Kaman Highlights the DIT-5200L Noncontact Differential Impedance Transducer
High sensitivity, extreme linearity, and exceptional thermal stability at a competitive price
Middletown, CT - The Measuring Division of Kaman Precision Products, Inc., the world leader in the design and manufacture of high-performance position measurement systems, highlights the DIT-5200L noncontact differential impedance transducer, which offers true differential for common mode rejection at an economical price. Capable of subnanometer resolution with high sensitivity (up to 10v/mil, 39 mV/μm) and outstanding linearity (up to 0.1% full range), this product provides a powerful solution for a diverse set of applications that demand exacting precision.
The DIT-5200L is a commercially-based, fully analog product built to IPC A-160 Class 3 standards. Depending on the program requirements, it also offers the opportunity for commercial-off-the-shelf up screening. The I/O is on a 9-pin mini-D connector, and the input power connections are reverse voltage protected.
The product's signal conditioning electronics are packaged in a die cast aluminum box with MCX style sensor connections, and the overall package size is just 7.7 cubic inches. The product is CE marked when purchased in the original enclosure. The electronics can also be supplied as a bare PCB for installation inside the user's enclosure, and custom configurations can be designed for OEM application requirements upon request.
Under the hood, the product features high precision eddy current balanced bridge technology. In an eddy current differential system, the two coils in the inductive bridge are housed in two separate sensors. Rather than one active coil and one reference coil, both sensors contain active coils. These two sensors are typically placed on opposite sides of either the target or the target pivot point.
Due to the theory of operation, differential systems provide greater resolution and thermal stability than single-ended systems. As the target moves closer to one sensor, it moves farther away from the other, and this increases the impedance in one leg of the inductive bridge and decreases it in the other. This push-pull effect amplifies the linear output-per-displacement and eliminates the need for summation amplifiers that add noise and drift. Ultimately, this provides exceptional thermal stability, namely, ±.03% FS/°C and ±.005% FS/°C at null.
Available in both single and dual channel configurations, the product fits a range of applications across industry verticals. These include servo control feedback, stage positioning, angular displacement indication, X-Y orbit position feedback, and stylus position. The product's applications play an important role in technologies such as precision optics, fast-steering mirrors, laser communications, directed energy, celestial applications, and magnetic bearing systems.
Featured Product
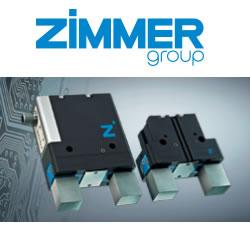