DEEP Robotics introduces high-torque joint modules to drive legged robotics development
DEEP Robotics expects the debut of new joint modules to have deep implications for the booming robot industry in China and beyond.
DEEP Robotics, a leading quadrupedal robot developer from Hangzhou, China, has launched a trio of new robotic joint modules, the J80-27P, J100-64P and J100-116P. All feature some of the highest torques within their cateogry.
Specifically, the J100-116P boasts a peak torque of 315 Nm and has been used in large humanoid robotics, paving the way for more mobile, dynamical and dexterous models.
The smallest of the trio, the J80-27P, maxes out at 84 Nm in torque and is widely utilized in smaller-sized legged robots.
For its part, the J100-64P is designed for medium-to-large-legged robots, providing a rated torque of 65 Nm and a peak torque of 180 Nm.
Notably, the torque coefficient of the J100-64P is the highest among the three joint modules, at 5 Nm per Arms, compared to 4.4 Nm per Arms for J80-27P and 3.9 Nm per Arms for J100-116P.
A higher torque coefficient translates into a greater torque output, giving the robot a higher payload needed to perform heavier tasks.
These joints have already been adopted by DEEP Robotics across its product portfolio. For instance, the X30, a flagship, industry-grade quadruped robot, is equipped with these new parts.
To date, they are deployed to more than 10 countries worldwide, with applications in power stations, factories, pipeline inspection, emergency rescue, fire detection, scientific research and so on.
Their performance has been validated in large-scale applications such as automated inspection and fire hazard detection under harsh operating conditions.
Built to the highest industrial standards, these IP67-rated joints are tolerant of rain and dust and can operate in all-weather outdoor environments.
These joints also feature high-precision control, as they utilize a highly reliable, battery-free multi-turn absolute encoder. This design offers high precision, reliability, and durability, with excellent control performance in overall joint tuning.
Additionally, DEEP Robotics also employs a high-speed EtherCAT communication protocol for these products.
This suggests that these joints can support the coordinated control of up to 30 joints on a single robot. Nowadays, most humanoid robots have more than 30 degrees of freedom or joints.
Both the J100 and J80 joint series are designed with a drive-control separation scheme, whereby they possess multiple benefits, such as facilitating multi-joint integration and heat dissipation.
They are also compatible with various mainstream drives available on the market, enabling customers to choose and integrate drives according to their needs.
DEEP Robotics expects the debut of the new joint modules to have deep implications for the booming robot industry in China and beyond.
The goal is to empower industry partners to advance the evolution of legged robotics and realize embodied intelligence together.
Featured Product
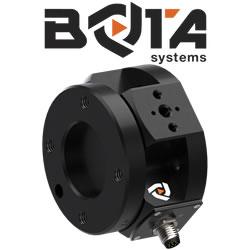
Bota Systems - The SensONE 6-axis force torque sensor for robots
Our Bota Systems force torque sensors, like the SensONE, are designed for collaborative and industrial robots. It enables human machine interaction, provides force, vision and inertia data and offers "plug and work" foll all platforms. The compact design is dustproof and water-resistant. The ISO 9409-1-50-4-M6 mounting flange makes integrating the SensONE sensor with robots extremely easy.
No adapter is needed, only fasteners! The SensONE sensor is a one of its kind product and the best solution for force feedback applications and collaborative robots at its price. The SensONE is available in two communication options and includes software integration with TwinCAT, ROS, LabVIEW and MATLAB®.