Rockwell Automation automates Meurer Research pilot plant
One way manufacturers stay ahead of the competition is by continuously equipping themselves with the latest automation and control technology. That has proven to be a successful strategy for Meurer Research Inc. (MRI) for more than 30 years.
One way manufacturers stay ahead of the competition is by continuously equipping themselves with the latest automation and control technology. That has proven to be a successful strategy for Meurer Research Inc. (MRI) for more than 30 years.
Since 1978, MRI has researched, developed and manufactured water and wastewater treatment systems used by municipalities around the world. Operating out of its 30,000 square-foot facility in Golden, Colo., MRI holds more than 50 patents for its advanced treatment systems and has implemented its equipment in over 2,000 projects worldwide.
Among MRI's most successful products are plate settlers, which are used in water and wastewater treatment plants as a method of pretreatment before the water enters the membrane filtration system. By separating and removing heavy solids that can clog filters, the plate settlers help extend membrane life, minimize cleaning requirements and reduce operating costs.
This advanced treatment technology has proven to deliver exceptionally high efficiency and better effluent quality. It also helps minimize the potential impact on the environment, while reducing the costs for treatment plant owners to dispose of processed wastewater. While plate settlers have been around for many years, recent technology advances have dramatically increased their cost effectiveness, and as a result, their popularity.
MRI's plate settlers offer distinct advantages over competitive systems, including an even flow distribution for improved efficiency.
Challenge
To better help potential customers evaluate the performance capabilities of its plate settlers, MRI maintains a fleet of 10 demonstration units. Installed on-site at treatment plants across the country for months at a time, these pilot systems allow municipalities to test the clarification and sludge removal capabilities of the equipment under actual operating conditions before committing to a full-scale implementation.
Once installed, these pilot units operate unmanned with minimal oversight during the majority of the test period. Any mechanical or control system problem can cause the system to report faulty data. Depending on the nature of the problem, this could require a service trip by MRI staff to resolve the issue with the customer. This can result in higher support costs and reflect negatively in the customer's overall evaluation of the system.
To help ensure these systems deliver maximum reliability, MRI sought to redesign and upgrade the control equipment on one of its 10 pilot units. The control system previously employed on the pilot unit included a mix of control products from multiple vendors, which hindered interoperability and limited connectivity between all of the automation equipment on a given machine.
MRI sought to ease the integration of components by working with a single-source supplier that could provide a control system easily integrated as a unified and more reliable system. In addition to improving reliability, performance and ease of use, MRI also wanted to equip the system with remote-monitoring capabilities. This would allow MRI to evaluate system performance and troubleshoot problems without traveling to the test site.
Solutions
After evaluating available technologies, MRI decided to replace the pilot unit's existing microprocessor with an Allen-Bradley MicroLogix 1400 programmable logic controller (PLC) from Rockwell Automation. The MicroLogix controller provided MRI with the critical features needed, including online editing, a built-in LCD and an embedded EtherNet/IP port, along with two serial ports for expanded communication capability.
The controller incorporates data-logging capabilities that help users capture operational and flow data from the test skid at precise intervals throughout the day. It also provides high-performance data collection and easy connectivity to an EtherNet/IP network for seamless data transfer.
As part of the upgrade, MRI replaced the pilot unit's one horsepower DC motor and drive with a 230 three-phase AC motor and an Allen-Bradley PowerFlex 4 drive. The PowerFlex drive converts single-phase electrical power into three-phases, eliminating the need for MRI to change the single-phase power requirements.
"Choosing Rockwell Automation made complete sense for us, because it allowed us to create a more integrated system that's easier to operate, configure and maintain," said Don Bersell, project manager, MRI. "Also crucial were the design and configuration tools that came along with the Rockwell Automation products, including the Connected Components Building Blocks, which have proven to be a tremendous timesaver."
The Building Blocks DVD includes pre-written blocks of application code for the PLC that can be modified to help meet the precise needs of the machine, pre-designed HMI screens to ease operator interface set up, and pre-configured drive parameter files that take the strain out of implementing speed control tasks. The easy access to information eliminated the need for engineers to refer to multiple vendor manuals, saving valuable configuration time and reducing tedious prep work.
To deliver the remote monitoring and data acquisition capabilities needed for the system, MRI added an AirLink cellular modem provided by Rockwell Automation Encompass partner Sierra Wireless. Now, by providing customers with an IP address, MRI engineers can monitor the real-time status of the pilot unit from anywhere in the world. MRI also set up a continuous data logging stream on a server at its main facility. This allows engineers to generate detailed electronic performance and quality reports that can be emailed to the customer to give them ongoing updates of the plate settler performance.
MRI also was able to replace numerous buttons and switches by equipping the pilot unit with an Allen-Bradley PanelView Component 600 touch-screen operator interface, allowing operators to easily monitor critical system functions. MRI also employed a wide range of Allen-Bradley industrial control components, including terminal blocks, relays and power supplies.
Results
Ease of integration and interoperability of the Rockwell Automation control components have helped provide MRI with a more reliable, cost-efficient pilot unit. The new control platform also gives MRI greater configuration flexibility, including the ability to integrate turbidity meters and chemical dosing pumps into the control system.
"We're now able to more precisely pace the speed of the pumps during turbidity spiles, which provides more even flows and better efficiency," Bersell said. "We also can change the frequency of sludge collection, and alter the speed and mixing energy of the flocculator for a more optimized treatment process. This can all be done remotely now."
The remote-monitoring capabilities provide MRI's customers with faster troubleshooting and more dependable operation, while helping MRI reduce its support costs. In addition, MRI estimates that the Rockwell Automation configuration tools helped reduce design time by approximately 30 to 40 percent. MRI anticipates that savings will be compounded as it upgrades remaining pilot units with the new control technology.
"The plug-and-play features of the Rockwell Automation components made manufacturing and testing much quicker and less complex than the previous system," Bersell said. "The new system is easier to start up and train operators… we are very pleased with this pilot system and have already begun upgrading our other pilot units with the same reliable controls."
In addition to pilot units, Meurer also recently decided to standardize on Rockwell Automation controls for all plate settler production units as well, providing additional engineering and design cost savings with each new system.
Featured Product
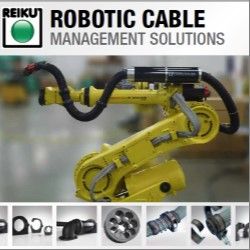
REIKU's Cable Saver™ - The Most Versatile Modular Robotic Cable Management Solution
REIKU's Cable Saver™ Solution eliminates downtime, loss of revenue, expensive cable and hose replacement costs, maintenance labor costs. It's available in three sizes 36, 52 and 70 mm.
All of the robots cables and hoses are protected when routed through the Cable Saver™ corrugated tubing.The Cable Saver™ uses a spring retraction system housed inside the Energy Tube™ to keep this service loop out of harms way in safe location at the rear of the Robot when not required. The Cable Saver™ is a COMPLETE solution for any make or model of robot. It installs quickly-on either side of the robot and has been tested to resist over 15 million repetitive cycles.
REIKU is committed to providing the most modular, effective options for ensuring your robotic components operate without downtime due to cable management.
www.CableSaver.com