Hummingbird Wings More Efficient Than Micro-Helicopter Blades
A quantitative analysis of hummingbird wings shows that they generate lift more efficiently than the best micro-helicopter blades. The findings could lead to more powerful, bird-inspired robotic vehicles.
More than 42 million years of natural selection have turned hummingbirds into some of the world's most energetically efficient flyers, particularly when it comes to hovering in place.
Humans, however, are gaining ground quickly. A new study led by David Lentink, an assistant professor of mechanical engineering at Stanford, reveals that the spinning blades of micro-helicopters are about as efficient at hovering as the average hummingbird.
The experiment involved spinning hummingbird wings - sourced from a pre-existing museum collection - of 12 different species on an apparatus designed to test the aerodynamics of helicopter blades. The researchers used cameras to visualize airflow around the wings, and sensitive load cells to measure the drag and the lift force they exerted, at different speeds and angles.
Lentink and his colleagues then replicated the experiment using the blades from a ProxDynamics Black Hornet autonomous microhelicopter. The Black Hornet is the most sophisticated microcopter available - the United Kingdom's army uses it in Afghanistan - and is itself about the size of a hummingbird.
Even spinning like a helicopter, rather than flapping, the hummingbird wings excelled: If hummingbirds were able to spin their wings to hover, it would cost them roughly half as much energy as flapping. The microcopter's wings kept pace with the middle-of-the-pack hummingbird wings, but the topflight wings - those of Anna's hummingbird, a species common throughout the West Coast - were still about 27 percent more efficient than engineered blades.
Hummingbirds acing the test didn't particularly surprise Lentink - previous studies had indicated hummingbirds were incredibly efficient - but he was impressed with the helicopter.
"The technology is at the level of an average Joe hummingbird," Lentink said. "A helicopter is really the most efficient hovering device that we can build. The best hummingbirds are still better, but I think it's amazing that we're getting closer. It's not easy to match their performance, but if we build better wings with better shapes, we might approximate hummingbirds."
Based on the measurements of Anna's hummingbirds, Lentink said there is potential to improve microcopter rotor power by up to 27 percent.
The study is published in the current issue of Journal of the Royal Society: Interface.
The high-fidelity experiment also provided an opportunity to refine previous rough estimates of muscle power. Lentink's team learned that hummingbirds' muscles produce a surprising 130 watts of energy per kilogram; the average for other birds, and across most vertebrates, is roughly 100 watts/kg.
Although the current study revealed several details of how a hummingbird hovers in one place, the birds still hold many secrets. For instance, Lentink said, we don't know how hummingbirds maintain their flight in a strong gust, how they navigate through branches and other clutter, or how they change direction so quickly during aerial "dogfights."
He also thinks great strides could be made by studying wing aspect ratios, the ratio of wing length to wing width. The aspect ratios of all the hummingbirds' wings remarkably converged around 3.9. The aspect ratios of most wings used in aviation measure much higher; the Black Hornet's aspect ratio was 4.7.
"I want to understand if aspect ratio is special, and whether the amount of variation has an effect on performance," Lentink said. Understanding and replicating these abilities and characteristics could be a boon for robotics and will be the focus of future experiments.
"Those are the things we don't know right now, and they could be incredibly useful. But I don't mind it, actually," Lentink said. "I think it's nice that there are still a few things about hummingbirds that we don't know."
Featured Product
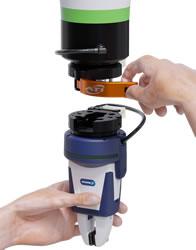
ATI Industrial Automation - MC-50 Manual Tool Changer
With intuitive and ergonomic lever operation, the patent-pending MC-50 Manual Robot Tool Changer provides a simple solution for quickly changing robotic end-of-arm tooling by hand. This compact and robust Tool Changer is designed for applications on collaborative robots that support payloads up to 25 kg and small industrial robots supporting payloads up to 10 kg. Featuring an ISO 50 mm mounting interface on the Master-side and Tool-side, the low-profile MC-50 mounts directly to most cobots and seamlessly integrates with many common cobot marketplace grippers and end-effectors.