Enhancing Equipment Reliability with xPump: AI/ML-Based Monitoring & Predictive Maintenance for COBRA DS 0700, 1000, 2000 G Vacuum Pumps
Enhancing Equipment Reliability: Implementing xPump - AI/ML Based Pump Monitoring & Predictive Maintenance System on the Dry Screw Vacuum Pump with Integrated Vacuum Booster COBRA DS 0700, 1000, 2000 G
Introduction: Enhancing Equipment Reliability with AI and ML
In today's fast-paced industrial landscape, reliability and performance are crucial for businesses to maintain a competitive edge. One of the most essential components in many industries is the vacuum pump, specifically the dry screw vacuum pumps with integrated vacuum boosters. These pumps are responsible for maintaining optimal vacuum levels and ensuring smooth operation in various industrial processes, ranging from semiconductor manufacturing to pharmaceutical production.
However, ensuring the reliability of these pumps can be challenging due to the complexities involved in their operation. To address this, advanced technologies such as Artificial Intelligence (AI) and Machine Learning (ML) have emerged as key solutions for improving pump monitoring and predictive maintenance. By leveraging AI/ML-based systems, businesses can proactively manage pump health, reduce downtime, and enhance overall efficiency.
In this blog, we will explore how the implementation of the xPump system, powered by AI and ML, can significantly enhance the reliability of the Dry Screw Vacuum Pump with Integrated Vacuum Booster models COBRA DS 0700, 1000, and 2000 G.
Understanding the Dry Screw Vacuum Pump and Integrated Vacuum Booster
The Dry Screw Vacuum Pump is a type of positive displacement pump that uses two helical screws to create a vacuum in the system. These pumps are known for their robustness and reliability, especially in demanding environments. The integrated vacuum booster in the COBRA DS models helps to further increase the vacuum pressure and improve pump efficiency.
These pumps are widely used across industries such as semiconductor fabrication, food processing, chemical production, and more. Due to their critical role in maintaining consistent production processes, any failure or downtime can lead to significant operational disruptions, making reliability a top priority.
Challenges in Traditional Pump Maintenance
Traditionally, maintaining the reliability of vacuum pumps involved regular manual inspections, maintenance schedules, and reactive repair strategies. While these methods have been effective to an extent, they have limitations, including:
Unpredictable Failures: Traditional maintenance approaches are often reactive, meaning that they address issues only after they occur. This can lead to unexpected downtime and repair costs.
Over-maintenance or Under-maintenance: Fixed maintenance schedules may result in either over-maintenance, where parts are replaced unnecessarily, or under-maintenance, where components are not checked often enough, leading to premature failure.
Inconsistent Performance Monitoring: Without continuous monitoring, it is difficult to track the health of the pump in real-time. This increases the risk of unnoticed problems, which can affect the efficiency and reliability of the equipment.
Increased Operational Costs: Unforeseen repairs and maintenance activities can lead to higher operational costs and lower overall profitability.
The Role of xPump - AI/ML-Based Pump Monitoring and Predictive Maintenance
To overcome these challenges, implementing the xPump system can revolutionize the way dry screw vacuum pumps and integrated vacuum boosters are maintained. The xPump system utilizes AI and ML technologies to monitor pump health, predict failures, and optimize maintenance schedules. Here's how it works:
Continuous Data Monitoring: The xPump system continuously collects real-time data from various sensors embedded in the pump. These sensors monitor critical parameters such as temperature, vibration, pressure, and flow rates. This data is transmitted to a centralized platform for analysis.
AI and ML Algorithms: The heart of the xPump system lies in its AI and ML algorithms. By analyzing historical data and detecting patterns, the system can predict potential failures before they occur. This predictive maintenance approach allows operators to address issues proactively, preventing unexpected breakdowns and reducing downtime.
