Safely Integrating Robots and AI Into Your Warehouse Workforce
With every year that goes by, we are seeing an increase in robotics and Artificial Intelligence capabilities within our companies and our workforce, and this is especially true in America’s warehouses. There are endless possibilities for what robots and computer technology can accomplish, which is why so many developers are getting into the robotics industry.
However, while integrating robots and AI into our warehouses can help with production and quality assurance, care must be taken when this tech is first introduced. Managers need to familiarize their employees with these innovations and take the proper preventive steps so that their human workers are safe. Let’s talk about the importance of robotics and AI and how you can introduce them into your warehouse as easily and safely as possible.
The Benefits Of Innovation
In order to successfully introduce robotics and AI into your warehouse, you first need to understand how valuable this tech can be to your product. For starters, when a robot or piece of AI software is properly programmed, then the chance of error while completing tasks drops dramatically versus human capabilities. Human error can happen more often than we would like, and if it does occur, it could negatively impact profits. If your warehouse handles highly detailed work, robotics could be a lifesaver.
Technology is also very adaptable. With a few keystrokes, a programmer can increase operating speeds to meet increased productivity requirements. Robots can also work longer hours without stopping or needing sustenance, and they can maintain their quality standards even if they work around the clock.
Because of all of these benefits, your warehouse is likely to see higher customer satisfaction ratings and better reviews for your services. When you mention that robotics will soon come to your workplace, you are destined to hear employees fear that they will be replaced, but it is important for management to advise them that robots can take some of the stress off of their shoulders, and when your warehouse is more successful, then your employees can have better job security, which is important.
Prepare Your Workforce
When your organization does decide to introduce robots and AI into the fold, the first step is to talk to your employees and show them how the technology operates so they can understand the functions and be safe when they are near these devices. This is very important, so instead of sending out an email blast, have all of your employees come in for an in-person meeting. During that presentation, show them the robot in action so they can see how it moves, its components, and how it can potentially cause harm. Make sure to leave plenty of time for questions. By seeing it in person and in a safe environment, they will know what to watch out for when out on the floor.
To ensure that all new workers are aware of the safety precautions necessary around this new tech, ensure that these talking points are a major part of your employee onboarding process. This training should include lessons on how to work alongside robots, tips for working with AI and when they may come in contact with the tech, and a general overview of how these advancements fit into their workflow. While initial education is important, human resources and managers should make it a point to check in with the employees again down the road to gauge their understanding and ask if they have follow-up questions.
This is also a good time to educate your staff on how robots can make their work easier and safer. For instance, robots can lift very heavy loads, which is often required in a warehouse environment. By avoiding this heavy lifting, your employees can protect their backs and joints. Also, robots can work in cramped spaces where humans may not be able to fit and still keep up the same level of productivity, sparing the employees from having to work in a dangerous position.
Aim To Prevent Safety Issues
Employee education is just one part of the equation when it comes to safety with robots. Management needs to know all of the risks so they can take the proper preemptive measures to avoid any issues. For instance, if this is your warehouse’s first foray into AI, then consider starting small and setting up a pilot program where you introduce the tech to a small section of your business. From here you’ll see how it works and if there are any bugs to work out. Once you are sure that the tech will be efficient and safe, then you can launch it throughout the company.
It is also important to remember that machines require electricity, so you will need to be aware of the physical dangers of robots, such as tripping hazards like cords and levers. Some robotics also require high-voltage systems, and if an inexperienced worker isn’t careful, they can be electrocuted. Study the likelihood of these threats and focus on creating a workplace that accommodates both human workers and robots alike.
Finally, it is important that you always keep your employees in the loop and aware of potential dangers by hanging signage and posting warnings whenever possible. If any of the robots have moving arms, then use floor marking tape to mark areas that are off limits so an employee isn't struck. To further prevent an issue, you can install sensors that will detect when a human is nearby and automatically shut itself down if there is a risk. Of course, have it put in writing that only authorized personnel are to operate the technology and have each employee sign with their understanding.
In the end, robotics and AI are here to stay, so it is time to start thinking about how you can implement these innovations in your warehouse. When you do, consider the tips mentioned here to ensure that humans and technology can work together safely.
Comments (0)
This post does not have any comments. Be the first to leave a comment below.
Featured Product
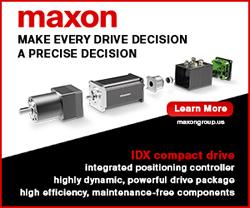