A remote solution to safety concerns - Remote controlled robots improve precision and worker safety
From bomb disposal and construction site monitoring to surveillance and firefighting, remote controlled robots allow humans to act in hazardous situations without putting themselves in harm’s way. Able to fit in small spaces and navigate challenging environments, these robots are being used in an increasing number of applications. Here, Dave Walsha, sales manager at small dc motor supplier EMS, explores how remote controlled robots can help to keep workers safe.
Unlike an autonomous robot, remote controlled robots do not have the ability to make decisions based upon sensor input. Instead, they rely on directions from human operators. Rather than limiting their utility, this allows remote controlled robots to be used in situations where human input and decision making is critical, such as in emergency situations, but the environment is simply not fit for human presence.
On the frontline
When there are survivors who need rescuing — from a collapsed building, for example — the safety of the emergency services must be considered first. If the environment is too dangerous, sending them in could result in the rescue team becoming casualties themselves. Remote controlled robots, however, can be deployed to give operators a clearer view of the situation at hand.
A UGV (unmanned ground vehicle) can explore the area without danger and send real-time images back to the emergency workers. They provide a more informed view of the disaster, improving decision making and increasing a victim’s chance of survival without first responders having to go in blindly.
Remote controlled robots are also routinely used to safely disable explosives. In many cases they will fire a high-pressure jet of water at the wires on the device, with the aim of breaking the circuit and rendering the explosive inert. If the worst case scenario occurs and the bomb explodes due to additional tamper protection in the device or any other issues, using a remote controlled robot means humans are kept well clear of the danger zone.
Hazardous industry
Using robots in industrial processes isn’t a novel concept — there are three million industrial robots operating in factories around the world. But in manufacturing, the focus is on getting factories as automated as possible, with the benefits of remote controlled robots largely overlooked.
A key advantage of remote controlled robots is their flexibility — they can easily be adapted to a range of tasks that cannot easily be programmed. For instance, maintenance and repair is difficult to automate because of the high degree of problem solving involved. Remote controlled robots allow complex repair tasks to be carried out, while keeping workers away from the most hazardous areas of the factory.
For example, flammable gases in the oil and gas industry create many potentially explosive environments. Sending a human into these areas to carry out maintenance and repair is risky, as the smallest spark could have disastrous consequences. Robots are already being used to carry out regular inspections of unmanned facilities such as those in the oil and gas industry, using a wireless network to communicate with a human operator located in a safe control room.
Elsewhere, robots are able to carry out maintenance tasks in the hard to access, hazardous and dirty environment of a water tube boiler. These boilers are commonly used in steam turbine power generation, but also in other industries such as chemical processing and paper manufacturing. Water is fed into the system and travels through tubes past a furnace to produce superheated steam.
If damage to these boilers, such as material corrosion, is left unchecked, there can be catastrophic safety implications and unplanned, costly interruptions to critical industrial processes. Therefore, regular maintenance of water tube boilers is highly important. Inspection robots can crawl along the water tubes and carry out visual inspections using a camera system. They then measure the thickness of the tube walls using ultrasonic thickness sensors and clean the tubes if necessary.
Dependable motors
When used in such extreme circumstances, remote controlled robots must be reliable — and so must their motors. EMS is the sole UK and Ireland supplier of FAULHABER motors, which are made in a finely controlled manufacturing process that ensures they perform with high repeatability and reliability. They also provide a high drive efficiency, resulting in a long battery life so the robot can continue its critical role until the job is done.
The motors need to be compact, so the robot can fit into tight spaces such as a collapsed building or in between industrial equipment. Low weight is another important requirement, allowing the robot to make quick and agile movements. Robots deployed in critical situations often have to force their way through debris, so the motors must exhibit high power.
FAULHABER motors are renowned for their unbeatable power to weight ratio. In particular, the BXT series can deliver torque up to 124 millinewton meters (mNm) from a 42mm diameter by 21mm long package thanks to its innovate winding technology. The multi-pole brushless motors are available in lengths as small as 14 millimetres, making them ideal for robots with small space requirements.
As safety continues to be a major priority, we’re expecting to see more and more remote-controlled robots to be deployed. And with the underlying technology advancing at a rapid rate, their applications are only bound to grow too.
Comments (0)
This post does not have any comments. Be the first to leave a comment below.
Featured Product
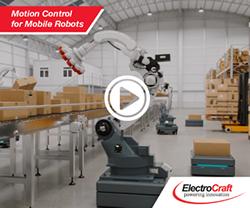