The Future of Robotic Exoskeletons: Roadblocks and Recent Advances
Exoskeletons, or wearable robotics, were a thing of fiction until very recently. Now, they exist not just in prototypes but in action, seeing service in heavy industries, physical rehabilitation and other sectors. As more people realize the technology’s benefits, exoskeletons could be a $5.4 billion industry by 2028.
Here’s a look at where the field is now, its current challenges and where it’s headed.
Current Exoskeleton Uses and Obstacles
Exoskeletons have remarkable potential. As with their science fiction counterparts, these machines can amplify their users’ strength, letting them lift heavier objects with less effort.
Construction and other heavy industries have started using them for these advancements, with some companies seeing a 50% reduction in muscle activity, preventing injuries.
Wearable robotics have also shown promise in the medical industry. Powered frames around patients’ legs can help some people rebuild their strength after an injury. These technologies could also give patients who previously used wheelchairs the ability to walk on their feet.
Despite these tremendous benefits, exoskeletons face some challenges today. Here are the most pressing.
1. Power
For exoskeletons to be a viable option for commercial adoption or some workplace uses, they need to be portable. That presents a challenge in terms of how to power the robotic elements. Wired options limit exoskeletons to indoor or confined spaces, and batteries can be heavy or offer limited operation time.
Exoskeleton power supplies must be light, reliable and long-lasting. That combination of qualities is difficult to achieve, especially affordably, as the high cost of electric car batteries exemplifies. Until researchers can find a solution to this issue, though, wearable robotics will have limited utility.
2. Cost
Another limiting factor of today’s robotic exoskeletons is their cost. Some medical exosuits can cost $80,000 per unit, and even “affordable” options cost as much as $30,000. Advanced medical facilities and large-scale industrial operations may be able to justify those expenses, but prices must drop to enable widescale adoption.
The advent of robotics-as-a-service (RaaS) can mitigate these high costs for industrial applications, enabling facilities to rent instead of purchasing them outright. Still, these models don’t work well in consumer applications. Users with mobility restrictions, for example, need to own their exoskeletons, not rent them, but prohibitive costs stand in the way.
3. Comfort and Range of Motion
While wearable robotics can prevent many strains and injuries, they’re often not comfortable. They can be heavy and awkward, and the way they strap onto users’ bodies can cause uncomfortable or even painful friction. Discomfort is preferable to injury, but these technologies likely won’t appeal to the masses until they’re more comfortable.
Similarly, exoskeletons today often have a limited range of motion. Most use fixed-axis rotating hinges for their joints, but this doesn’t accurately mimic how human limbs move. As a result, users’ mobility in an exoskeleton doesn’t reflect natural movement, limiting its versatility.
Recent Exoskeleton Advances
These obstacles are significant, but exoskeleton technology has come a long way in a relatively short time. In the past few years, there have been several advances that are pushing these robotics forward. Some of these innovations could provide solutions to the technology’s most prominent challenges.
Wearable robotics is still a new technology, so there’s much room for growth ahead. Here are a few recent advances that provide a glimpse into exoskeletons’ promising future.
1. Soft Exoskeletons
Many exoskeleton companies have leaned away from rigid, metallic exoskeletons recently. Soft exoskeletons, consisting of fabric and flexible, artificial muscles, offer multiple advantages over their metal counterparts. Most notably, they can be far lighter and offer far more range of motion, making these tools more useful.
New soft materials like microlattice don’t sacrifice safety to achieve these benefits, either. Microlattice can slow blunt impacts by 21.7% despite its light weight, making soft exoskeletons a viable tool for workplace protection. Since these exoskeletons look and feel more like clothing than an external frame, they’re also more comfortable, enabling longer usage times.
2. Passive and Pseudo-Passive Exoskeletons
Other recent exoskeleton advances may provide an answer to the problem of power consumption. Passive exoskeletons don’t use electricity at all, instead using mechanical energy to assist their users. For example, they could use a metal frame to redirect weight to prevent strain or springs to absorb shock.
A similar solution is to use pseudo-passive designs, which inject small amounts of power to bolster otherwise passive exoskeletons. These alternatives only deliver power as needed and use mechanical advantage to reduce what energy they need. As a result, they can operate with smaller motors and run for longer, maximizing energy efficiency.
4. Alternative Power Sources
Another possible solution to the energy issue is to replace traditional batteries with alternative power sources. Some exoskeleton companies have started looking into using built-in solar panels to provide the power they need. As solar technology becomes more efficient, this becomes a more viable solution for exoskeleton power.
Kinetic energy from users’ own movements presents another possibility. There are already wearables that draw power from movement, so similar technologies could bring this alternative energy source to exoskeletons. Current kinetic energy harvesting devices don’t generate much electricity, but they could help extend battery life, especially in pseudo-passive designs.
5. AI and Smart Sensors
Artificial intelligence (AI) and connected sensor technology have started to break into exoskeleton design as well. In these designs, sensors throughout the wearable robot gather data on its current use and the users’ physiological state. AI then interprets this data to adjust the exoskeleton as necessary to deliver optimal performance.
Some researchers have created exoskeletons that adjust their torque to optimize users’ running and walking economy based on metabolic data. Such devices could help reduce repetitive strain injuries in workplaces or improve patient outcomes in physical therapy. Wearables that gather this type of data are already commonplace, so incorporating them in exoskeletons is a natural next step.
We’ve Only Scratched the Surface of Exoskeleton Technology
Today’s exoskeletons are already impressive, but these recent innovations show how much further the technology can go. As more organizations implement these technologies, funding for exoskeleton research will grow, leading to more improvements. Today’s wearable robotics use cases are likely just the tip of the iceberg.
It could be a long time before exoskeletons are commonplace, but it will likely happen eventually. The technology is too promising in too many potential applications for organizations to dismiss it. As exoskeletons start to overcome their current obstacles, they can start reshaping their areas of implementation.
Comments (0)
This post does not have any comments. Be the first to leave a comment below.
Featured Product
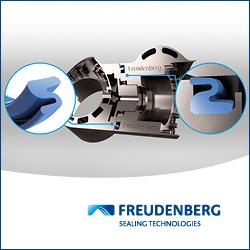