ABB wins $52 million robots order to boost manufacturing flexibility at Ford's newest China factory
ABB robots to be installed at Changan Fords new Harbin-based auto factory as part of its Body-in-White (BIW) welding process ABB robots have been used successfully across Changan Ford's major automobile production facilities in China since 2007
Zurich, Switzerland, July 2, 2015 - ABB, the world's leading power and automation technology group, has won an order worth $52 million to boost the flexibility and efficiency of Changan Ford Automobile Co., Ltd.s new production facility in Harbin, China. The robots will be used to make Fords new Focus model.
ABB will provide robots including the IRB 6700 and IRB 7600 for Changan Fords new highly-automated "Body in White" welding production line. Included in the order is ABBs GateFramer car body framing positioning system, capable of producing up to six vehicle models on the same line, with just 18 seconds needed to switch to a different model.
ABB robots at the new Changan Ford plant will bolster the carmakers flexible manufacturing allowing it to respond swiftly to changing consumer sentiment and demand while simultaneously reducing investment costs compared to traditional production lines. ABB has worked with Changan Ford since 2007, with ABB robots producing the joint ventures Ford Mondeos at manufacturing plants in Chongqing.
"Changan Ford and ABB have a longstanding relationship, and we are pleased to see ABBs solid reputation for providing outstanding and reliable technology and excellent project management capabilities gain customer recognition once again," said Pekka Tiitinen, president of ABBs Discrete Automation and Motion division. "Improving industrial productivity is one of the major drivers of ABBs business growth under the ‘Next Level strategy. ABBs flexible, intelligent manufacturing technologies help customers effectively reduce their investment costs and enhance their productivity and respond to the market needs in a timely fashion."
The IRB 6700 robot family, a new generation of large industrial robots, was introduced to the market in 2013. More robust and 15% more energy efficient than its predecessor, its maintenance has been simplified, making it the highest performing robot for the lowest total cost of ownership in the 150-300 kg class.
ABB also will provide Changan Ford with comprehensive and advanced Body-in-White solutions, including a flexible car body conveying system and laser welding system, as well as the robotic Roller Hemming system which is used for the production of the vehicles four doors and roof.
ABBs industrial robot technologies cover the entire automobile production process, including stamping, Body in White, painting, and powertrains. Automobile customers include international automakers such as BMW, Honda, Volvo and Great Wall Automobile.
ABB Robotics is a leading supplier of industrial robots - also providing robot software, peripheral equipment, modular manufacturing cells and service for tasks such as welding, handling, assembly, painting and finishing, picking, packing, palletizing and machine tending. Key markets include automotive, plastics, metal fabrication, foundry, e lectronics, machine tools, pharmaceutical and food and beverage industries. A strong solutions focus helps manufacturers improve productivity, product quality and worker safety. ABB has installed more than 250,000 robots worldwide.
About ABB
ABB (www.abb.com) is a leader in power and automation technologies that enable utility, industry, and transport and infrastructure customers to improve their performance while lowering environmental impact. The ABB Group of companies operates in roughly 100 countries and employs about 140,000 people.
For help with any technical terms in this release, please go to: www.abb.com/glossary
Featured Product
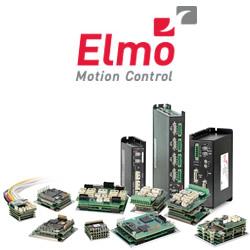
Elmo Motion Control - The Platinum Line, a new era in servo control
Significantly enhanced servo performance, higher EtherCAT networking precision, richer servo operation capabilities, more feedback options, and certified smart Functional Safety. Elmo's industry-leading Platinum line of servo drives provides faster and more enhanced servo performance with wider bandwidth, higher resolutions, and advanced control for better results. Platinum drives offer precise EtherCAT networking, faster cycling, high synchronization, negligible jitters, and near-zero latency. They are fully synchronized to the servo loops and feature-rich feedback support, up to three feedbacks simultaneously (with two absolute encoders working simultaneously). The Platinum Line includes one of the world's smallest Functional Safety, and FSoE-certified servo drives with unique SIL capabilities.