Robotic Welding Trends for 2022
Like most manual and fabrication processes in the digital age, welding has been enhanced and improved by technological concepts such as automation in recent times.
In fact, the global robotic welding market peaked at a value of $5.450.5 million in 2018, while this figure is set to increase further to $10,784.4 million by 2026. During this period, the market will grow at a CAGR of 8.7%, highlighting the growing influence of robotics on welding applications.
But what are the main robotic welding trends to look out for in 2022? Here are a few to focus your attention on:
#1. Improved Speed and Precision With Robotic Welding
Ultimately, there are numerous benefits of robotic welding, from improved efficiency and deployment of skills to creating considerably safer and more realistic training environments.
It’s also clear that robotic welding can enhance precision and the consistency of workmanship (even across complex applications), while simultaneously increasing output and the number of parts welded every hour.
This is underpinned by a concept referred to as ‘adaptive control’. Based on cutting edge technology and the principles of machine learning, adaptive control draws on welding data from different robots. This is then logged and subsequently analysed to identify ways in which processes can be enhanced going forward.
Adaptive control can leverage some granular datasets, such as the voltage of machines and the level of resistance incurred during welding. Other factors such as temperature are also considered, with a view to creating adaptive robots that continually operate in optimal conditions.
These datasets are then reviewed to identify specific improvements, especially those pertaining to the speed and precision of operations.
Typically, individual adjustments save robotic welding controls milliseconds, but adopting this approach across the board can deliver significant gains in speed, accuracy and efficiency over time.
#2. Ushering in the Age of Industry 4.0
The term ‘Industry 4.0’ refers to the Fourth Industrial Revolution, which conceptualises the rapid pace of technological advancement and the wider impact of interconnectivity and smart automation across a broad range of industries.
Of course, the global coronavirus pandemic has accelerated the impact of Industry 4.0, as businesses have sought to embrace digitisation and create a more resilient value chain that safeguards against future disruptions to their operations.
The term ‘value chain’ is used to describe the various activities that contribute to a business’s operation, which may include welding applications and key tasks that help to create specific products.
Because of this, robotic and automated welding is thought to be at the front and centre of enabling Industry 4.0, as it has already begun to transform various applications and industries through the deployment of cobots (which are collaborative robots that work alongside humans in a shared space) and ‘plug and play’ automation systems.
In this respect, Industry 4.0 is already here, while advancements in robotic welding will continue to drive this revolution further by negating the need for complex industrial R & D and allowing businesses to focus on execution and delivering far greater efficiencies.
#3. Bridging the Skills Gap Through Cobots in the Short-term
While the demand for workers in the global welding industry continues to rise, there remains a widespread shortage of skilled operatives.
In the US alone, the American Welding Society has predicted a total deficit of 400,000 welders by 2024, with this triggered largely by an ageing workforce and the distinct lack of younger welders making their way within the industry.
Of course, robotic welding has been positioned as a way of bridging this considerable gap, both from the perspective of providing immersive training to the next generation of welders and optimising productivity while the shortage of skilled workers persists.
However, the fact remains that this technology is still in its infancy, while there is currently a significant shortage of skilled robotic welders as the industry continues to mature. So, the use of cobots may provide a more viable solution in the shorter-term.
As we’ve already touched on, cobots are collaborative robots that leverage artificial intelligence to work alongside humans. Conversely, robots are autonomous and completely intuitive machines that perform tasks without human control, and require a much bigger evolution in terms of how a business operates.
Of course, cobots generally have a lower payload capacity than traditional robots, while the speed of their movements and actions is considerably slower when compared to robots.
However, a reduced payload capacity shouldn’t be much of an issue for most welding applications or instances when the welding gun is lightweight, while their relatively compact and lightweight nature enables them to be moved seamlessly around the workplace and provide optimal coverage across a reduced workforce.
Make no mistake; cobots can help to boost the efficiency of human workers and affordably bridge the short-term gap created by a global welder shortage.
This also allows time for robotic welding to develop further and provide a longer-term solution to the industry’s labour imbalance.
The Last Word
As we can see, robotic welding remains a relatively nascent concept, and one that will continue to mature in the months and years to come.
However, it’s already being embraced on a much larger scale across multiple industries, contributing to enhanced operational speed and precision and helping to usher in the age of Industry 4.0.
At the same time, associated technologies such as cobots are also helping to bridge the welding skills gap and enabling operations to embrace robotics more gradually over time.
Comments (0)
This post does not have any comments. Be the first to leave a comment below.
Featured Product
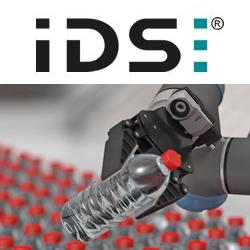