NOVEL SERVO DRIVES BOOST MACHINE PERFORMANCE
New designs provide up to 25 % faster acceleration
Braunschweig, Germany, June 7, 2012 --- Today, Metronix launches a range of
slash system building costs in dozens of common industrial automation
applications. The new drives offer a peak current capability that is up to
twice that of many similar drives on the market, allowing machine builders
to dramatically boost acceleration times.
An increased overcurrent capability of four times the continuous output
rating is being offered as standard on Metronix' ARS 2000 FS range of
Ethernet-compatible servo drives. This compares with the ~2 to 2.5 times
overcurrent rating offered by many other servo drive manufacturers.
The capability can be exploited in many common motion control applications
to increase the speed of moves and the overall throughput of machines. In
tests that compared drives offering a two times overcurrent capability
against the new ARS 2000 FS, using a range of loads on rotary and linear
servo motor axes, the new drives shortened travel times by factors from
around 17 to 25 %. The drives will sustain the overcurrent for half a
second, providing considerable flexibility for the system builder.
Depending on the application and the motion profiles used, faster
acceleration can have a significant impact on machine cycle times.
Point-to-point moves are the most frequently used type of motion on many
machines for example. Here, Metronix' ARS 2000 FS can dramatically shorten
the times required to accelerate up to full speed when using common motion
profiles such as trapezoids or S-curves.
This kind of movement features extensively in many automation applications
such as pick and place, parts handling and assembly, labelling and
packaging, and sampling and testing. In continuous applications such as
these, Metronix' tests demonstrated overall increases in automation
productivity of around 5 to 7% by switching to the new drives.
The faster acceleration results from an uprated IGBT power stage, which
utilizes power factor correction to boost the internal DC bus voltage level
and allow the motor to reach higher top speeds. This adds only a fractional
cost to the drive.
Metronix developed the capability to provide a closer match between drive
and servo motor capabilities. Many servo motors offer an overcurrent
capability that is higher than the typical drive's overcurrent ratio of
around two. Ratios from three to four are common, and they can be even
higher. By using Metronix drives, machine builders are able to exploit the
full continuous and peak torque capabilities of the servo motor. In some
applications, it's also anticipated that users will also be able to select a
smaller servo drive, cutting a substantial amount from the bill-of-materials
- as the drives are usually the most expensive part of the motion control
system.
"This capability provides automation builders with a means of reducing
machine cycle times for faster payback, and potentially reducing
bill-of-materials costs as well," says Metronix' Product Manager, Frank
Essmann. "Some simple calculations at the start of a machine design project
are all that's needed to evaluate the potential improvements that can be
gained."
ARS 2000 FS is a family of compact panel/cabinet-mounting drives available
with a choice of six single- or three-phase continuous output power ratings
from 0.5 to 6 kVA, in two case sizes with widths of 59 or 69 mm (2.32 or
2.72 inches). The drives all feature a universal encoder interfacing
capability that allows connection to resolvers, analog/digital incremental
encoders, and single/multiturn absolute encoders such as Hiperface or EnDat.
Standard communications interfaces include Ethernet, USB and the CAN
fieldbus - compatible with the DS 402 CANopen device profile. The drives
also come with a built-in EMC filter, integrated brake chopper and brake
resistor. Two expansion bus slots accepting plug-in modules provide a very
powerful means of extending a drive's capability for specific applications.
Among the options available are a motion control module that can control up
to four interpolated axes, digital I/O, additional networking interfaces
including EtherCAT or Profibus-DP, and a functional safety module compliant
with EN 61800-5-2.
The motion control plug-in adds another powerful mechanism to the
cost-saving potential of Metronix' new drives, providing the means to
convert an ARS 2000 FS into a very economic intelligent drive. As the module
can also control up to four interpolated axes, it can greatly reduce the
costs of many common assembly, manufacturing and processing motion control
applications such as product synchronization or spacing, registration,
labelling, cutting, pick-and-place, and wrapping. Complex applications
involving three axes of control, plus a feed or handling axis, can even be
accommodated using the economic plug-in module. A powerful Windows-based
programming and configuration software tool is available to users to create
embedded motion and machine control software for Metronix systems.
Metronix has been producing motion control technology for industrial
machines and automotive applications for over 30 years. Its product range
includes smart servo drives with integrated positioning capability, plus
motion controllers and accessories that provide cost-effective solutions for
multi-axis motion control and automation, and decentralized machine control
requirements. A key feature of Metronix' motion products is their rich
networking and encoder interfacing capability, which ensures that drives can
be integrated easily into virtually any industrial system or machine - even
if an OEM has custom PLC or control hardware. This feature is highly valued
by many OEMs as it allows them to create and continue developing innovative
brands of machine offering unique features. Metronix complements this
capability with what is probably the most sophisticated and capable custom
drive engineering service on the market today. Motion control products
designed by Metronix are marketed under its own brand, and in custom forms
by a number of well known industrial OEMs.
The company additionally makes geophysical instruments and customer-specific
digital controls for measurement and control applications. Metronix is part
of the Apex Tool Group, headquartered in Sparks, Maryland, USA. The Apex
Tool Group has more than 7,600 employees in over 30 countries. Metronix'
design and manufacturing facility is located in Braunschweig, Germany.
For more information please contact:
Metronix Meßgeräte und Elektronik GmbH, Kocherstrasse 3, D-38120
Braunschweig, Germany. t.: +49 (0)531 8668-0; sales@metronix.de;
www.metronix.de
Featured Product
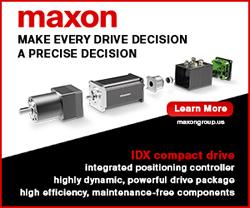
The maxon IDX Compact Drive with Integrated Positioning Controller
The compact brushless EC-i motor combined with an EPOS4 positioning controller delivers a highly dynamic, powerful drive package with field-oriented control (FOC), high efficiency, and maintenance-free components in a high-quality industrial housing. The maxon IDX drives are suitable for use across the entire speed range (from standstill to maximum speed) and have an extremely high overload capability. Together with a positioning controller, the integrated sensor (single turn) enables absolute positioning.