRs.
The adoption of these solutions is on an upward trajectory, expected to reach an $18 billion market revenue by 2027. To reap the benefits of this technology, business leaders should deploy AGVs and AMRs where the solutions can deliver the most significant impact and bridge operational gaps. It’s also critical to set your facility up for success in implementation – and that starts with developing a charging strategy.
Your charging strategy is a vital component for simplifying internal material transportation and data transfer. One option in the space gaining popularity and adoption is a wireless charging system, which provides intervention-free charging. With wireless charging comes a unique set of considerations to ensure you get the most out of your equipment and investment.
Here are three things to consider to get the most out of your wireless charging strategy.
Assess Your Current Infrastructure
Before integrating wireless charging across your facility, start by assessing your current infrastructure to determine what areas could benefit from using autonomous robot solutions. What are your current challenges – are you struggling with data transfer issues or looking for a way to cut down on repetitive workforce tasks? AGVs and AMRs are designed to seamlessly integrate into your operations, acting as quick and efficient automation solutions.
Understanding your operational challenges can help you identify which robot is suitable for your facility. AGVs follow fixed paths and require the use of magnetic tapes or wires. They typically perform well in more traditional facilities with a consistent production environment. AMRs, on the other hand, can navigate uncontrolled environments without fixed routes and can be operated with fleet control software. Manufacturing facilities have been migrating toward using AMRs because of their flexibility and variability in new and changing environments. By understanding the workflows within your operating space, you can know which solution is right for your business and then consider your charging strategy needs.
Weigh the Pros & Cons of Wireless Charging
Next, consider how wireless charging will enhance automation within your facility or warehouse. Wireless or inductive chargers are intervention-free, as they rely on electromagnetic induction that is used to transmit energy between the mobile robot and charging station. They operate without plugs or paddles and are optimized for Lithium batteries. So why choose this charging strategy over a more conventional method like conductive charging? Wireless charging plays a significant role in reducing operational downtime, eliminating manual intervention, and maximizing your ROI.
Because wireless charging is ideal for lithium-ion batteries, you can participate in opportunity charging, charging your mobile robots for shorter durations of time throughout the day. Where AGVs and AMRs have historically charged all at once, this practice now removes the risk of paused operations and wasted time, allowing you to set up charging stations in various places like workstations, staging areas, and loading/unloading stations. As workflows and production line processes constantly ebb and flow, wireless charging gives your business the flexibility and adaptability to keep operations moving forward.
Prioritize Data Transfer Optimizations
Lastly, consider how your wireless charging strategy can aid in data transfer. Charging stations are often developed with data transfer capabilities, so while your AGV or AMR mobile robots pause to recharge, they can exchange the information they’ve gathered during operation. The data exchange process enhances communication between the robot and the central control system, seamlessly transferring data metrics, software updates, task assignments, and more. This real-time data transfer means better visibility across your facility.
When robots are connected to a wireless charging system, sensor data can be transmitted, providing data analysis on changes within the facility or warehouse environment and route optimization plans. With this information, you can prioritize safety measures like collision avoidance, identify when proactive maintenance is needed, and improve system intelligence.
Charging for the Future
Adopting AGV and AMR solutions is a step forward for many facilities toward greater productivity and efficiency. While the benefits these robots offer are significant, many people treat the charging strategy for these solutions as an afterthought. Having touched on wireless charging today, there are several charging options businesses can consider. Whichever route you explore, it’s important to operate with your business needs and goals front and center. From there, you can make the best decisions to maximize the use of these automated solutions, increasing operational efficiency and improving business processes with reliable data.
Brian Cook is a Senior Product Manager at Conductix-Wampfler. With deep expertise spanning EV fleet management and charging infrastructure, Cook partners with engineers to bring new products to market faster. Prior to his role at Conductix, he served as Automation Project manager at Teledyne CETAC Technologies.
Comments (0)
This post does not have any comments. Be the first to leave a comment below.
Featured Product
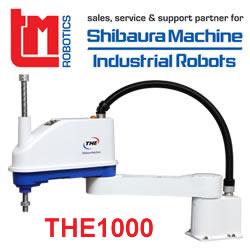