Introducing the New Delta Line Multi-Axis BLDC Motor Controller Family: The Phoenix Drive
Delta Line has introduced the Phoenix Drive product family, a new multi-axis brushless DC motor controller inside of a slim, space-saving package. Ideal for applications with strict size requirements, the advanced EtherCAT Phoenix Drive controls up to 3 motors within a compact and functional solution
The Delta Line Phoenix Drive product family is the next generation of highly integrated motor control solutions. By processing all real-time critical functions within the drive, the Phoenix Drive minimizes communication traffic, reduces controller dimensions and decreases the overall system cost. It also provides axis synchronization, making the Phoenix Drive a cost-effective integrated motion controller.
The Phoenix Drive uses EtherCAT high speed communication protocol and is available in two configurations: B100 and B500. Both configurations include system protections such as over current, over and under voltage, overheating, phase-to-phase shorts and ground shorts. These drives control BLDC motors with both 5V encoders and hall effect sensors. The B500 Controller includes brake output of 1.3A and STO (Safe Torque Off).
Delta Line is a trusted partner for demanding, high-growth industries such Automatic Guided Vehicles (AGVs), Autonomous Mobile Robots (AMRs), electric vehicles, electric wheelchairs, logistics solutions and more. With the release of this highly integrated, compact multi-axis Phoenix BLDC Motor Controller family, Delta Line continues to be a leader in mobile motion control applications.
Specifications at a glance:
• Motor Axis: 3
• Power Supply: 12-48 VDC
• Phase Current: up to 12A RMS
• Peak Current: 36A
• Dimensions:
o Phoenix B500 Drive 200 x 90 x 30 mm
o Phoenix B100 Drive 180 x 40 x 20 mm
• Feedback Options: Encoder (5V differential or 5V single-Ended incremental) and/or Hall Effect Sensor
• Brake (1.3A Output) and STO (Safe Torque Off) available for Phoenix B500 Drive
• Communication interface: EtherCAT
• Chopper frequency: 40kHz
• CE, REACH, ROHS 3 Certified
Featured Product
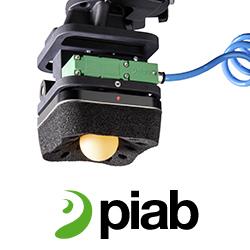