Condition-Based Monitoring: Unlike traditional time-based maintenance, the xPump system shifts to condition-based maintenance. This means that maintenance is performed only when needed, based on the real-time condition of the pump. This approach reduces unnecessary repairs and extends the lifespan of pump components.
Predictive Alerts and Notifications: When the system detects abnormal behavior or predicts a potential failure, it generates alerts and notifications. These alerts are sent to maintenance teams, allowing them to take corrective actions before a failure disrupts operations.
Optimized Performance: By continuously analyzing performance data, the xPump system helps to optimize the pump's efficiency, ensuring that it operates at its best. This results in improved energy efficiency, reduced wear and tear, and lower operational costs.
Benefits of Implementing xPump for the COBRA DS Series Pumps
The integration of the xPump system on the COBRA DS 0700, 1000, and 2000 G dry screw vacuum pumps with integrated vacuum boosters offers numerous benefits, including:
Increased Equipment Uptime: Predictive maintenance minimizes unexpected failures, ensuring that the pumps run smoothly and efficiently, which leads to increased uptime.
Cost Savings: By reducing downtime, preventing costly repairs, and optimizing maintenance schedules, businesses can significantly cut maintenance and operational costs.
Improved Efficiency: With real-time monitoring and data analysis, the pumps can be optimized for peak performance, leading to energy savings and better operational efficiency.
Prolonged Pump Lifespan: By addressing issues before they lead to failure, the xPump system helps to extend the lifespan of the pumps and their components, leading to a better return on investment.
Enhanced Data-Driven Decision Making: The continuous stream of data and insights provided by the xPump system enables businesses to make more informed, data-driven decisions regarding pump maintenance and operation.
Real-World Applications and Case Studies
Industries that rely heavily on dry screw vacuum pumps can benefit greatly from the implementation of xPump. In semiconductor manufacturing, for instance, a failure in the vacuum system can cause significant production delays, leading to costly downtime. By using the xPump system, semiconductor plants can predict and prevent such failures, ensuring smooth, uninterrupted operations.
Similarly, in the pharmaceutical industry, where precise vacuum levels are crucial for the production of medicines and vaccines, the reliability of vacuum pumps is of utmost importance. With the implementation of xPump, pharmaceutical companies can ensure that their pumps are always operating at peak efficiency, reducing the risk of production halts and improving overall product quality.
Call to Action: Get Started with xPump Today
The future of pump maintenance is here, and it's powered by AI and ML. By implementing the xPump system on your Dry Screw Vacuum Pump with Integrated Vacuum Booster COBRA DS 0700, 1000, or 2000 G, you can transform your maintenance approach, enhance equipment reliability, and reduce operational costs.
Don't wait for the next breakdown to disrupt your operations. Take control of your pump maintenance with predictive analytics and ensure that your equipment operates at peak performance.
Contact us today to learn more about how xPump can revolutionize your pump maintenance strategy and improve your equipment reliability.
Featured Product
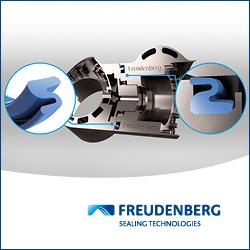
IP Seals for Robots
Freudenberg Sealing Technologies' IPRS (Ingress Protection Seals for Robots) provides reliable protection for robotic systems operating in harsh environments. Designed to prevent dust, moisture, chemicals, and wear from compromising performance, IPRS extends service life and reduces maintenance. The adaptive Z-shaped geometry ensures sealing integrity under continuous motion, making it ideal for high-speed automation and outdoor applications. Manufactured with high-performance elastomers such as Fluoroprene XP and EPDM, IPRS offers exceptional resistance to lubricants, cleaning agents, and extreme temperatures. This makes it the perfect solution for six-axis robots, SCARA robots, AMRs, AGVs, and cobots.
With its low-friction design and durable materials, IPRS enhances energy efficiency and operational reliability in industrial and autonomous robotics. Learn more about our IPRS Seals