The sense of touch - Tactile technologies for cobots
Cobots have been developed to a point where the only thing differentiating them from their human co-workers is soft-skills. Cobots developing adaptive capabilities, like decision-making or problem-solving, is challenging for engineers although progress is inevitable. With state-of-the-art sensors, actuators and software, cobots are now capable of experiencing physical sensations, allowing them to feel and identify an object being touched. Here Claudia Jarrett, US country manager at automation parts supplier, EU Automation, discusses the advantages of tactile technologies for cobots.
The first cobot was manufactured in 1996, designed for basic pick and place applications and communicated with operators using motion resistance. Cobots have since come a long way towards supporting humans’ work in a safe way. They are now able to detect objects and people in their environment using vision sensors and can even slow down, or stop functioning, in case of an unintended contact.
Modern cobots also possess the ability to take corrective actions and minimise risks, but sophisticated models take a further step in imitating human-like problem solving. Touch sensing technologies are quickly evolving to increase both the applicability and safety of cobots, especially in demanding applications that require handling delicate materials safely and precisely, such as healthcare.
Preventing collision
Currently, there are several tactile sensors used in cobots, including piezoelectric, piezoresistive, capacitive and elastoresistivity types. Piezoelectric technologies are used for gathering data from the cobot’s joints and transmitting it to the controller. On the other hand, capacitive sensors can act as proximity sensors, allowing the cobot to slow down when it detects the presence of an obstacle.
Most detection sensors are placed outside of the cobot, such as area sensors, that enable the machine to slow down or stop when human workers are close to it. Although collisions might still happen, these technologies ensure that the impact is minimized. To make navigation more reliable, tactile sensors may be embedded at the end of the cobot arm, just like in a human arm, and equipped with artificial intelligence to always avoid collision and allow the cobot to move more efficiently.
Precise object handling
Tactile sensors can also be used to identify the features of objects and recognize defects and changes. For example, early research from the USC Viterbi School of Engineering used embedded tactile sensors with conductive fluid to simulate human touch, resulting in a robot differentiating between the texture of wool and that of cotton.
Modern touch sensing systems use tactile sensors to gather different information about an object, such as shape, size, texture and transmit an electrical signal to the controller. They then measure the real characteristics of the objects producing accurate information. This is helpful for defect detection at a deeper level, by being able to spot issues with the texture of objects.
These sensors are also valuable for precise object placement, when loading parts into a fixture for machine tending. The sensing technology can find the exact part location and correct changes in the position or size of the raw stock material by measuring the insertion force.
With a more effective sense of touch, cobots could be used in applications where they interact with more fragile or deformable objects. One possibility could be using tactile technology in surgical cobots to enhance precision and accuracy. For this to be successful, multiple tactile sensors would have to be integrated using AI and machine learning.
Advancements in tactile sensors for cobots allow humans and machines to perform increasingly complex tasks in a collaborative environment to achieve more productivity and accuracy. An agile work environment that plays on the strengths of automation is key to a successful business. At EU Automation we encourage the development of automation technologies and help manufacturers reduce downtime by sourcing components safely and timely.
Find out more about our services at www.euautomation.co.uk.
Comments (0)
This post does not have any comments. Be the first to leave a comment below.
Featured Product
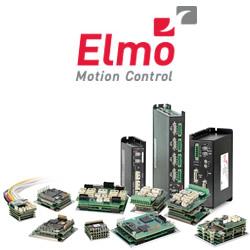