Mobile robotics software: Advancements and applications
Advances in mobile robotics software are revolutionizing the industry, driving innovations in automation and efficiency. At the heart of these advancements is the Robot Operating System (ROS), an open-source framework that has become the standard for mobile robotics development. In this article, Román Navarro, head of Robotnik's Software Department for 16 years, delves into the critical role of ROS software for mobile robots and explores future trends in this rapidly evolving field.
🟥OVERVIEW OF MOBILE ROBOTICS SOFTWARE🟥
Within the field of robot programming software, significant technological advancements are also observed in adjacent technologies such as artificial intelligence and machine vision. This evolution enables mobile robots to serve as the foundation for automation in a growing number of applications, including mobile handling, load transportation, inspection, cleaning, surveillance, and agricultural tasks that require mobility.
Another example of the importance of software development in robotics is the growing demand for fleet management systems that coordinate and unify the control of robot fleets. For a fully automated process in the industries mentioned above, the involvement of multiple robots is sometimes necessary. In these cases, fleet management software simplifies and optimizes the management of the various devices.
In addition to being a hardware manufacturer, Robotnik is a robotics engineering company that develops open source software for indoor and outdoor mobile robotics, based on ROS. The in-house development of mobile robots software makes it possible to facilitate the integration of all robots in any industrial sector and for a wide range of applications.
🟥FREQUENTLY ASKED QUESTIONS ABOUT ROBOTICS SOFTWARE🟥
Román Navarro, Software Manager at Robotnik, tells in this interview more about ROS, as well as the keys to the evolution, present and future of software focused on mobile robotics.
1️⃣ What are the main functions and responsibilities of a software department at a mobile robotics company?
R: Robotnik's software department is involved in many processes in the development and manufacturing of our products. I highlight some of the tasks of our team:
- Development of new functionalities for our equipment. When failures are detected or improvements are identified, we start working on them to incorporate the changes as soon as possible.
- Integration of new hardware and software components. We collaborate with many other hardware and software suppliers that require software integration with our systems.
- Package updating. Our systems require periodic updating of application libraries as well as the operating system. Some of these updates are related to new functionalities and others to cybersecurity.
- Participation in internal development projects. Most of our internal development projects require a lot of work from our developers.
- Implementation of projects. Some of our projects require a start-up and training which we also take care of.
- Equipment testing / Quality control. Participation in the testing and quality control of our systems.
- Support tasks. We actively participate in the resolution of any problem related to our equipment.
- Technical support for commercial tasks. We solve any doubt that customers may have related to the functionality of our robots.
2️⃣ Major milestones and advances in robotics development.
R: During these 16 years, we have experienced an amazing evolution both in the field of mobile robotics and in adjacent technologies: Artificial Intelligence, machine vision, virtual reality, machine learning, etc.
From my point of view, the biggest advance in robotics during these years has been the creation and implementation of ROS as the reference framework in service and research robotics, and with an increasing presence in industrial robotics. ROS has allowed most robotics developments and applications to share a common way of working and allows the reuse of much of the code generated by the community. Before ROS, each group/company developed its own robot software from scratch.
Since 2002, our hardware and software have evolved significantly, adapting to all the challenges we have encountered along the way. We've seen how autonomous mobile robotics has greatly advanced in this sense, reaching a point of real and safe interaction with humans.
So we now have mobile robots playing very diverse roles in a wide range of industries, from traditional logistics to agriculture, mobile handling to surveillance. Our robots now work in shared spaces with people without the need for safety perimeters thanks to innovation in navigation, localization, obstacle detection and other advanced sensing.
Technology has progressed enormously, allowing for greater autonomy, environmental awareness and collaboration with humans.
3️⃣ More and more companies are manufacturing mobile robots, what makes the difference between one product and another, from the SW point of view?
R: The differentiation between products at a software level comes down to several aspects. First, the ability to adapt and customize the software to meet the specific needs of the customer and the environment in which the robot will operate is fundamental. Each customer's tasks or applications have specific and particular characteristics. No two tasks or environments are exactly the same. In Robotnik we manufacture with a certain modularity, so that the robot adapts as much as possible to the needs of each company.
The robustness and reliability of the software are also critical aspects, especially in applications where safety and precision are a priority. The ability to integrate with other systems and the ease of programming and operation are equally important to ensure a smooth implementation. In addition, the ability to upgrade and enhance the software over time to keep up with changing market demands and new technologies is essential to ensure the longevity and continued value of the product.
Another point of differentiation is the framework and architecture employed in the robot. Using ROS-based systems allows many integrators and developers to better understand how our applications work and even develop their own solutions based on ours.
4️⃣What do you think will be the most important application in the next 20 years?
R: Mobile robotics is at the people's service. Therefore, we may think that the main applications in robotics will respond to the main needs of people.
I think that in the coming years we will see major advances in mobile manipulation applications, either with humanoids or with AMR + manipulator. The implementation and development of generative AI, as well as the cheapening of hardware will make it possible for us to see many applications in this area, both in industry and in service applications.
🟥THE ROLE OF AI IN ENHANCING ROBOTICS SOFTWARE🟥
To conclude, among the current trends in robotics software it is necessary to highlight Artificial Intelligence and the technological revolution that it implies.
Artificial intelligence (AI) and Machine Learning are transforming mobile robotics software. These technologies allow robots to learn from their experiences and expand their interaction capabilities based on experience:
- Image recognition: The use of convolutional neural networks (CNN) makes robots recognize objects and people in their environment.
- Reinforcement learning: This method allows robots to learn optimal behaviors through a trial-and-error process.
- Natural Language Processing (NLP): Facilitates interaction between humans and robots through spoken or written language.
Mobile robotics software is a dynamic and constantly evolving area. From operating systems like ROS to navigation algorithms and artificial intelligence, each component is crucial to the development of efficient and safe autonomous robots.
Featured Product
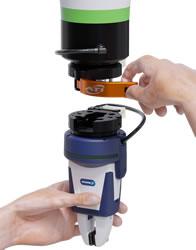
ATI Industrial Automation - MC-50 Manual Tool Changer
With intuitive and ergonomic lever operation, the patent-pending MC-50 Manual Robot Tool Changer provides a simple solution for quickly changing robotic end-of-arm tooling by hand. This compact and robust Tool Changer is designed for applications on collaborative robots that support payloads up to 25 kg and small industrial robots supporting payloads up to 10 kg. Featuring an ISO 50 mm mounting interface on the Master-side and Tool-side, the low-profile MC-50 mounts directly to most cobots and seamlessly integrates with many common cobot marketplace grippers and end-effectors.