Adept and Bremer Werk fur Montagesysteme GmbH Deliver Future-Proof Assembly Concept for High-End Razors
When Philips, a world leader in healthcare, lifestyle and lighting products, decided to build an assembly line capable of manufacturing their current line of high-tech shavers and support any future redesigns, they turned to Adept Technology (Nasdaq:ADEP) as their supplier of robotics and flexible feeding systems.
When Philips, a world leader in healthcare, lifestyle and lighting products, decided to build an assembly line capable of manufacturing their current line of high-tech shavers and support any future redesigns, they turned to Adept Technology (Nasdaq:ADEP) as their supplier of robotics and flexible feeding systems. The combined expertise of Bremer Werk fur Montagesysteme GmbH and Adept led to a successful deployment of an assembly system capable of producing Philips\' high-tech shavers, which are in high-demand and considered premium products all over the globe.
\"True flexible feeding means being able to solve tomorrowÂ's challenges today,\" says Ruediger Winter, Director of European Sales, Adept Technology. \"Changing products no longer requires any hardware changes, but just a few minutes to teach the system to accept the new parts. This makes our customer feel safer about the longer-term competitive nature of their assembly line.\"
The high-tech shavers are produced at Philips\'s facility in Drachten, Netherlands, which is where the company\'s research and development activity resides. The assembly of the high-tech shaving devices demanded the highest level of quality, which is why the Drachten plant turned to automation instead of manual labor for their production. Reliable assembly processes with integrated quality control assure the highest level of quality of the consumer products. For Bremer Werk fur Montagesysteme GmbH, it is no secret how to build the necessary equipment for demanding assembly tasks. The specialists had the industry expertise and knowledge, but in the case of Philips, there was much more required than pre-existing, proven solutions off-the-rack.
Future-Proof Assembly Concept for High-End Shavers
\"The real challenge in finding the right solution for Philips was to accomplish the enormous model variety of the high-end shavers. Currently about 60 different product lines culminate in some 600 single products. Thereby the product spectrum changes almost every day,\" said Matthias Schaller, head of robotics at the Bremer Werk fur Montagesysteme GmbH.
Beyond that obstacle, Philips outlined a requirement for an assembly solution that demanded much more than just the foresight of the construction engineers. In essence, Philips was insisting on a guaranteed level of performance of their equipment - in the future.
Sietze Bremer, Senior Sourcing Specialists Industrial at Philips said, \"We wanted to implement a future-oriented assembly concept. And with regard to the total investment, we wanted to feel certain that the equipment would still be able to economically produce shavers in ten years without knowing how the shaver of the future will look at all.\"
Building machinery capable of assembling products that don\'t exist yet presented a significant challenge. BWM chose Adept flexible robotic solutions after realizing that they would need 6-axis robots, SCARA robots, vision systems, part feeders and controls - all from a single source. Adept\'s high-duty components met all requirements and had already shown their efficiency in similar projects in the past for BWM.
Consistently Flexible
The first item to address was how to achieve the highest levels of flexibility. Maximum flexibility in the automation was delivered in a number of ways. The modular layout of the shavers consists of three main components that can be manufactured independent of one another on different production lines. Additionally, the conception of the complete equipment is also based on the module idea.
In Drachten, the three-head-shavers are currently assembled on a total of nine slitting lines each composed of five to eight cells. Each cell operates autonomously and can be connected or disconnected according to the plug-and-play principle. At present the complete equipment is extended by four new lines. The concept of smaller and mutually independent lines with autonomous cells delivers maximum flexibility and availability.
More than 120 Robots and 40 AnyFeeders
When the line integration is complete, more than 120 robots and 40 Adept Anyfeeder™ systems will provide the frictionless assembly system for the shavers. According to experienced Senior Manager Sietze Bremer, \"We count on Adept completely when expanding the equipment. The majority of Viper 6-axis and Cobra SCARA robots are equipped with AdeptSight vision guidance and inspection capabilities. The systems arrive already having been tried and tested in existing lines. The robots impress with their precision, speed, and availability and perform the tasks with the high accuracy that is required.\"
The AnyFeeder plays a key role within the cells,\" explains Bremer. \"Without its approved flexibility, the system concept would not have been feasible.\" The inherent flexibility of the AnyFeeder systems affected a number of areas throughout the assembly automation process, especially where efficient assembly with a high-degree of individualization mattered.
At the Philips plants, Bremer Werk fur Montagesysteme counted on the Adept AnyFeeder™ SX 240 flexible feeding system. And when integrated with Adept Cobra™ and Adept Viper™ robots and AdeptSight™ vision guidance, the AnyFeeder system redefines what it means to be flexible in small-parts feeding applications.
\"Flexible feeding systems are key components for the intelligent assembly automation, especially relating to the sustainability of the Philips equipment,\" said Schaller. \"Regardless of how the individual parts of the shavers will look in the future, the highly-flexible AnyFeeder will feed them as bulk goods. After \'seeing\' the parts, the robots will pick them up and proceed to assemble the devices. And in ten years, this simple and basic principle will not change.\"
Vision Guidance is Mandatory Going Forward
Vision guidance has been added to approximately 50 robots on the four new assembly lines currently being built. A majority of the robots on the existing lines were already equipped with vision guidance and all new machines are scheduled to have a vision system. This again reinforces the focus on flexibility: \"A robot with integrated vision guidance can be perfectly adopted for varying tasks and, furthermore, can take over additional work contents, for instance in the field of quality control,\" said Bremer.
The groundbreaking automation solutions guarantee an economic and efficient assembly of high-end shavers. In connection with the innovative components from a single source, the sophisticated assembly concept assures an unrivalled level of sustainability and the Philips plant is now one of the most innovative production sites for high quality shavers.
About Adept Technology, Inc.
Adept is a global, leading provider of intelligent robots and autonomous mobile solutions and services that enable customers to achieve precision, speed, quality and productivity in their assembly, handling, packaging, testing, and logistical processes. With a comprehensive portfolio of high-performance motion controllers, application development software, vision-guidance technology and high-reliability robot mechanisms with autonomous capabilities, Adept provides specialized, cost-effective robotics systems and services to high-growth markets including Packaging, Medical, Disk Drive/Electronics, and Solar; as well as to traditional industrial markets including machine tool automation and automotive components. More information is available at http://www.adept.com.
Featured Product
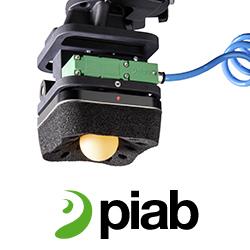