The Role of Robotics in Attracting Talent Back to the Warehouse
A persistent shortage of labour remains a major issue for the UK warehousing and logistics sector. Automation and robotics are proven to help businesses significantly improve productivity and increase efficiency. But automating manual tasks is only half of the story.
As fulfilment demand continues to increase, the way warehouses operate is changing. Still, a lights-out, or fully automated, warehouse operation is a long way off for many companies and SMEs. In most cases, robotics and automation will remain complementary to the work of human employees. Yet, not enough is being done to help companies in the industry secure the talent they need.
This is where robotics and automation can have a dual role to play in helping to address the labour shortage, says Dr Paul Rivers, Managing Director, Guidance Automation. Far from the industry deterrent that some might think, automated technologies can help change the image of warehouse work, while creating the environment to attract and nurture new talent.
Persistent Demand
UK businesses have reported a shortage of workers for almost two years now. Between September and November 2022, there were 50,000 vacancies in the transport and storage sector, adding to pressure on an already strained supply chain and its remaining workforce. Without change, these challenges will only intensify. When asked why they were unable to fill vacancies, almost half of businesses in the sector cited a lack of EU applicants. By 2030, economic inactivity related to population ageing is expected to rise by 2.4m, adding to higher turnover and fewer young people entering the workforce.
The UK government is coming under increasing pressure to provide more support; UKWA, for example, is lobbying to include sector roles on The Shortage Occupation List of the UK Immigration Rules. Automated technologies, especially autonomous mobile robots (AMRs), are also helping to provide quick relief from the pressures of persistent labour and skills shortages. Integrating just one or two AMRs can make a significant difference to operational efficiency, enabling companies to sustain productivity levels with fewer people. Designed to take on more onerous or simple jobs, such as transporting goods around the warehouse, AMRs can help free up existing staff to take on other roles. They can also pick up the slack during periods of peak demand when temporary workers are scarce.
But automated technologies are not a silver bullet. Contrary to popular belief, it is not often that companies introduce automation with the aim of replacing people entirely. Fully lights-out operations are still a way off, and won’t be the goal of every company, especially when considering 99.9% of the UK’s business population are SMEs. Within many warehouse operations, introducing automated technologies will always be about complementing and collaborating with existing staff. To overcome labour shortages, companies must therefore also consider why interest in warehousing and logistics as a viable and interesting career path is waning, and how they can leverage automated technologies to change this.
Employee Experience
Nearly every UK business has struggled to fill roles in the past year, with SMEs most affected. The Federation of Small Businesses recently found that 80% of small firms faced difficulties recruiting applicants with suitable skills. As warehouse operations evolve to incorporate greater levels of automation, an onus on training and upskilling existing employees is a must. However, there is also still a general lack of awareness outside of the industry of the important, varied, and rewarding roles on offer.
One of the main reasons industry employers are said to have difficulties retaining skilled workers and recruiting new staff is the demanding conditions. According to the HSE, workers within the transport and storage industry are amongst the most at risk of workplace injury. Staff shortages combined with rising fulfilment demand put even more pressure on existing staff, increasing the risk of dangerous mistakes.
Robots can play an important role in improving staff well-being by reducing the risk of manual handling injuries. By using robots to reduce the physical demands on staff, a company can create a safer and appealing work environment that is more likely to attract top talent with enjoyable, high value roles – such as data integration, planning, quality assurance and other tech-driven positions.
New Image
In addition to providing an improved working environment, robotics and automation can assist with improving the overall image of a company and the industry as a whole. Despite higher levels of automation and sophistication, it's still not seen as a career path for digital native generations. Younger generations also tend to prefer hybrid working environments, which warehouses typically aren't known for.
And yet, according to a recent study of Generation Z workers by Dell Technologies, 80% of respondents aspire to work with cutting-edge technology, and 91% say the technology offered by an employer would be a factor in choosing among similar job offers. What’s more, 51% believe that humans and machines will work as integrated teams, while 38% see machines as tools for humans to use as needed.
According to research from KPMG, businesses unable to demonstrate a meaningful commitment to environmental, social and governance values are also unappealing to younger prospective candidates. When looking for a new role, a third of 18-24-year-old respondents said they had turned down a job because the company’s ESG commitments did not align with their values. Automated and robotic technologies are an enabler for greater sustainability in the warehouse. Electric AGVs represent a cleaner material handling choice, while automated processes and the efficiency they add to operations, will ensure optimised energy use and reduced waste.
Conclusion
Overcoming the labour shortage will, in no small part, depend on a company's ability to meet the labour force’s desire to work with technology. Faced with persistent labour shortages and an ageing workforce, introducing mobile robots, for example, can instantly impact productivity while making the company more appealing to a wider pool of candidates. By working together with robots, human workers can take on new roles and responsibilities that are more fulfilling and rewarding. At the same time, companies improve efficiency, safety, and retention of their much sought-after skilled staff.
Comments (0)
This post does not have any comments. Be the first to leave a comment below.
Featured Product
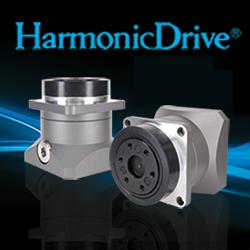