How to Successfully Implement Automated Warehouse-Picking Robots
Automated warehouse-picking robots can generate invaluable increases in productivity and efficiency, but only with the right implementation strategy. Integrating these bots into any setting requires research, preparation and strategizing beforehand. This is especially true for organizations that have not used order-picking robots before.
A new robotics implementation may deliver improved results if as the proper groundwork is in place. Luckily for those looking to introduce this technology, companies can take concrete steps to ensure they have the best chance of success with their warehouse robotics integration.
Identify Key Areas for Automation
Before inquiring about any robots or prototypes, organizations need to survey their warehouse operations carefully. One of the keys to successfully implementing automated order-picking robots is integrating them in the right places. Just as different types of cars are better suited to certain roads, some warehouse robots may be a better fit than others. The only way to know what type of robot would be the best fit is to clearly understand what needs to be automated.
Businesses need to analyze their current operations to identify areas that could benefit from automation. For example, an online retailer might want to reduce its shipping speed by two days on every order. Automation can help with this. In fact, accelerated delivery times are one of the top benefits of an automated warehouse. The question is, what part of the order fulfillment process needs it?
A thorough efficiency analysis might reveal the retailer’s item picking process is a severe bottleneck. With that knowledge in mind, it can safely hypothesize how automated order-picking robots could make a big difference. Likewise, stationary pick-and-place robots might be a better fit if the order packing process caused the bottleneck. Establishing specific concepts and goals like this will build a concrete foundation for an organization’s warehouse robotics strategy.
Choose the Right Warehouse-Picking Robots
Companies can move ahead with robot selection once they’ve identified specific automation applications. This process may take time, but it’s essential to do as much research and testing as possible to ensure they choose the right robot or combination of robots.
It’s a good idea to take note of any features working particularly well for an organization’s unique situation while exploring and testing different models. Maybe one robotics provider integrates well with the legacy systems in place or has an easy-to-use programming interface for the robots. Certain features like these will likely determine which bot is the best choice between similar models.
Many different models of warehouse-picking robots are available today. However, the items a company wants the robot to pick will help narrow things down. For example, BionicHIVE designed the SqUID robot specifically for picking rectangular boxes. Other robots, like autonomous forklifts, might be good for moving even larger items. There are also collaborative bots that work alongside humans, which can be an ideal strategy in many warehouses.
Order-picking robots generally fall into two categories — collaborative (cobots) or fully autonomous. Most non-collaborative warehouse robots are either AGVs or AMRs. These types of machines are similar but differ in how they navigate. Autonomously guided vehicles (AGVs) require a navigation system, such as metallic strips or rails. They stay confined to these laid-out paths but can autonomously move along them. Autonomous mobile robots (AMRs) can move freely, typically using some combination of LiDAR, AI, cameras and sensors.
Cobots include various meet-me, follow-me and other goods-to-person robots. They may not be the best option for all businesses, but they are often a great way to improve the efficiency of human teams without replacing employees altogether.
Preparing for Order-Picking Robot Integration
Organizations must set themselves up for top performance for a warehouse robotics integration to be successful. This involves organizing the space where the robot will operate, providing training for employees and establishing necessary safety measures.
Companies should take stock of the space they intend for the warehouse-picking robots to work. This will depend entirely on a business’s unique space and the robots they adopt. However, some general rules of thumb include clearing enough open space and setting up safety barriers as needed. If the bot is part of a larger automated packaging line, where will they situate it? Verify that no objects or structures could get in the robot's way and cause an accident.
Some robots may need enclosure so employees can’t accidentally wander into a dangerous area while they are operating. Additionally, it is worth considering the warehouse layout in terms of traffic flow. Proper traffic management can make a big difference in the efficiency of AGVs and AMRs.
Training is a crucial but often-forgotten part of implementing automated warehouse robots. Employees will need basic safety training to work around any order-picking bots. They may also need operational training depending on the nature of the machine. Inclusive training is critical to ensure that no one accidentally impedes the successful operation of robotics. It also assures workers know what to do in an emergency or accident involving a robot.
Integrating in Stages
Integrating in stages is a good idea when the time finally comes to put the new warehouse-picking robots into action. This doesn’t necessarily mean rolling things out slowly. It simply entails integrating only one or two new types of robots at a time and analyzing their performance before adding more. A pilot program with only a few may even be a good idea for organizations new to robotics.
Integrating automated warehouse robots in stages allows businesses to refine their approach and pinpoint issues early. For example, suppose the previously mentioned online retailer adopts five types of order-picking robots. In that case, it can choose to either introduce them all on the warehouse floor at the same time or just start with two. Any unusual results or issues will be harder to diagnose if it launches all five at once.
It is far easier to tell what is causing any performance problems when fewer new variables are at play.
Analysis and Optimization
Ongoing success relies on reflection and continuous improvement throughout the stage of robotics integration and beyond. After all, Amazon has arguably the most successful implementation of warehouse robotics worldwide. It continues to update, optimize, improve and adjust its robotics integrations. Every organization can benefit from regular analysis of their warehouse-picking robots. Ultimately, it will lead to better performance and better ROI.
Regardless of the technology used, warehouses should follow performance metrics as consistently as possible. Some companies prefer to track this manually, while others automate the process using AI data-analysis algorithms. This information can reveal ways to optimize performance and boost efficiency.
For example, AGVs may take longer than necessary due to inefficient routes throughout the warehouse. Businesses can use data to find bottlenecks and areas for improvement to ensure they make the most of their robots and build the strongest warehouse automation strategy possible.
Implementing Warehouse-Picking Robots Smoothly
Successfully implementing automated order-picking robots can be easy with the right approach. Preparation is often the most critical part of the process, long before new machines hit the warehouse floor. Integrating in stages and continually analyzing and refining implementation can ensure ongoing success. With these tactics in mind, any organization can elevate its operations with the help of cutting-edge warehouse robotics.
Comments (0)
This post does not have any comments. Be the first to leave a comment below.
Featured Product
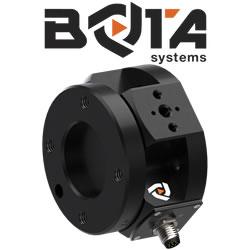