Cobots — electric or pneumatic?
As a famous advert warned, “power is nothing without control”. For more than two decades, cobot manufacturers have strived to offer the perfect combination of power and control, a delicate balancing act that requires many considerations, not least the cobot’s power source. Now, the release on the market of the first all-pneumatic cobot further enriches the complex cobot market. Here Claudia Jarrett, US country manager at automation parts supplier EU Automation, offers an overview of the benefits of electric and pneumatic models.
The impressive growth of the global cobot market shows no sign of slowing down. According to the consulting group Next Move Strategy Consulting, it is projected to grow from 2020 to 2030 at a compound annual growth rate (CAGR) of almost twelve per cent, reaching almost two billion US dollars by 2026.
Cobots have quickly become a favorite in manufacturers’ arsenal of powerful automation technologies — versatile, cost-effective and inherently safe, they enable true human-machine collaboration and remove the need for cumbersome robot cells and safety fences.
One of the latest additions to the rich cobot landscape comes from Festo. It is an all-pneumatic cobot, the first of its kind, which has recently been unveiled and is expected to be available on the market from Autumn 2023.
Instead of the typical electric motors and mechanical transmission, Festo’s new cobot features six pneumatic direct drives that consist of a circular chamber with a moveable partition. Differences in the air pressure on either sides of the partition cause the joints to move.
It’s always exciting to see the latest innovations reach the market, but what are the benefits of this new set up for manufacturers? And when are traditional electric cobots still the best choice?
Precise, agile, safe
The pneumatic cobots contain six rotary actuators in their base, eliminating the need for external motors and control cabinet. This makes them incredibly light and versatile — with a weight of only 17 kilograms and no need for additional hardware, they can be easily moved by one person.
Pneumatic cobots are also very safe. Their pneumatic system regulates pressure in the joints when the machine senses an imminent collision, reducing the torque to zero. Their soft-touch technology also means that in case of impact, the cobots are as soft as contact with a human being.
Another advantage is that pneumatic drives are known for allowing smooth movements, compared to the stiffness that characterizes robots powered by large, heavy motors. This allows the cobots to move in a fluid and extremely precise way.
Moreover, the simple design of pneumatic systems mean that the cobots are expected to be more durable and require less maintenance than their electric counterparts.
Finally, one benefit that pneumatic and electric cobots share is low-code programming, which facilitates set up for less experienced users. According to Festo, pneumatic cobots can be ready to use in less than an hour for some applications, and even users with no programming skills can take advantage of their guided configuration mode to manually program movements.
The limits
Despite the many advantages of pneumatic cobots, there are still situations where electric alternatives might be preferable. It is the case, for example, of applications that require precise and rapid tweaks of speed. Pneumatic systems allow for limited speed control compared to their electric counterparts, which offer complete motion control, including the option to program them with custom speeds.
Another typical drawback of pneumatic systems is that the compressed air used to power them contains water, which can build up in the pipes and affect the functionality and lifespan of cobots. This can also be a problem in freezing conditions, such as those that can be found in some food and beverage applications.
Finally, pneumatic actuators are best used in light and medium-duty applications, but might not be powerful enough for heavy-duty applications, where an electric alternative might be more suitable.
What do you think of pneumatic cobots? Do they inaugurate a new era of perfect balance between power and control, or do you prefer to stick to traditional electric models?
For the latest updates on the world on industrial automation, and to order a variety of quality automation components, visit www.euautomation.com.
Comments (0)
This post does not have any comments. Be the first to leave a comment below.
Featured Product
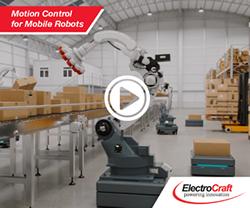