Robots are taking human roles – and SMEs need to be ready
A mantra often heard within the manufacturing and logistics industries is that robots are not taking the jobs of humans. And, in many ways, this is true. Today, automation is even a necessary solution to plug a shortage of human labour. However, this mantra can also be misleading. Robots may not be displacing human workers, but they are undoubtedly reshaping human roles – and companies, regardless of their size, must be ready for how this plays out. Paul Rivers, Managing Director, Guidance Automation, outlines how SMEs can introduce necessary new skills and prepare their workforce for the future.
Realistic outlook
In many warehousing and manufacturing facilities, robots are being introduced to enhance efficiency and productivity. Adoption amongst SMEs, however, remains slow – and this is a concern. Not only are SMEs missing out on the benefits that robotics could add to their operations now, they also risk falling out of touch with the influence that automation in the future will have on their human workforce.
Take automotive manufacturing as an example. More than 30 years ago, automotive manufacturers pioneered the introduction of guided vehicles and subsequently robot arms. Today, all companies in the sector rely heavily on this type of automation. And, while an automotive plant would have traditionally employed a workforce of thousands, modern plants can now operate effectively with just a few hundred employees supported by robot technologies.
Ultimately, this same trend will apply to warehousing and other manufacturing sectors. That’s not to say that a human workforce will no longer be required, but their roles will invariably shift. This will necessitate a new set of skills, primarily focused on robot repair, maintenance, and implementation. Plus, there is another layer of this story to consider. Automation comes at the same time as a new generation of workers with a different set of priorities. This is an interesting intersection that will impact how the economy will evolve – and that SMEs, even if they are not introducing automation now, need to be prepared for.
New skills
First, what are the skills that will become indispensable in warehousing and manufacturing settings? Technicians specialising in software programming of robotics, their customisation, installation, and electronics will all be highly desirable as companies introduce more robots into their workforce. Problem-solving skills will also become paramount to address new challenges and identify new ways to utilise automation and robotics to gain a competitive edge.
Then there is data analysis, which is key to problem-solving. The ability to collect, analyse, and make strategic decisions from data generated by processes like inventory management, human movement in warehouses, and order fulfilment will be a critical skill to bring in-house. For example, is stock in the right location to optimise flow? Do some workers move faster than others and can this data help to optimise human workflows? Businesses that have these capabilities can leverage insights to their own advantage, but perhaps more importantly, they can explore ways to monetise their data and introduce new revenue streams.
Building tomorrow’s workforce
SMEs need to consider how they will attract a future workforce with these skills while also working with the talent they already have. Within manufacturing and warehousing industries, workers often acquire essential skills by adding a practical element to their college or university-level education. Larger companies can more easily accommodate apprenticeships to support this. However, for SMEs, apprenticeships can be a significant investment with no guarantees the candidate will stay after their training comes to an end. Fewer SMEs offer apprenticeships as a result, which is a lost opportunity to understand and develop the skills their business will need.
T Levels, in this context, are a practical introduction to the industry that SMEs could consider instead. The investment is time, and even if the immediate return is limited, it could lead to a valuable recruitment opportunity in the long term. Imagine a scenario where a candidate presents their CV for an entry-level role, having completed a T Level in a relevant field such as electrical engineering or systems installation. This signals several desirable attributes, not least a genuine interest and enthusiasm, as well as an existing level of competence in the role.
Offering practical experiences is not only beneficial for an aspiring workforce. It is also advantageous for business leaders who want to understand the new skills their company requires and the new generation of workers who will fulfil them. This is an interesting time for manufacturing and warehousing businesses to navigate: aside from the shortage of labour, and the increase in robot workforces, there is also a noticeable shift in the mindset of today’s human workforce to consider. Lots of studies show how work priorities are changing with many choosing jobs that offer the best work/life balance or the most flexible working hours. This, of course, is complementary to automation in the workplace, so long as employers are forward-thinking enough to embrace new working models.
Does this mean the four-day week will take off? Will more free time mean a boom in leisure industry roles? We don’t have the answers, but we can be confident that big changes are coming and, as employers, we should keep an ear to the ground and be open to what they might be.
Team training
Finally, SMEs can start to consider the development of their existing workforce and seek out employees who are eager to learn and embrace new skills. This might mean providing training opportunities in-house or allowing them time off to attend relevant college courses.
Failure to invest in employees' skills and knowledge now could lead to their obsolescence as automation advances. Therefore, strategic planning and investment in employee development are essential to ensure a fair and secure transition into an increasingly automated environment. Not every employee will choose to return to formal education, but offering the option demonstrates a commitment to their professional growth. For the company, it means the opportunity to retain industry experience and reward loyal service.
Conclusion
Are robots taking human jobs? It’s not a simple yes or no answer, but one thing is for sure – robots are changing human jobs. While SMEs might only have one or two robots now (or perhaps none at all), they should take the opportunity to invest in their human workforce and ensure the skills they need to get ahead in an era of increasing automation.
About Guidance Automation:
Guidance Automation is an award-winning pioneer of autonomous mobile robot technologies.
Our suite of flexible and robust products is at the forefront of innovation, featuring autonomous material transportation, light-directed handling, and warehouse execution and control systems. We incorporate conveyors, sorters, robotic arms, and numerous other state-of-the-art automation technologies to deliver a comprehensive and bespoke solution for each unique business application.
Over three decades, we have helped hundreds of SMEs in the warehousing, logistics, distribution, eCommerce, and manufacturing sectors seamlessly integrate automation into their material handling processes to boost productivity and efficiency.
Our mission is to make automation accessible to all, not just large enterprises. With our support and expertise, we empower businesses of all sizes to create a hybrid workforce and embrace the future.
For more information, visit: www.guidanceautomation.com
Comments (0)
This post does not have any comments. Be the first to leave a comment below.
Featured Product
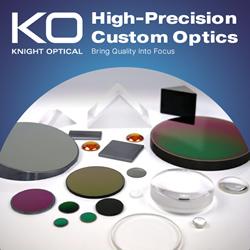