How to Simplify the Integration of Robotic Automation
Robotic automation has had a significant impact on the manufacturing sector. Enlisting a robotic workforce to take over more repetitive and dangerous jobs has enabled plant managers to re-allocate their human workforce towards more valuable tasks, such as setting up new machines, writing PLC programs, and assembling parts. This not only helps companies to better leverage the skills of their employees, but to also create more meaningful employment opportunities.
Automation technology installed right out of the box is not an immediate path to increased profits - successful integration is key. This article explores the main principles that align the integration of robotic automation and success.
Data Integration
When you think about automation, the image that may come to mind is one that includes dozens of precisely moving robotic arms as they busily assemble complicated products along an assembly line. As valid as that image is, it really is only half the picture.
As much as robotic automation relies on physical hardware to perform tasks, it is almost equally about information. Automation, after all, would not be possible if it weren’t for the data that is fed into, analyzed and used by the system. This data, however, is not always easy to obtain even when it all exists under the same roof. Oftentimes, when a manufacturer is transitioning their operations to include more autonomous equipment, the data that is needed for a seamless integration is trapped in silos of differing systems that have no way of sharing data with one another.
Unfortunately, gutting and replacing these systems can be cost prohibitive, which in turn can act as a barrier to entry into more autonomous operations. In order to successfully deploy robotic automation, the automation process needs to be able to pull any relevant data collected by any associated device into the workflow. Once the process is complete, the resulting new information must be pushed back to those same systems and devices so that all systems of record will be up to date.
Intelligent Automation
Once all relevant data can be accessed and analyzed, a technician with PLC automation training can begin the task of developing the desired automation process. In a manufacturing setting, PLC technicians develop code (in addition to maintaining and troubleshooting the system) to automate the kind of high volume, repetitive tasks that perhaps more easily lend themselves to error when performed by a human operator.
Automation was not developed to substitute human reasoning and intuition, nor to replace it. Many tasks however can often be effectively completed using robotic process automation (RPA) if it was developed using the hard data collected and the application of programming logic. It’s one thing to successfully gather the data from the various silos, and another thing entirely to connect that data and program intelligent RPA. Though it does take considerable effort initially to gather and analyze the data and write the automation code, the increase in efficiency alone makes it a worthwhile endeavour.
Extensibility
For manufacturers who are just beginning to test the waters of this transformative technology, the best approach to take is the same one taken when exploring the viability of any new technology. Before making a financial commitment to integrate automation into the entire operation, it is advisable that one project be selected as a proof of concept. Likewise, an employee looking to gauge the viability of a new career in building or servicing robotics and AI technology must understand how ready managers are to adopt RPA, as well as its prevalence in the industry. The project should consist of a limited run completed in short order where the costs versus benefits analysis can be examined relatively quickly. It’s difficult to know what the return on investment will be if it isn’t tested in real world conditions.
Another benefit of starting with one project as a proof-of-concept is that it might answer many of the questions surrounding scaling up the integration of RPA, how to avoid pitfalls specific to your business or industry, and how the technology might be better leveraged to drive unprecedented growth for the manufacturer and opportunities for the employee.
Realistically, a two-pronged approach should be taken when integrating automation technology. The first prong of the approach should be modular, so that maintaining the system is easily achieved. The second prong consists of flexibility (namely, the RPA should be robust enough to apply more complex algorithms as the quantity of data increases exponentially).
As RPA systems become integral across industries, working towards the right training will prove invaluable in shaping your career. Check out George Brown College’s Robotics Technician training program to kickstart an exciting career or to increase opportunities for your existing one.
Comments (0)
This post does not have any comments. Be the first to leave a comment below.
Featured Product
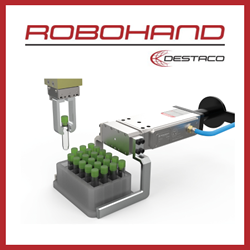