Robots in the factory: bosses or slaves?
In the 1990s, could you have imagined the rise of the self-service checkout? This twenty-first century phenomenon is now a common sight in most supermarkets, and despite a few challenges — and more than a few “unexpected item[s] in the bagging area” — they are a change largely for the better. Like self-service checkouts, industrial robots benefit end-users and businesses. But, what about workers? Nigel Smith, managing director of robotics supplier TM Robotics, argues the case for worker-friendly robots.
Industrial robots have long had a reputation problem. In fact, distrust in automation has led to slow adoption in some countries. Even in the US, the International Federation of Robotics’ 2019 report found that adoption rates were 49 per cent below what was expected.
Change is coming
Industrial robots excel at tasks that are repetitive. Moving faster and more precisely than their human counterparts, they can drastically increase productivity levels. Shibaura Machine’s THE SCARA robots, for instance, offer a cycle time of just 0.39 seconds. These repetitive, manual tasks are the same ones that human workers often find dull and physically demanding — not to mention potentially dangerous.
The same can be said for difficult, dirty, or hazardous environments — human workers may be at higher risk of injury in these kinds of work environments, while robots will be unaffected.
Removing workers from these tasks frees humans up to take on more meaningful and fulfilling work. In fact, the World Economic Forum (WEF) predicts robots will displace 75 million jobs globally by 2022 but while doing so, will create 133 million new ones.
But, what do these new roles look like?
Automating for growth
Grabit, a start-up using electroadhesion for materials handling, uses the Shibaura Machine THL1000 SCARA robot for footwear assembly. The technology can assemble the uppers of Nike trainers at 20 times the pace of a human. Bad news for humans, or so you would think.
When production capacity is increased so exponentially, the rest of the businesses operations needs to adapt to reap the full benefit. There’s no advantage to manufacturing20 times as many shoes without the staff to quality check, package, deliver and market these goods.
That’s not to mention the additional work required to installing and maintain robots. Installing this technology will also generate additional factory floor jobs, such as design, maintenance engineers or software engineers.
While some factory floor roles will be lost to the rise of robotics, expanding businesses need to hire in other areas in order to keep up with demand.
TM Robotics can supply 6-axis, SCARA, or cartesian robots designed for a variety of applications and environments. As distribution partners of Shibaura Machine, formerly Toshiba Machine, they have over 20 years of experience supplying industrial robotics and understand that each application needs a unique approach. For those new to automation, they now offer online training sessions with their robotics experts, to help you improve your ability to work with industrial robots.
New technologies bring change, whether industrial robotics or self-service checkouts. While some tasks may be reduced, new roles will also be created because of automation. Robots do not simply replace humans but are a tool we can use to make manufacturing easier and more efficient; they work for us, not the other way around.
To take the first steps towards automating your manufacturing business, contact TM Robotics via info@tmrobotics.com for a free online consultation. Or see the full range of Shibaura Machine robots here.
Comments (0)
This post does not have any comments. Be the first to leave a comment below.
Featured Product
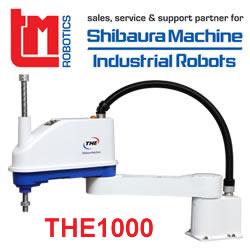