5 Compelling Benefits Of Automation In Your Warehouse
Warehouse management can be a complex task, requiring businesses to make the most of their available real estate while addressing a range of logistical challenges. To achieve this, many modern companies are turning to automation technology, which offers a range of benefits.
Automated conveyor systems, for instance, eliminate the need for staff to sprint across the warehouse — making narrower aisles and higher inventory stacking possible. Companies like DHL are investing heavily in warehouse automation, and collaborating with partners such as Locus Robotics to deploy thousands of robots in their warehouses.
As the adoption of robotics and IoT technologies continues to accelerate, warehouse automation is poised for sustained growth — with the global market expected to reach $93 billion by 2031, growing at a CAGR of 15.7% between 2021 and 2031.
The rapid expansion of the warehouse automation market is fueled by the diverse benefits that these technology solutions offer, and this article highlights just a few of the most compelling advantages.
1. Minimize human error
Once you set up an automation system, it will check off all the tasks you’ve configured and never make any mechanical errors that humans typically make.
For example, the person maintaining the warehouse inventory might commit a fat finger error even with a digital tool. Automating inventory records can help eliminate these types of errors completely.
Whether you’re a manufacturer, a D2C brand, or provide warehousing services — an automation system can help trim out human error from almost every process. Minimizing human error helps save:
-
Time: You save time you’d otherwise spend correcting mechanical errors.
-
Money: You save money you’d need to spend on undoing the damage caused by a mechanical error.
-
Reputation: You won’t have to answer tough questions from customers that can blemish your reputation.
2. Increase productivity
Growing demand might encourage you to put more people in the distribution center (DC). The result? Low space per person and increased costs. The lack of planning, space, and adequate training translates to poor ROI, and in some cases, cost overruns.
Instead, you can let machines take care of the repetitive tasks — they perform tasks faster and more accurately. You won’t have to hire more people because of an automatic reaction to an abrupt demand surge and you’ll free up your current team’s time to focus on more strategic tasks.
Companies like ASOS are already investing heavily in automation to increase productivity. The UK fashion retailer invested $100 million towards automating its warehouse in Georgia, which the company expects will increase the capacity up to 50%.
Besides that, DHL is investing heavily in warehouse automation, and collaborating with partners such as Locus Robotics to deploy thousands of robots in their warehouses.
3. Optimize space use
Some of the biggest companies in the world are employing automation to optimize space use in their massive warehouses. As McKinsey highlights in one of its articles, Edeka (Germany’s largest supermarket corporation) invested €93 million to expand its Berbersdorf warehouse and added 300,000-square-foot of partially automated picking-and-storage area.
If you’ve already stacked pallets as high as your forklift can reach, there’s little you can do to optimize space use without automation. However, with automation, you can squeeze aisles closer together and replace a manually operated lift system with an automated storage and retrieval system (AS/RS).
AS/RS can stack and pull out pallets from an entire aisle. When you don’t have to reserve space for staff to walk around and pull items off the racks, you can bring the aisles closer together and using more vertical space.
4. Fewer safety hazards
Safety has been a big concern for the warehouse industry. The Bureau of Labor Statistics reported 46 fatalities per 100 full-time workers in 2021.
The constant lifting and stretching can stress the human body, leaving it vulnerable to injury. Injuries may start as a sprain or pulled muscle, but constantly putting the body under stress can be a recipe for chronic, painful conditions that last a lifetime.
Automating repetitive and labor-intensive tasks can help minimize staff susceptibility to injuries. Let robots pick up heavy pallets or handle harmful chemicals while your staff monitors them.
Your staff will also appreciate automation technology that improves safety — greater safety is the number one factor making warehouse employees feel optimistic about automation technologies.
The article quotes Yanis, a France-based forklift operator:
“I used to be on sick leave several times due to severe back pain. The automated forklift truck has improved the most important aspect of my physical health.”
5. Effective inventory management
Managing inventory is critical to ensure you always have enough stock. Running out during peak season can hit your bottom line hard. Most businesses invest in inventory management software that requires manual effort, but what if you could put it on autopilot?
Applying artificial intelligence (AI) and machine learning (ML) to inventory data can automate inventory-related decisions. For example, the algorithm assesses your inventory needs throughout the year and triggers notifications to restock.
That’s precisely what Ocado (the world’s largest dedicated online grocery retailer) did. The company managed to minimize food waste to an impressively low figure of 0.02%. The company uses automation, robotics, and proprietary software to manage inventory and ensure minimal waste.
The ROI on warehouse automation
As AI and ML mature, new IoT devices enter the market, and warehouse managers try to minimize costs, automation will drive warehouse management into a digital future. At face value, implementing warehouse automation might seem expensive. However, the returns are impressive — you’ll be more resilient to fluctuating market demands and labor shortages.
According to a report by the Boston Consulting Group, leading companies have automated their warehouse networks and generated a 20% to 50% reduction in fulfillment costs. Wouldn’t you consider automating your warehouse if you could reduce your fulfillment costs by over 20%?
Will Schneider is the founder of InsightQuote, a match-making service for B2B services, and writes informative posts about fulfillment services at Warehousing And Fulfillment. He is passionate about helping businesses find the right solutions to improve their operations. When not working, Will enjoys coaching youth basketball.
Comments (0)
This post does not have any comments. Be the first to leave a comment below.
Featured Product
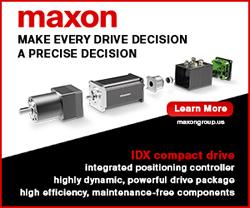